Choosing the right aluminum pipe welding gun is crucial for successful welding projects. Different welding techniques, project complexities, and material characteristics necessitate specific types of welding guns. This article explores the factors influencing this choice. Aluminum pipe welding demands precision and the use of appropriate tools due to the metal’s unique properties, such as a lower melting point and higher thermal conductivity. To address challenges like warping and oxidized layers, various welding methods like Tungsten Inert Gas (TIG) and Metal Inert Gas (MIG) welding are employed.
Aluminum pipe welding guns are mainly used
In the realm of aluminum welding, two types of welding guns are predominantly used: TIG (Tungsten Inert Gas) welding guns and MIG (Metal Inert Gas) welding guns.
TIG Welding Guns: These are typically used for precise, high-quality aluminum welds. TIG welding guns require a highly skilled operator due to the complexity of the process, but they offer exceptional control over the welding variables. This makes them suitable for complex or delicate welding tasks where precision is paramount.
MIG Welding Guns: MIG welding guns are known for their versatility and ease of use, making them a popular choice among beginners and for large-scale projects. While they may not offer the same level of precision as TIG welding guns, MIG guns provide efficient and strong welds, making them suitable for tasks where speed and productivity are important.
Each type of gun has its own set of advantages and considerations, and the choice between them often depends on the specific aluminum welding project at hand. Understanding these types and their applications can help you choose the most suitable welding gun for your needs.
Advantages of Difaferent Aluminum Pipe Welding Guns
Advantages of TIG Welding Guns:
- Precision: TIG welding offers superior precision. It’s ideal for intricate work or when working with thin materials where accuracy is vital.
- Quality: TIG welding creates high-quality welds with less spatter, which means less cleanup work post-welding.
- Versatility: A TIG gun is capable of welding more types of metals than any other process, including aluminum.
Advantages of MIG Welding Guns:
- Speed: MIG welding is typically faster, making it ideal for projects that require the welding of large surface areas.
- Ease of use: MIG welding guns are easier to handle and require less skill to operate, making them suitable for beginners.
- Efficiency: MIG welding guns are efficient at creating strong welds, making them an excellent choice for projects where strength and durability are required.
Things to Consider When Welding Aluminum
When welding aluminum, there are several key factors that should be taken into account to ensure a successful outcome:
- Cleaning the Aluminum: Aluminum forms an oxidized layer that can hinder the welding process. Therefore, it’s essential to clean the aluminum thoroughly before starting any welding task. This can be done using a wire brush or other specialized cleaning tools.
- Choosing the Right Welding Method: As discussed earlier, both TIG and MIG welding methods have their advantages when working with aluminum. The choice between these methods should be based on the nature of the project, the type of aluminum being used, and the specific requirements of the weld.
- Welding Speed: Aluminum’s high thermal conductivity means it heats up quickly during the welding process. To avoid burning through or warping the material, it’s essential to maintain an appropriate welding speed.
- Selection of Filler Material: The filler material used for welding aluminum should match or be compatible with the material being welded. Incompatible filler material can lead to weak welds and potential failure points.
- Welding Environment: The environment in which the welding is taking place also matters. Aluminum welding should ideally be done in a clean, dry, and well-ventilated area to prevent contamination and ensure safety.
By keeping these factors in mind, welders can improve their chances of achieving strong, high-quality welds when working with aluminum.
Popular welding machine models and their outstanding features
Millermatic 211
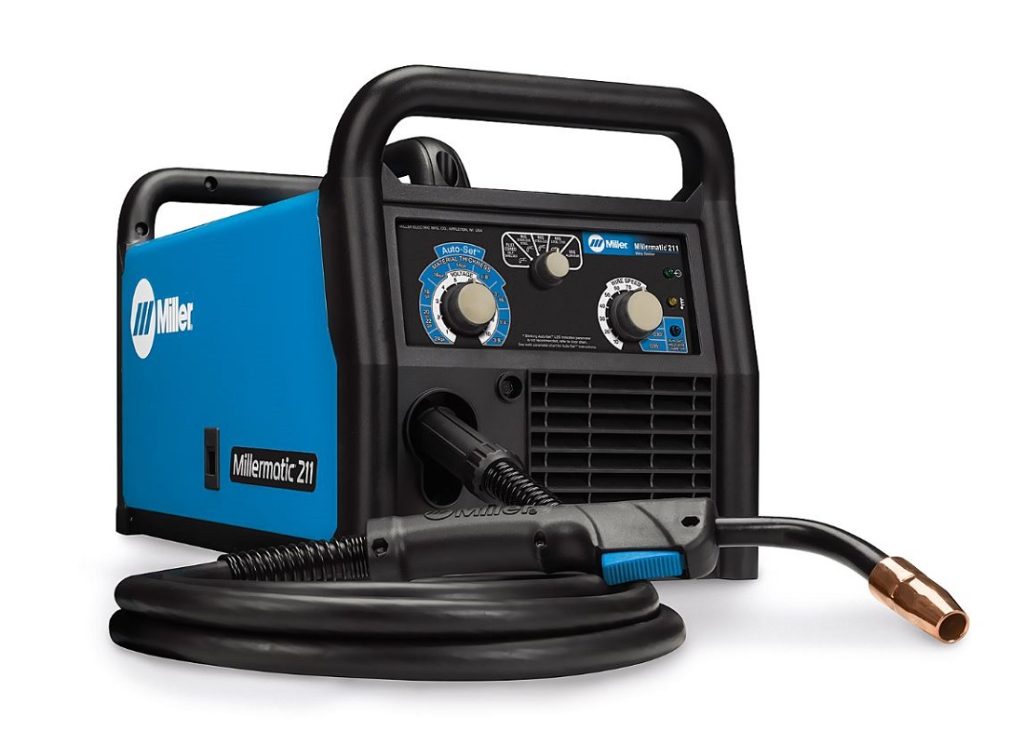
The Millermatic 211 is a versatile MIG welder that is perfect for welding aluminum. It comes equipped with an Auto-Set mode, which allows for easy setup and delivers a smooth and stable arc for quality welds. Its multi-voltage plug adapts to 120V or 240V power supplies, making this model highly portable.
Lincoln PowerMIG 210
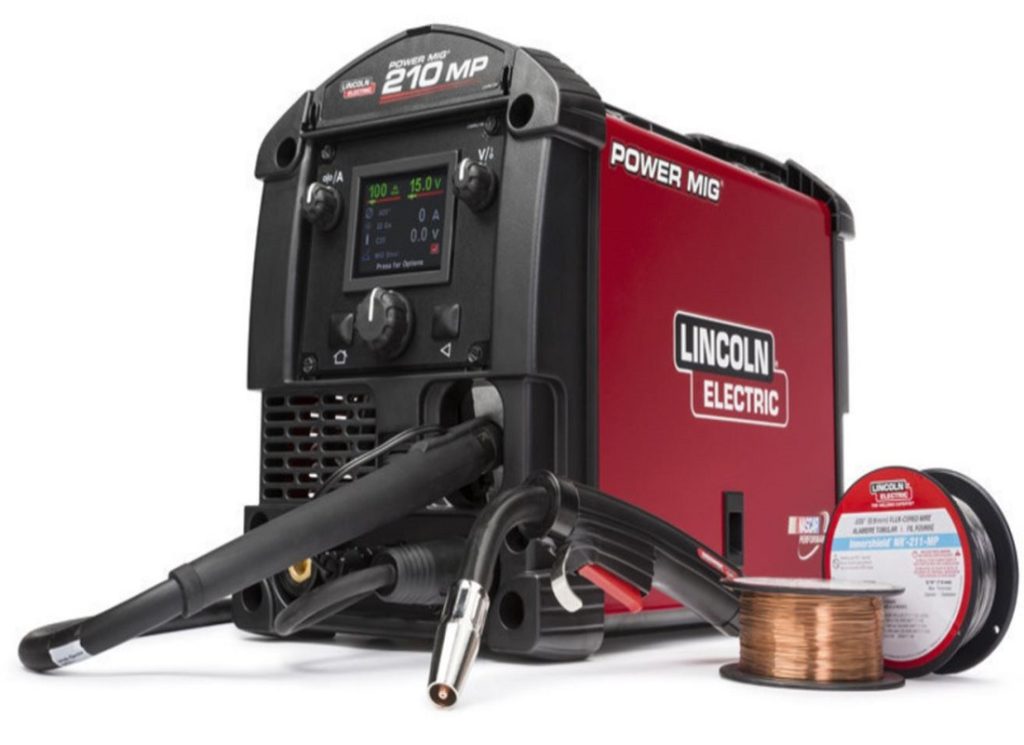
Another popular model, the Lincoln PowerMIG 210, is known for its dual-voltage capability and a user-friendly interface. It can handle aluminum welding using both MIG and TIG processes and offers a broad welding amperage range, making it suitable for a wide variety of welding tasks.
Hobart Handler 210 MVP
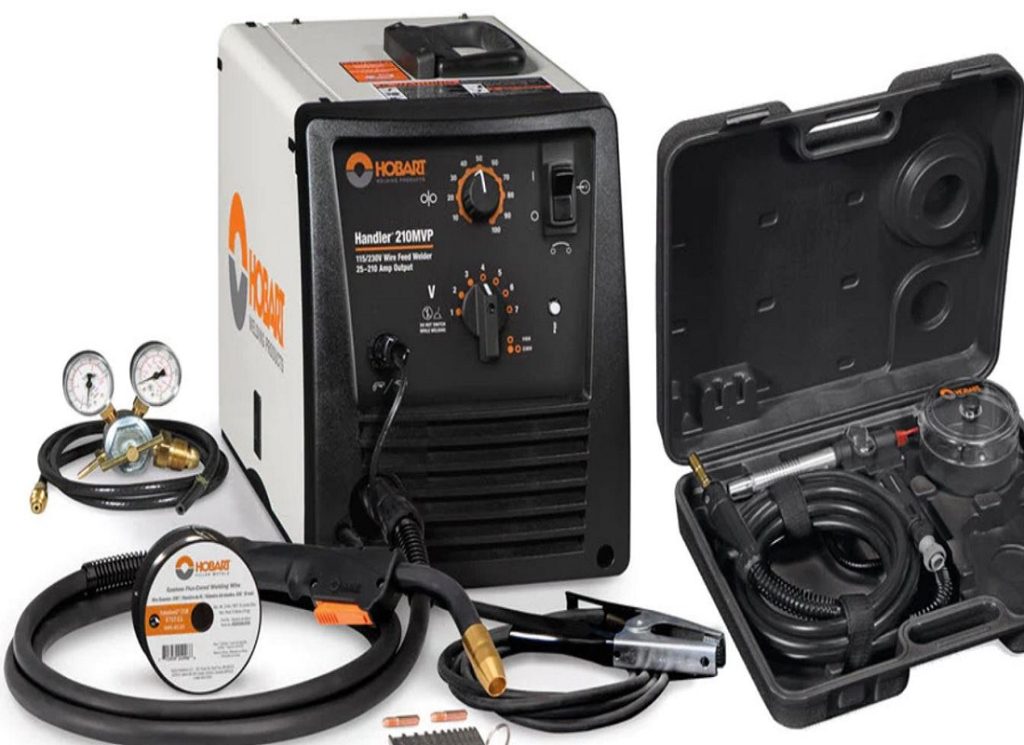
The Hobart Handler 210 MVP is widely appreciated for its power and portability. It can weld aluminum up to 3/8″ thick and offers a 7-setting voltage control for precision welding. This model also includes a dual-voltage plug, making it adaptable to both home and industrial power supplies.
How should your approach to TIG welding be adjusted?
TIG welding aluminum requires a more refined technique compared to other forms of welding, but it can yield excellent results with practice. The tailoring of this approach comes down to understanding the unique characteristics of aluminum and how it responds to heat.
Aluminum conducts heat quickly and has a low melting point, which makes maintaining the right temperature crucial during the TIG process. You’ll find that the use of a foot pedal control can greatly help manage the current and thereby control the heat input.
The choice of filler material is also essential. In most cases, you’ll want to use a filler that’s the same grade as the base material. If that’s not available, a filler that’s one grade softer can also work. It’s also crucial to remember that TIG welding works best on clean surfaces, so pre-cleaning the aluminum is a must.
Finally, practicing your technique is paramount in TIG welding. Aim for a consistent travel speed and try to maintain a steady hand. With time and practice, you can master the art of TIG welding, producing high-quality, aesthetically pleasing welds on your aluminum workpieces.
Advantages of Using Aluminum in Welding
1. Lightweight: Aluminum is significantly lighter than other commonly used metals, which makes the final product easier to handle and reduces transportation costs.
2. Corrosion Resistance: Aluminum forms an oxidized layer when exposed to the environment, which provides natural protection against rust and corrosion, extending the life of the weld.
3. High Strength-to-Weight Ratio: Despite its lightweight nature, aluminum exhibits a high strength-to-weight ratio, making it an ideal choice for applications where strength without added weight is preferred.
4. Excellent Conductivity: Aluminum is an excellent conductor of heat and electricity, making it an ideal choice for applications requiring such properties.
5. Aesthetics: Aluminum welds, especially those done with TIG welding, can be aesthetically pleasing due to their shiny, clean appearance. This can be a significant advantage in applications where the visual appeal of the weld is crucial.
Remember, these advantages can be maximized by selecting the appropriate welding process and technique based on the nature of your aluminum welding project.
Things to Consider When Welding Aluminum
When welding aluminum, it’s imperative to consider various factors to ensure a successful outcome.
- Preparation: The preparation phase is critical when dealing with aluminum. This metal is prone to oxidation, forming an oxide layer on its surface that can interfere with the welding process. To counter this, it’s important to clean the aluminum thoroughly before welding, using either a wire brush or a dedicated cleaning solution.
- Selecting the Right Process and Equipment: Both TIG and MIG welding can be suitable for aluminum, but each comes with its own set of considerations. TIG welding offers greater precision and quality, but it can be more difficult and time-consuming. MIG welding, on the other hand, is quicker and easier, making it ideal for larger projects or those requiring less detail.
- Filler Material: The selection of the correct filler material is vital. When welding aluminum, it’s usually best to choose a filler alloy that matches the alloy of the base material. If that’s not possible, a filler alloy that’s one grade softer can also be effective.
- Welding Speed: Aluminum’s high heat conductivity necessitates careful control of the welding speed. Too fast, and the weld may not penetrate deeply enough; too slow, and you may cause burn-through.
- Environment: Finally, the environment can significantly impact the success of the welding process. Welding should ideally be done in a clean, dry, and well-ventilated environment to minimize contamination and ensure safety.
By taking these considerations into account, it’s possible to achieve strong and durable welds when working with aluminum.
Popular models and their features
AHP AlphaTIG 200X
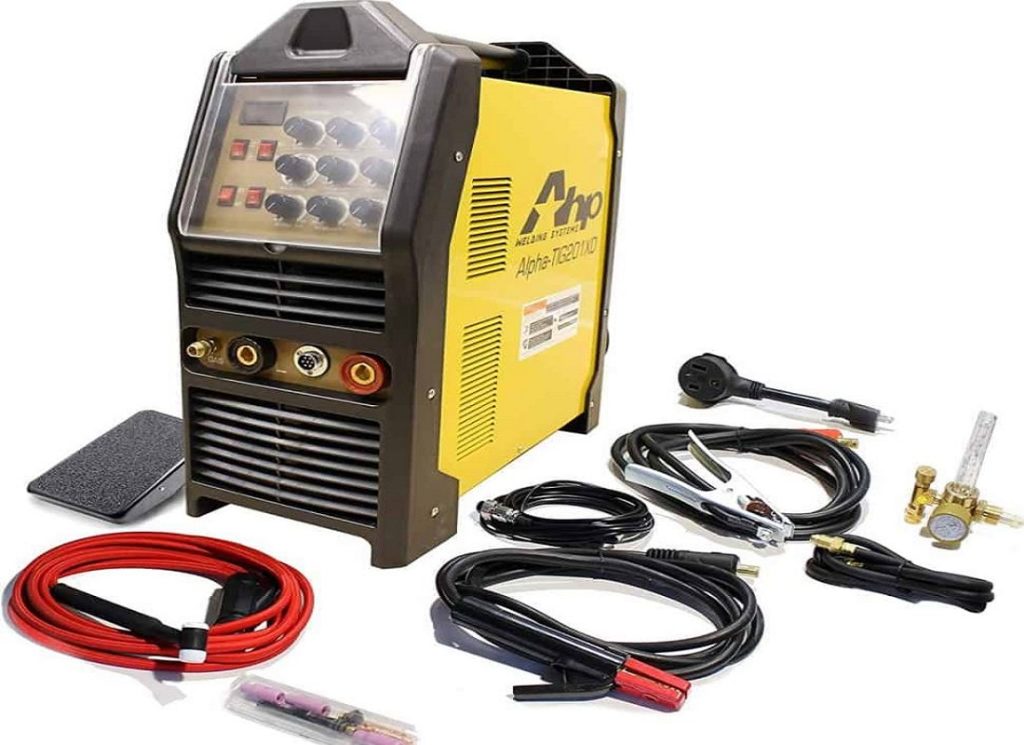
Renowned for its precision and control, the AHP AlphaTIG 200X is a popular choice for aluminum TIG welding. It offers a wide range of amperage control, allowing for intricate and precise welds on thinner materials. It’s also equipped with an advanced inverter technology with pulse width modulation (PWM), enhancing the quality of the welds.
Everlast PowerTIG 255 EXT
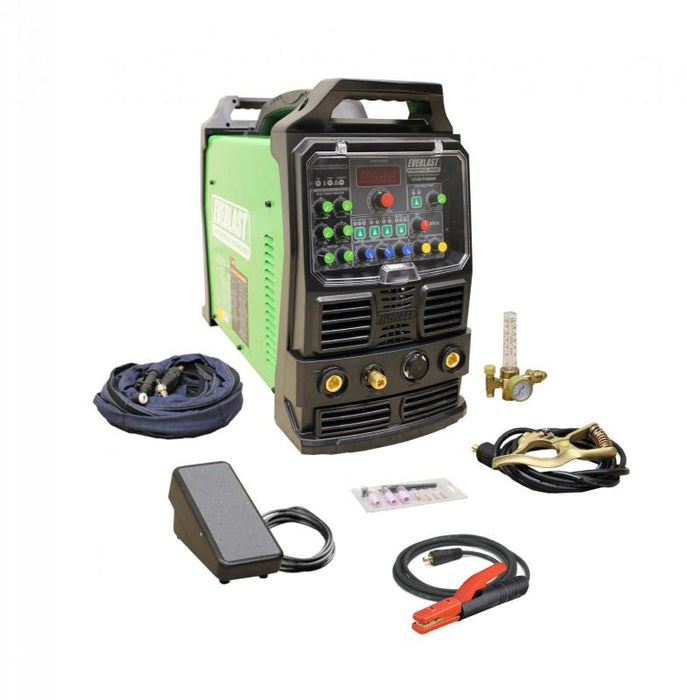
The Everlast PowerTIG 255 EXT is known for its reliability and power. It provides both AC and DC TIG welding capabilities, making it versatile and suitable for a variety of applications, including aluminum welding. Its digital IGBT inverter design allows for precise control over the welding parameters, ensuring high-quality welds.
Lincoln Electric Square Wave TIG 200
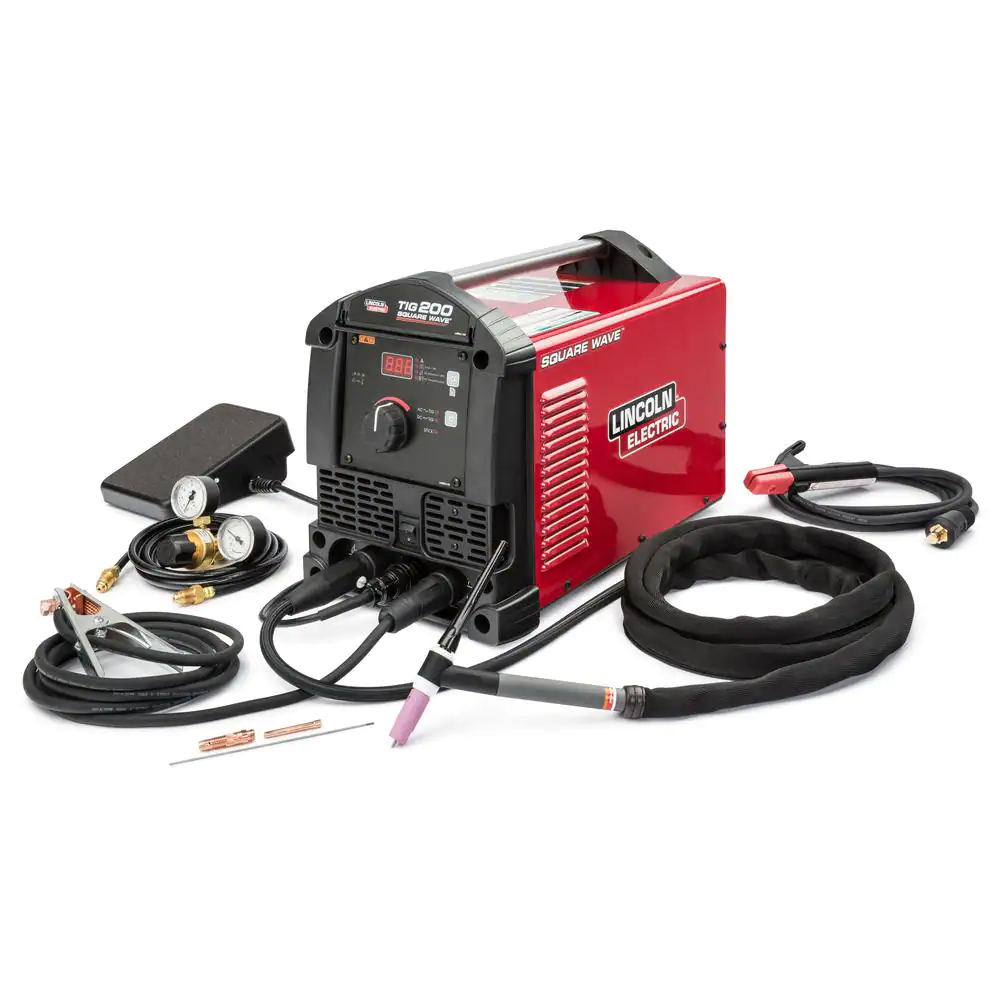
The Lincoln Electric Square Wave TIG 200 is ideal for hobbyists and small businesses. Despite its compact design, it’s packed with features, including AC/DC TIG and stick welding capabilities. It’s recognized for its intuitive user interface, making it easier for beginners to get started. Its advanced features, such as the adjustable AC frequency and balance control, provide excellent control over the welding process, making it a great choice for aluminum welding.
Each of these TIG welders offers unique advantages and features, and the choice among them would depend on the specific requirements of your welding project.
Stick Welding Gun
A stick welding gun, also known as a stinger, is a key component in the Shielded Metal Arc Welding (SMAW) or stick welding process. It is responsible for holding the electrode and transferring the required current to it. The gun’s design typically includes an insulated handle for the welder to safely hold during the welding process and a clamping device to securely hold the electrode and ensure reliable conductive contact.
Choosing a stick welding gun with an ergonomic design can enhance welder comfort and control, thereby increasing the overall quality of the weld. It’s also essential to consider the amperage capacity of the gun to ensure it is suitable for the welding tasks at hand. Understanding the specific features and functionalities of your stick welding gun can help maximize efficiency and ensure safety during the welding process.
Hobart Handler 210MVP
The Hobart Handler 210MVP is a versatile and powerful MIG welder, ideal for welding aluminum. It offers both 115V and 230V operation, allowing you to weld from nearly anywhere. With its 7 voltage selections, enhanced magnetics, and infinite wire feed speed control, it offers the flexibility and control needed for aluminum welding. The welder also comes with a dual-groove quick-change drive roll, making it easy to switch between .023/.025 in. (0.6 mm) and .030 – .035 in. (0.8 – 0.9 mm) wire. The Hobart Handler is easy to set up and use, making it a great choice for beginners and professionals alike.
Considerations and Limitations
While welding equipment like the AHP AlphaTIG 200X, Everlast PowerTIG 255 EXT, Lincoln Electric Square Wave TIG 200, and Hobart Handler 210MVP provides myriad benefits, it’s crucial to be aware of some considerations and potential limitations.
- Learning Curve: Both TIG and MIG welding techniques have a steep learning curve, especially for beginners. Proper mastery requires significant practice and training.
- Cost: High-quality welding equipment can be costly. While investing in such equipment can provide long-term benefits, the initial cost may be prohibitive for hobbyists or smaller businesses.
- Maintenance: Regular maintenance is necessary to ensure the longevity and optimum performance of the equipment. Negligence in this regard can lead to decreased efficiency and eventual breakdown.
- Safety Concerns: Welding can be hazardous if proper safety measures are not taken. This includes using appropriate personal protective equipment (PPE) and ensuring adequate ventilation.
- Limitations in Material Thickness: While these models are versatile, they may not be suitable for welding exceptionally thick or thin materials. It’s essential to understand the equipment’s limitations to avoid sub-optimal results.
- Power Requirements: These welding machines require substantial power to operate. Ensure you have a suitable power source and consider the potential impact on your energy bills.
Taking these considerations into account can assist you in making an informed decision and optimally utilizing your welding equipment.
Recommended Models for Aluminum Welding
Miller Multimatic 220 AC/DC
For those seeking versatility, the Miller Multimatic 220 AC/DC is an excellent choice. It offers MIG, TIG, and Stick welding capabilities and features Auto-Set Elite technology to simplify setting control. This welder is known for its superior arc quality and has AC TIG capabilities for aluminum welding.
Hobart Handler 210MVP
The Hobart Handler 210MVP is a highly recommended model for those focused on MIG welding. It offers dual voltage capabilities, allowing for greater flexibility. This welder also features an easy-to-use interface, making it ideal for beginners.
ESAB Rebel EMP 205ic AC/DC
The ESAB Rebel EMP 205ic AC/DC welder offers the full range of welding modes – MIG, Flux-Cored, Stick, and AC/DC TIG. It stands out for its innovative Smart MIG feature that adapts to the operator’s welding technique. This model is also praised for its portability and durability.
Deciding on the right model will depend on your specific welding needs, budget, and skill level. Each of the recommended models has its strengths and is well-regarded in the welding community for its performance and reliability.
What factors should be kept in mind when choosing welding gun?
When selecting a welding gun, there are several key factors to consider that directly influence the efficiency, comfort, and outcome of your welding tasks:
- Type of Welding: The first factor to consider is the type of welding you will be doing. Different welding processes, such as MIG, TIG, or Stick, require different types of guns.
- Amperage: The welding gun should have the appropriate amperage rating for your tasks. A lower amperage gun is suitable for lighter tasks, while a higher amperage is necessary for heavier applications.
- Durability: The gun should be robust and durable to withstand the rigors of welding, especially for frequent use or industrial applications.
- Ergonomics: Comfort is crucial for precision and long-term use. Look for a welding gun with an ergonomic design that is comfortable to hold for extended periods.
- Cable Length: Depending on your workspace, you may need a longer or shorter cable. A longer cable provides more flexibility, but can also be harder to manage.
- Consumables: Consider the type and cost of consumables that the gun requires. Some guns may use less expensive consumables, but they may not last as long.
- Price: While it’s not always the case, the price can sometimes reflect the quality of the welding gun. However, it’s important to balance cost with the other factors mentioned.
Remember, the right welding gun for your needs will depend on a combination of these factors. It’s crucial to assess all aspects before making your choice.
Learn about the impact of material thickness in welding
The thickness of the material you intend to weld significantly impacts the process and outcome of welding tasks. Different thicknesses require different welding techniques and equipment capabilities.
For instance, thin materials risk warping or burning through when using a welding process that delivers too much heat, such as MIG welding. Delicate processes like TIG welding are better suited for thin materials as they offer the welder greater control and generate less heat.
Conversely, welding thick materials necessitates a process that can deliver a deep, penetrating weld. MIG and Stick welding can be used for these heavier tasks. Keep in mind that the welder’s power output, measured in amperage, also plays a vital role here. Higher amperage welders can handle thicker materials.
In the context of the models mentioned above, Hobart Handler 210MVP and ESAB Rebel EMP 205ic AC/DC have robust power outputs that can handle thicker materials, while the Miller Multimatic 220 AC/DC, with its AC TIG capabilities, can proficiently handle thinner materials, especially aluminum.
Understanding the material thickness you most often work with will guide you in selecting the appropriate welding process and equipment.
Learn about welding positions
The position of the workpiece during welding plays a significant role in the process, influencing the difficulty of the task and the quality of the weld. There are four main welding positions: flat, horizontal, vertical, and overhead.
- Flat Position: Also known as the downhand position, this is the easiest position in which to weld and typically yields the highest quality welds. The workpiece is flat, and the welder performs the weld on top of it.
- Horizontal Position: In horizontal welding, the workpiece is positioned so that the weld forms on a vertical surface that runs horizontally. This position requires more skill than flat welding, as the welder must counteract the effect of gravity.
- Vertical Position: Vertical welding is more challenging still. The welder operates on a surface that runs vertically and must weld from bottom to top or top to bottom. Careful control is required to prevent the molten weld pool from sagging or dropping.
- Overhead Position: The most challenging position is overhead welding, where the welder performs the weld on the underside of a horizontal surface. This position requires significant skill and control, and safety is a particular concern due to the risk of molten metal falling.
Each of these positions demands different techniques and settings. Therefore, understanding and practicing welding in various positions will make you a more versatile welder and open up a broader range of projects.
Compatibility with Power Supply
An often overlooked but crucial factor to consider when choosing a welding machine is its compatibility with your power supply. Welding machines can run on 110V or 220V power outlets, with some versatile machines capable of operating on both.
If you’re mainly going to be using your welder for small home projects or in a space with limited power supply, a 110V welder might suffice. However, for heavy-duty welding or industrial use, you’ll want a welder that can run on 220V for increased power and performance.
The Hobart Handler 210MVP and the ESAB Rebel EMP 205ic AC/DC mentioned above are examples of multi-voltage welders, offering you the flexibility to switch between power supplies as needed. Conversely, ensure you have a compatible power outlet or a reliable adapter if you choose a welder with a fixed voltage.
Remember, the correct power supply not only ensures your welder operates efficiently but also contributes to safety in the workspace. Always double-check the power requirements of your chosen welder and ensure it matches your power source before purchasing.
Understand the concept of workflow
Work cycle, often referred to as the duty cycle, is a critical factor in selecting a welding machine. The duty cycle is a measure of how long a welder can operate at a particular output in a ten-minute period without overheating. For instance, if a welder has a duty cycle of 30% at 150 amps, it means the welder can run continuously at 150 amps for three minutes out of every ten-minute period. After that, it would need to cool down for seven minutes to prevent overheating.
Choosing a welder with a high duty cycle can provide more extended periods of continuous operation, which is particularly beneficial for industrial applications or large projects. However, for smaller, occasional tasks, a lower duty cycle may be sufficient, and these welders often come at a lower price point. Thus, understanding the work cycle concept will help you choose a welder that best suits your usage pattern and budget.
Factors Influencing Welding Machine Selection
When selecting a welding machine, considering its ease of use and ergonomics can significantly impact your welding experience. Welding machines vary in terms of user interface, control layout, and physical design, all of which can either simplify or complicate the welding process.
A user-friendly interface with clear control settings can make it easier to adjust your welding parameters accurately. Some welding machines even offer advanced features like auto-set controls, which automatically configure the correct welding parameters based on your input, making the process more straightforward for beginners.
Ergonomics refers to the physical design and how comfortable the welding machine is to handle and operate. Things to consider include the weight of the machine, the design of the handle, and the length of the power cord and welding leads. Lightweight machines with well-designed handles can reduce user fatigue, especially during long welding sessions, while longer cords and leads offer greater flexibility and range of movement.
Remember, a machine that feels comfortable and intuitive to use can enhance your productivity and result in higher quality welds. Therefore, it’s always a good idea to try out different models and choose a welder that fits well with your comfort and usability preferences.
Budget Considerations and Pre-Purchase Notes for Welding Machines
Your budget plays a crucial role in selecting the right welding machine. Welding machines come in a wide range of prices, with varying features, capabilities, and power requirements. Bear in mind, though, that the most expensive welder isn’t necessarily the best one for your needs.
For beginners and hobbyists, a basic, user-friendly, and cost-effective machine might be the most suitable choice. These machines typically have fewer features but are easy to use and perfect for simple projects.
On the other hand, professional welders or those who frequently undertake large scale projects may need a high-end welding machine with advanced features and capabilities. While these machines come with a higher price tag, the investment can be worthwhile for the power, performance, and durability they offer.
Consider how frequently you’ll be using the machine and the complexity of your welding tasks. It’s worth investing in a higher quality machine if you’ll be using it regularly or for complex tasks. However, if you’re only going to be using it occasionally for straightforward projects, a more affordable option might be more cost-effective. Remember that it’s not just about the initial investment. Consider other costs like maintenance, power consumption, and welding consumables when setting your budget.
Best advice for welding aluminum pipes
Welding aluminum pipes presents unique challenges due to the metal’s properties. Here are some key tips to consider:
- Use appropriate welding methods: TIG (Tungsten Inert Gas) welding is typically preferred for welding aluminum due to its precision and clean welds. However, MIG (Metal Inert Gas) welding can also be used for thicker sections.
- Proper preparation: Aluminum oxidizes rapidly when exposed to air. To ensure a clean weld, remove the oxide layer using a stainless steel brush before welding.
- Proper heat management: Aluminum dissipates heat quickly, causing the pipe to warp if not managed correctly. Use a welding technique that allows for proper heat input and distribution.
- Use correct filler material: The filler material should match the type of aluminum being welded. For example, 5356 filler rod is typically used for 6000 series aluminum.
- Practice good welding technique: Maintaining a short, focused arc and moving at a steady, even pace will help create a clean, consistent weld.
Remember, practice is essential in mastering aluminum welding. Don’t be discouraged if your initial attempts aren’t perfect. Keep refining your technique, and you’ll improve over time.
Evaluate and view lightning after welding
The post-welding review is a critical stage in any welding project. It involves inspecting the weld to ensure its quality and safety. This review can be accomplished through various methods, including visual examination, destructive testing, and non-destructive testing.
Visual Examination: This is the most basic, yet essential form of weld inspection. It involves checking the surface of the weld for any obvious defects such as cracks, porosity, or inadequate penetration. The shape and size of the weld bead can also provide useful information about the quality of the weld.
Destructive Testing: This involves physically breaking the weld to examine its internal structure. Methods such as bend testing or tensile testing can reveal defects that are not visible on the surface. However, destructive testing, as the name implies, destroys the weld, so it’s mostly used for test samples rather than the final product.
Non-Destructive Testing: These methods are used to inspect the weld without damaging it. Techniques include ultrasonic testing, radiographic testing, and magnetic particle testing. These can reveal internal and surface defects, but they require special equipment and training.
Always remember, reviewing your work post-welding is as important as the welding process itself. It’s a step that ensures the integrity, quality, and safety of your welds. Moreover, it provides a learning opportunity to identify and rectify any mistakes, thereby improving your future welding projects.
Conclusion
In conclusion, welding is a skill that requires knowledge, practice, and attention to detail. Various factors need to be considered, from choosing the right welding machine and understanding its functionalities to mastering various welding techniques and conducting post-welding reviews. Welding aluminum requires specific techniques and practices, like using appropriate welding methods, proper preparation, heat management, and selecting the correct filler material.
Leave a Reply