Welding plays a vital role in numerous industries, requiring precision, consistency, and safety. The selection and use of appropriate AWG (American Welding & Gas) gases and welding supplies are paramount to achieve these objectives. These supplies not only determine the quality of the weld but also affect worker safety and productivity. The selection should be based on factors like the type of metal being welded, the welding process being used, and the desired finish. This guide will provide insights into how to choose and use AWG gases and welding supplies effectively in the welding industry.
Types of AWG Welding Gases and Their Uses
There are several types of AWG welding gases, each with unique properties that make them suitable for specific welding processes and materials.
Characteristics and Applications of Common AWG Welding Gases
There are several types of AWG welding gases, each with unique characteristics and applications. The two commonly used gases are Argon and Carbon Dioxide. Argon, an inert gas, provides superior control of the welding arc and puddle and is often used for TIG welding. On the other hand, Carbon Dioxide is an active gas and is typically used in MIG welding. It’s cheaper than Argon but doesn’t offer the same level of control and can lead to a more spattered weld.
Comparing Different Types of Gases
When it comes to choosing the right welding gas, it’s crucial to understand the differences and how they affect your specific needs. As mentioned, Argon offers greater control and results in cleaner welds, making it an excellent choice for fine or detailed work. However, it’s more expensive. Carbon Dioxide, while less precise, is more economical and suitable for general welding tasks. The choice between these gases, therefore, depends on the precision required, budget considerations, as well as the type of metal being welded.
Choosing Welding Supplies
Selecting the right welding supplies is a critical step in ensuring the success of your welding project. The choice should align with your specific project requirements, objectives, and safety standards.
Aligning Welding Supplies with Projects and Goals
Every welding task demands different supplies. For instance, TIG (Tungsten Inert Gas) welding requires a tungsten electrode, whereas MIG (Metal Inert Gas) welding uses a wire-feed. Besides, the project’s scale, desired finish, and metal type also influence the selection. It’s essential to research and understand the specifications of your project thoroughly. Consulting with industry professionals or trusted vendors can provide valuable insights into making appropriate choices.
Quality Standards and Safety Measures
Ensuring the quality and safety of your welding supplies is critical. Always choose supplies that meet or exceed the industry’s quality standards. Check for regulatory certifications on the products, which prove they have passed rigorous testing and adhere to safety norms. Remember, using substandard supplies can compromise the weld’s strength and durability, leading to potential safety risks. Moreover, personal protective equipment, including welding helmets, gloves, and jackets, should be of high quality to provide the necessary safety during welding operations. Regular inspection and maintenance of the supplies are also vital to sustain their performance and safety.
Overview of AWG gases that you should pay attention to
AWG gases are integral to the welding process, influencing the quality of welds and worker safety. Understanding their technical specifications, advantages, and disadvantages can help make informed decisions in their selection and use.
Technical Specifications
- 1. Argon (Ar)
Argon is a colorless, odorless, tasteless, and non-toxic gas. It has a density of 1.784 grams per liter at standard conditions. Argon’s ionization energy is 15.76 eV, and it has a thermal conductivity of 0.01772 W/m.K.
- 2. Carbon Dioxide (CO2)
Carbon Dioxide is a colorless gas with a slight acidic odor. It has a density of 1.98 grams per liter at standard conditions. The ionization energy of CO2 is 13.78 eV, and it has a thermal conductivity of 0.01465 W/m.K.
Advantages and Disadvantages
- 1. Argon
Advantages
Argon provides excellent control over the welding arc and puddle. It forms a protective gas shield around the weld area, preventing oxidation. This results in cleaner and higher-quality welds with minimal spatter. Argon is suitable for welding non-ferrous metals and stainless steel, making it versatile for various applications.
Disadvantages
Argon is more expensive than most other welding gases. It also requires careful handling and storage due to its inert nature.
- 2. Carbon Dioxide
Advantages
Carbon Dioxide is more economical than Argon and other gases. It’s also readily available and produces deep weld penetration, making it ideal for welding thicker materials.
Disadvantages
Carbon Dioxide can lead to a more spattered weld and doesn’t offer the same level of control as Argon. It may not be appropriate for welding thin or delicate materials or for detailed work due to the potential for burning or warping.
Recommended welding supplies that you should prepare
Choosing the right welding equipment can substantially influence the quality of your welds and your overall productivity. Below we highlight some essential features and our top recommendations for welding supplies.
Welding Helmets
A welding helmet is a crucial safety tool that protects your eyes and face from radiation and sparks. Look for a helmet with an auto-darkening feature that adjusts to the brightness of the arc, such as the Miller Electric Digital Elite. This helmet offers four independent sensing circuits and provides excellent coverage.
Miller Electric Digital Elite
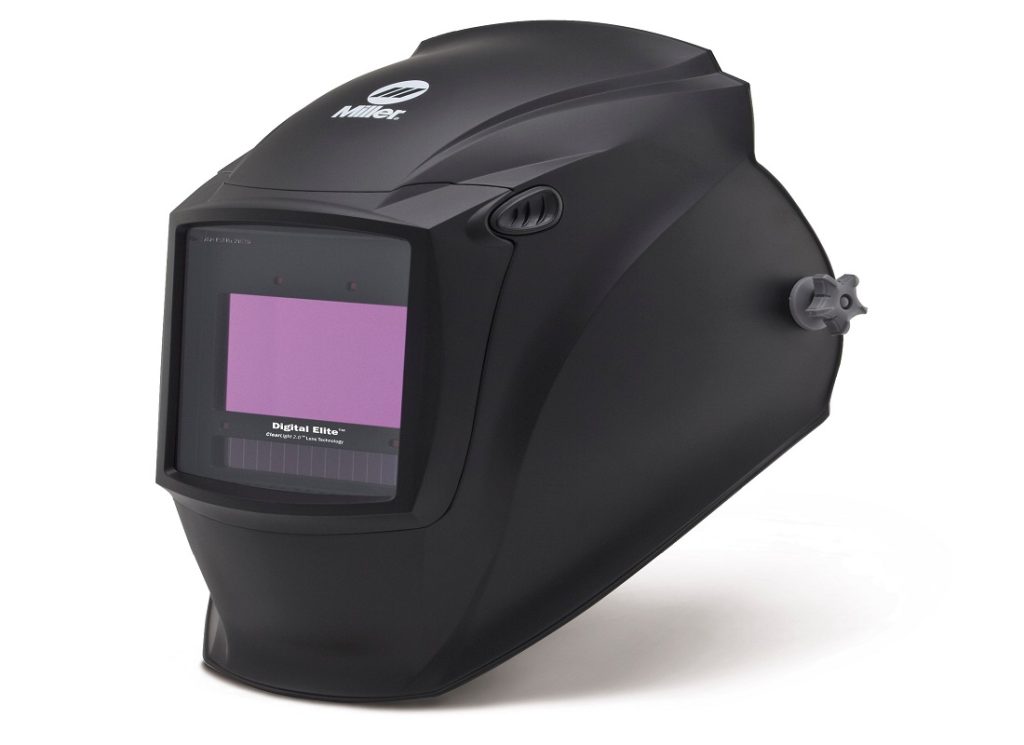
Welding Gloves
Welding gloves should offer both flexibility and protection. Lincoln Electric Traditional MIG/Stick Welding Gloves are a premium choice. Made of heat- and flame-resistant leather, these gloves provide superior comfort and protection.
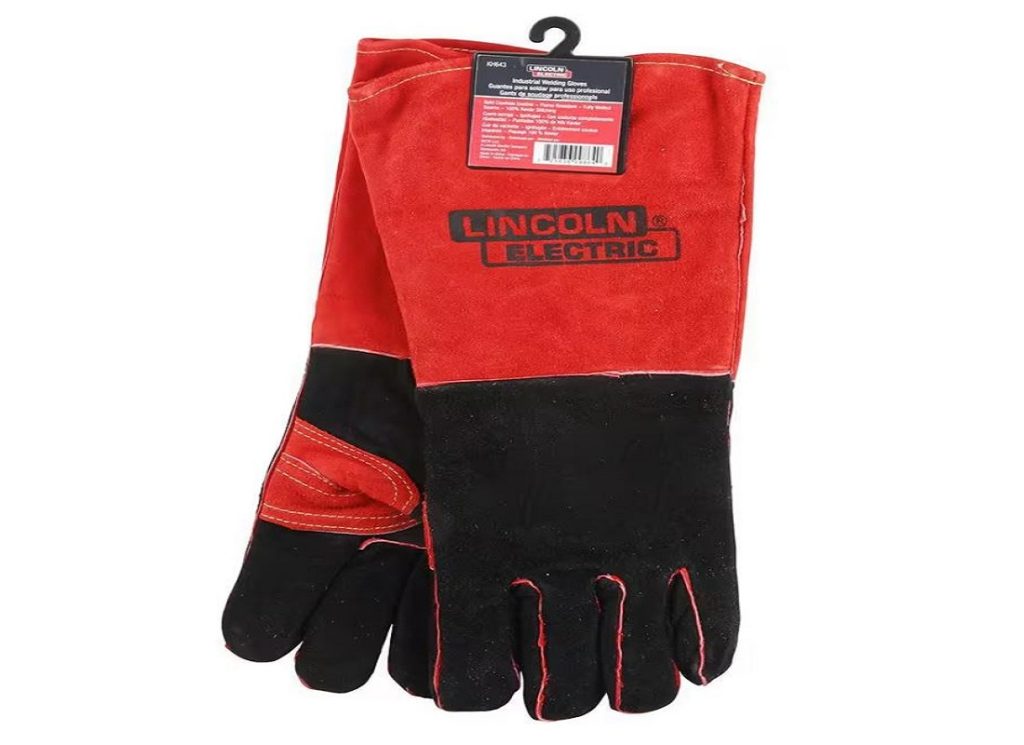
Lincoln Electric Traditional MIG/Stick Welding Gloves
Welding Machines
When it comes to welding machines, consider your welding process, the thickness of the material, and portability. For MIG welding, the Hobart Handler 210 MVP MIG Welder is a powerful and versatile choice.
Hobart Handler 210 MVP MIG Welder
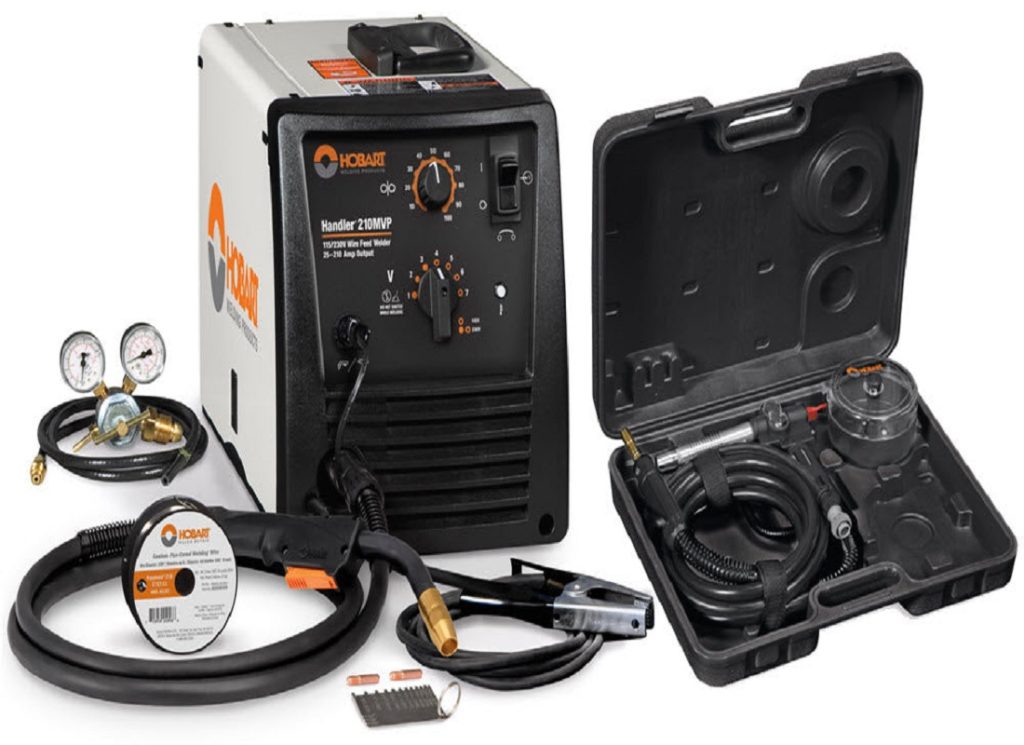
For TIG welding, the Miller Electric Maxstar 150 STL is a compact yet robust option that offers precision and control.
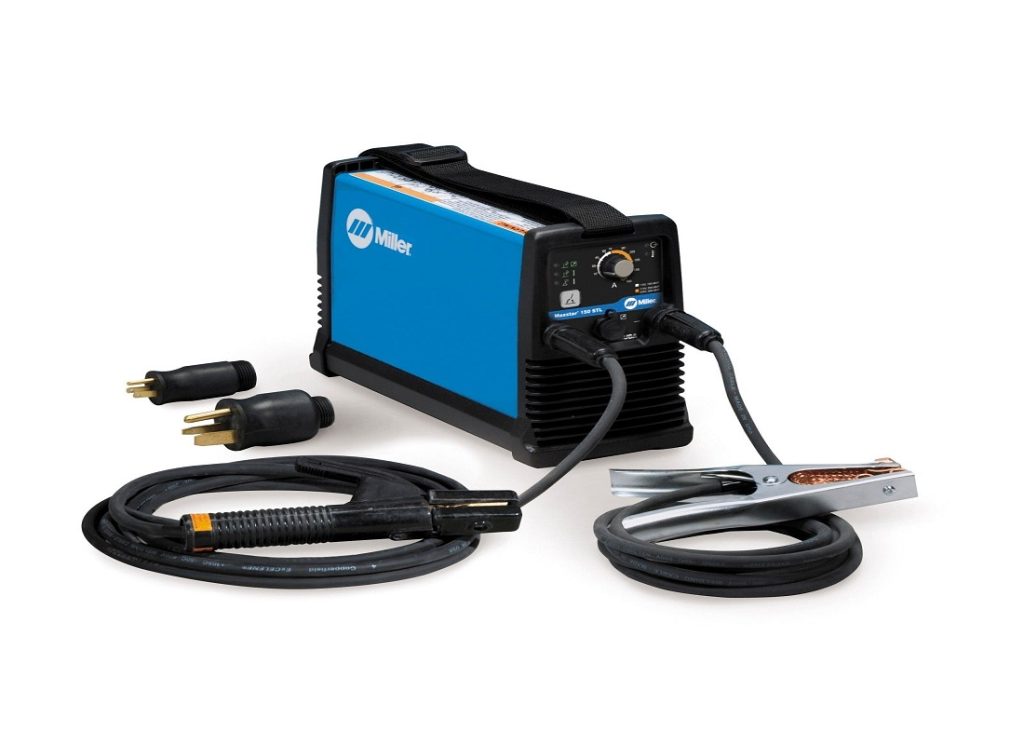
Miller Electric Maxstar 150 STL
Welding Wires
Welding wires should be chosen based on the welding process and the type of metal. For steel welding in MIG processes, we recommend Hobart H305406-R22 10-Pound ER70S-6 Carbon-Steel Solid Welding Wire. This wire provides smooth, consistent welds.
Hobart H305406-R22 10-Pound ER70S-6 Carbon-Steel Solid Welding Wire.
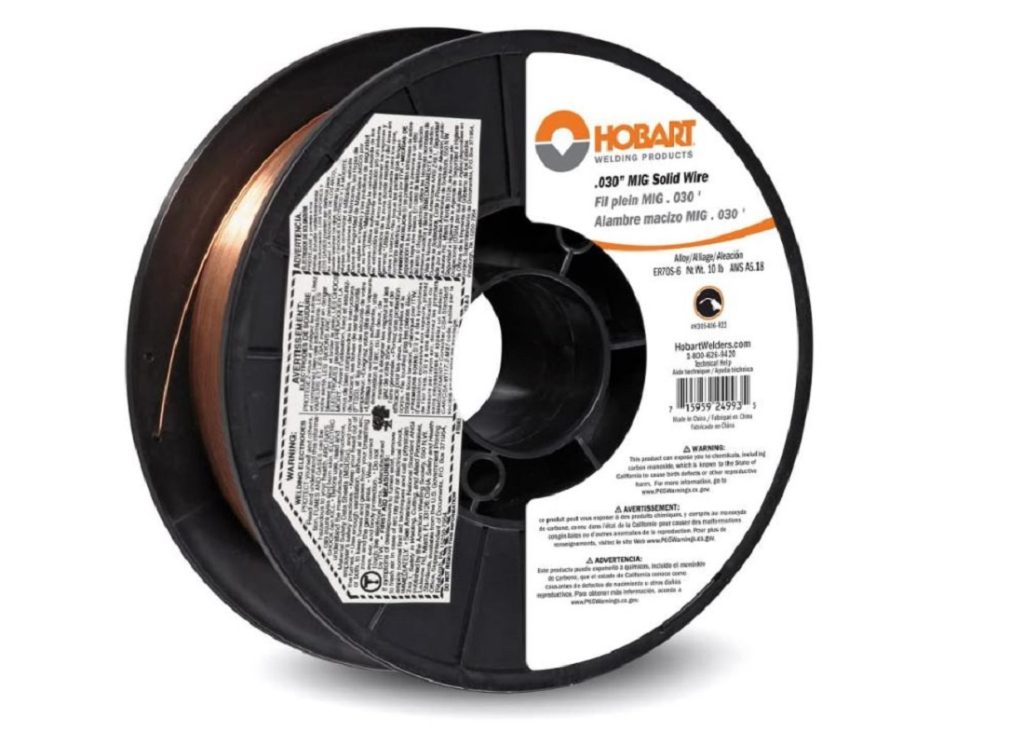
Welding Jackets
A welding jacket protects against heat, sparks, and spatter. The Lincoln Electric Leather Welding Jacket is made from durable, flame-resistant leather and offers excellent mobility and comfort.
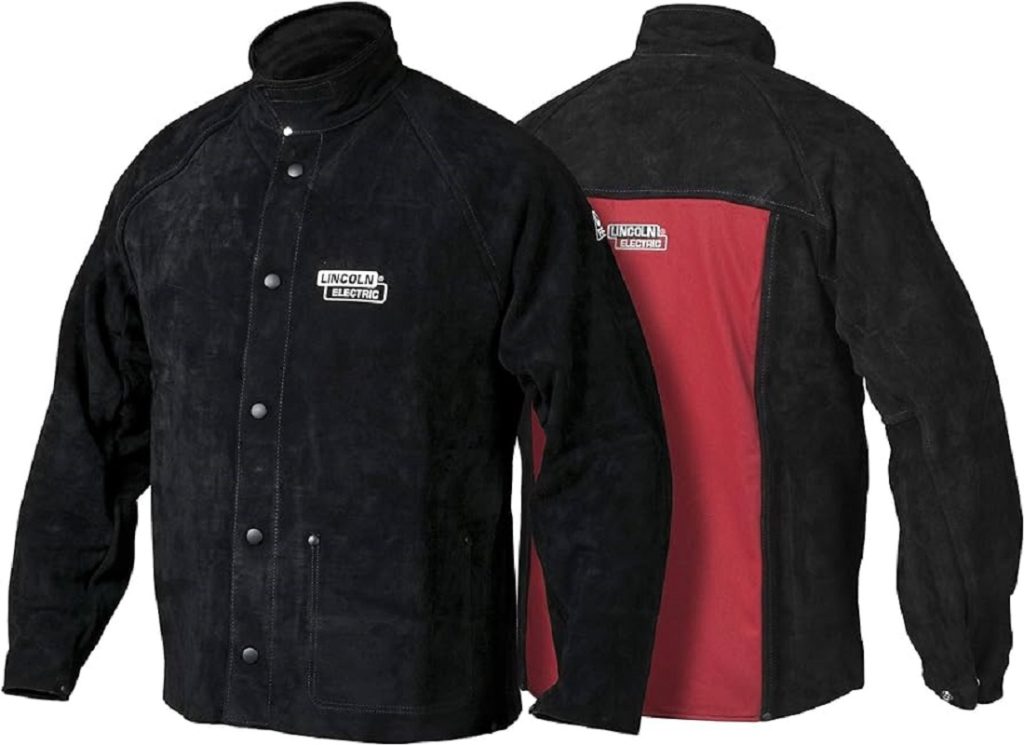
Lincoln Electric Leather Welding Jacket
Remember, the right welding supplies can make a significant difference in the success of your welding projects, ensuring not only exceptional weld quality but also enhanced safety. Always choose products that meet industry standards and suit your specific welding needs.
Proper Use and Storage
Safe and Efficient Use of AWG Gases and Welding Supplies
The correct use of AWG gases and welding equipment is paramount to ensure the integrity of your welding projects and maintain safety. Always follow the manufacturer’s guidelines. Adjust the flow rate of the AWG gases according to the welding process and metal you are working with. When using welding machines, ensure you select the correct settings and use the appropriate welding wire. Always wear your safety gear – welding helmet, gloves, and jacket – whenever you are welding. Regularly inspect these items for any damages and replace them when necessary to maintain their protective function.
Recommendations for Storage of Welding Supplies
Proper storage of welding supplies is essential for their longevity and performance. Store AWG gases in an upright position in a well-ventilated area, away from heat sources and flammable materials. Ensure the gas cylinders are securely fastened to avoid accidental tipping. Welding machines should be kept in a dry, clean place to prevent dust accumulation and moisture damage.
Welding wires should be stored in a sealed container to avoid exposure to humidity, which could lead to rust. Personal protective equipment should be cleaned according to the manufacturer’s instructions and stored in a dry, clean place. Remember, proper care and storage of your welding supplies can significantly extend their service life and ensure they function optimally when you need them.
Some tips you should refer to
As industries continue to strive for faster and more efficient production processes, welding is no exception. Optimizing welding efficiency can result in cost savings, increased productivity, and improved quality of products. Here are some tips to help you optimize your welding process:
- Choose the right welding process: There are several types of welding processes available, including TIG, MIG, and Stick welding. Each process has its own advantages and limitations, so it’s important to choose the right one for your specific application.
- Select the appropriate gas: Welding gases play a crucial role in achieving quality welds and optimizing efficiency. The most common gases used in welding are Argon, CO2, and a mixture of both known as C25. These gases provide shielding and cooling to the welding area, preventing contamination and ensuring proper heat distribution.
- Maintain proper gas flow rate: It’s important to maintain a consistent and appropriate gas flow rate for optimal efficiency. Too little gas can result in poor weld quality, while too much gas can be wasteful and increase costs.
- Use high-quality welding supplies: Using low-quality or outdated welding supplies can significantly impact the efficiency of your welding process. Quality equipment, such as welding torches and nozzles, can improve gas flow and distribution, resulting in better welds.
- Monitor and adjust settings: Regularly monitoring and adjusting your welding settings can help optimize efficiency by ensuring proper gas flow and heat input. This can also prevent overheating, which can lead to weaker and less durable welds.
- Train and educate employees: Proper training and education of welding techniques can greatly improve efficiency. Educating employees on the correct use of equipment, gas flow, and other important factors can result in smoother operations and higher quality products.
In addition to these basic steps, using the right type of gas and welding supplies for the final product’s quality is crucial. For example, using a gas with lower levels of oxygen and nitrogen can result in cleaner and stronger welds. It’s also important to consider the type of metal being welded and its thickness when selecting welding supplies.
Comparison and Selection
Guide on Comparing and Choosing Between Different AWG Gases and Welding Supplies
When comparing different AWG gases and welding supplies, there are a few key factors to consider. Firstly, think about your specific application – different types of welding processes may require different gases. For example, TIG and MIG welding often utilize Argon, while other processes may call for a blend of gases. Ensure to research the compatibility of the gas with your welding technique.
As for welding supplies, consider the quality and reputation of the brands available in the market. Look for manufacturers who are known for producing durable and effective equipment. Read reviews and ask for recommendations from other professionals in the field.
Analyzing Costs and Benefits to Make Informed Decisions
When it comes to costs, it’s important to look beyond just the initial price of the gas or equipment. Consider the long-term implications – a cheaper gas or piece of equipment may end up costing more in the long run if it leads to lower-quality welds or requires frequent replacement.
On the other hand, investing in high-quality gases and welding supplies can result in improved efficiency and better product quality, ultimately saving you money. Therefore, conducting a cost-benefit analysis can help you make an informed decision. This analysis will weigh the cost of the investment against the potential benefits, such as increased productivity, improved quality, and reduced rework.
Conclusion
In summary, grasping the types of AWG welding gases and selecting appropriate supplies are pivotal in welding. Understanding the features and applications of common AWG gases, adhering to quality standards, and ensuring safety are vital for optimal welding performance. Proper usage and storage enhance longevity, while comparing and selecting AWG gases and supplies, considering costs and benefits, facilitates informed decisions. Apply this knowledge in real-world welding scenarios to enhance quality and efficiency, recognizing the crucial impact of the right choice of gases and supplies on the final product.
Leave a Reply