Introduction to the 125 Flux Core Welder
The 125 flux core welder is a versatile and user-friendly welding machine that is well-suited for a wide range of steel welding applications. Compared to traditional stick welding or MIG/MAG welding, the flux core welder offers several key advantages that make it a popular choice among welders.One of the primary benefits of the 125 flux core welder is its ability to weld in any position without the need for shielding gas. This flexibility allows welders to tackle a variety of welding tasks, from fabrication work to on-site repairs, without the added complexity and cost of a gas supply system. Additionally, the initial investment for a flux core welder is generally lower than that of a MIG/MAG setup, making it an accessible option for small workshops, DIY enthusiasts, and professionals alike.Despite its simplicity, the 125 flux core welder is a powerful tool that can produce high-quality welds on a variety of steel materials, including carbon steel, alloy steel, and stainless steel. By understanding the proper setup, welding techniques, and maintenance procedures, users can leverage the full potential of this versatile machine to tackle a variety of welding projects with confidence and efficiency.
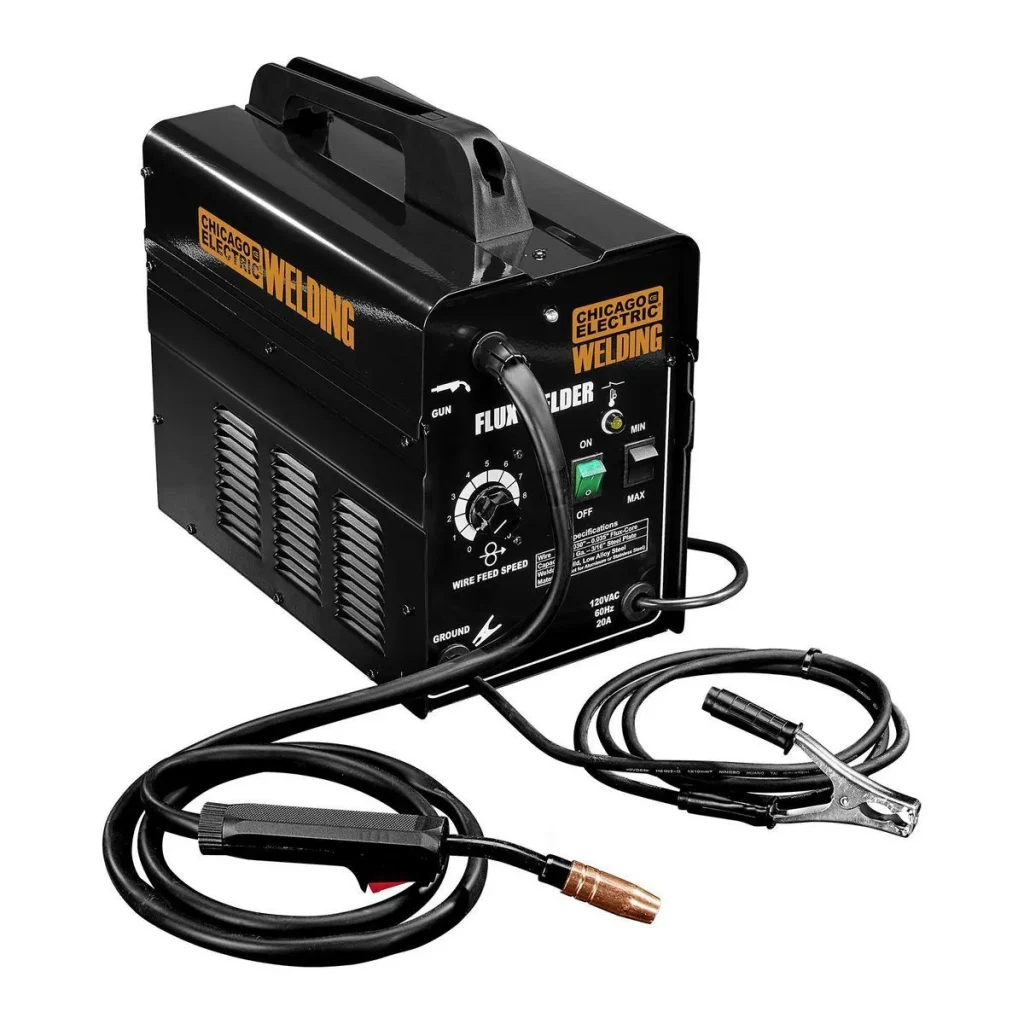
Preparing the 125 Flux Core Welder for Use
Before you can begin welding with the 125 flux core welder, it’s important to properly set up the machine and ensure that all the necessary components are in place. This process typically involves the following steps:
- Connecting the Welding and Ground Cables: Start by connecting the welding cable to the positive terminal on the welder and the ground cable to the negative terminal. Ensure that these connections are secure and free of any obstructions or damage12.
- Attaching the Welding Electrode: Next, you’ll need to attach the flux-cored welding electrode to the electrode holder. It’s crucial to select the appropriate electrode type based on the material you’ll be welding, the desired welding position, and the recommended welding current range12.
- Adjusting the Welding Current: Once the electrode is in place, you’ll need to set the welding current to a level that is suitable for the electrode diameter you’re using. As a general guideline, 1.6-2.6mm electrodes are typically used with welding currents ranging from 20 to 120 amps12.
By carefully following these preparation steps, you can ensure that your 125 flux core welder is ready to deliver optimal performance and produce high-quality welds.
Mastering the Welding Technique with the 125 Flux Core Welder
With the 125 flux core welder properly set up, it’s time to focus on developing the necessary welding technique to create strong, consistent welds. Here are some key points to keep in mind:
- Electrode Angle and Distance: Hold the welding electrode at a 60-80 degree angle relative to the workpiece, maintaining a distance of approximately 2-3mm from the weld edge. This angle and distance help to establish a stable arc and ensure proper penetration.
- Welding Speed and Direction: Move the electrode along the joint line at a steady, controlled speed. Maintain a consistent travel speed to prevent undercutting or excessive buildup of weld metal.
- Arc Length and Stability: Adjust the distance between the electrode and the workpiece to maintain a stable arc. A consistent arc length helps to ensure even heat distribution and prevents the formation of porosity or inclusions in the weld.
- Welding Current Considerations: When welding with a flux core electrode, it’s generally recommended to use a slightly higher welding current compared to stick welding. This higher current helps to ensure complete melting of the flux core, which is essential for creating a strong, slag-free weld2.
By mastering these welding techniques and continuously practicing on scrap material, you’ll be able to produce high-quality welds with the 125 flux core welder, regardless of the welding position or material thickness.
Safety Precautions and Best Practices
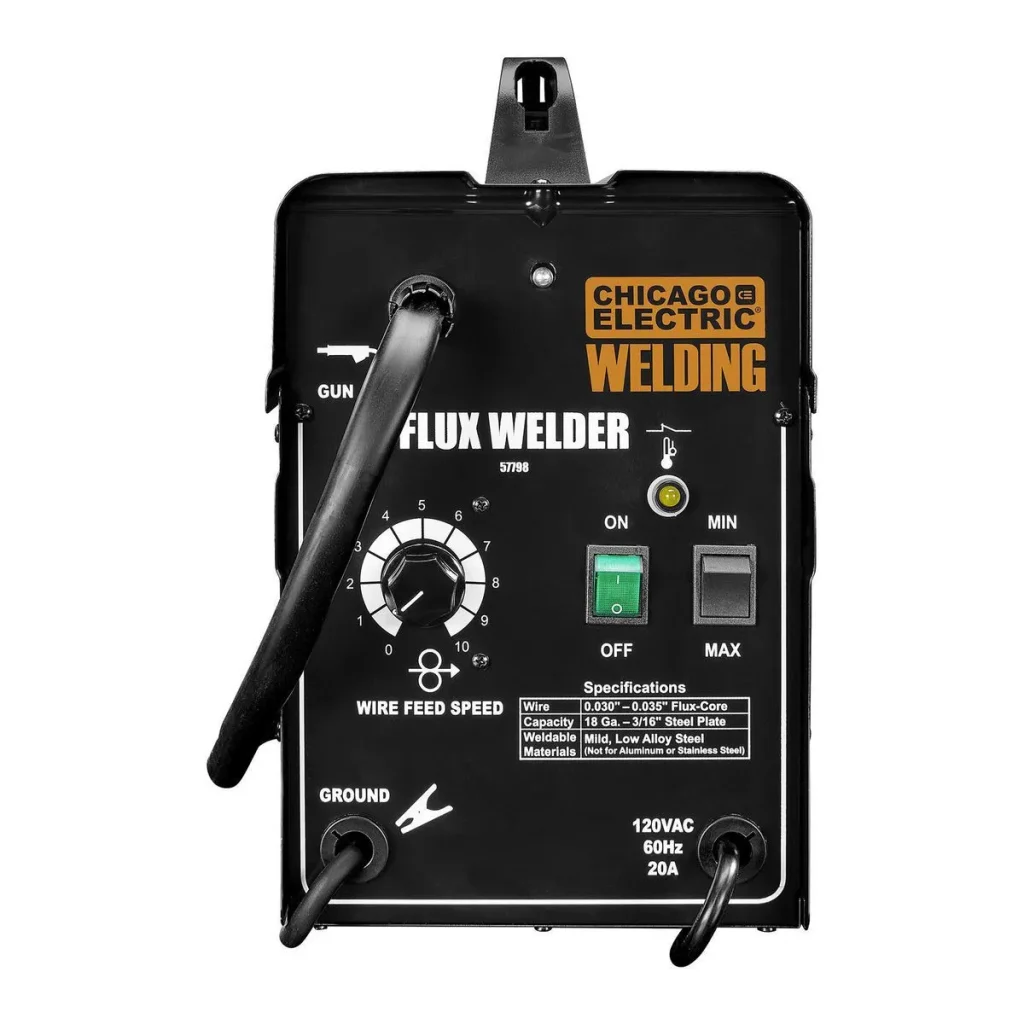
Safety should always be the top priority when operating any welding equipment, including the 125 flux core welder. To ensure a safe welding environment, it’s crucial to follow these best practices:
- Proper Personal Protective Equipment (PPE): Always wear appropriate PPE, such as a welding helmet with the correct shade lens, welding gloves, and a flame-resistant jacket or coveralls. This protective gear helps to shield you from sparks, UV radiation, and hot metal.
- Workpiece Preparation: Before welding, thoroughly clean the workpiece surface to remove any contaminants, such as oil, grease, or rust. Welding on a contaminated surface can lead to the formation of harmful fumes and can compromise the integrity of the weld.
- Ventilation and Fume Control: Ensure that the welding area is well-ventilated to prevent the buildup of welding fumes. If necessary, use a fume extractor or ensure that the area has adequate natural or mechanical ventilation.
- Fire Prevention: Be aware of any potential fire hazards in the welding area and take appropriate precautions. Keep a fire extinguisher nearby and clear the area of any flammable materials before starting to weld.
By prioritizing safety and following best practices, you can minimize the risks associated with welding and ensure a safe working environment for yourself and those around you.
Maintaining and Troubleshooting the 125 Flux Core Welder
To ensure the long-term reliability and performance of your 125 flux core welder, it’s essential to perform regular maintenance and address any issues that may arise. Here are some key steps to consider:
Routine Maintenance
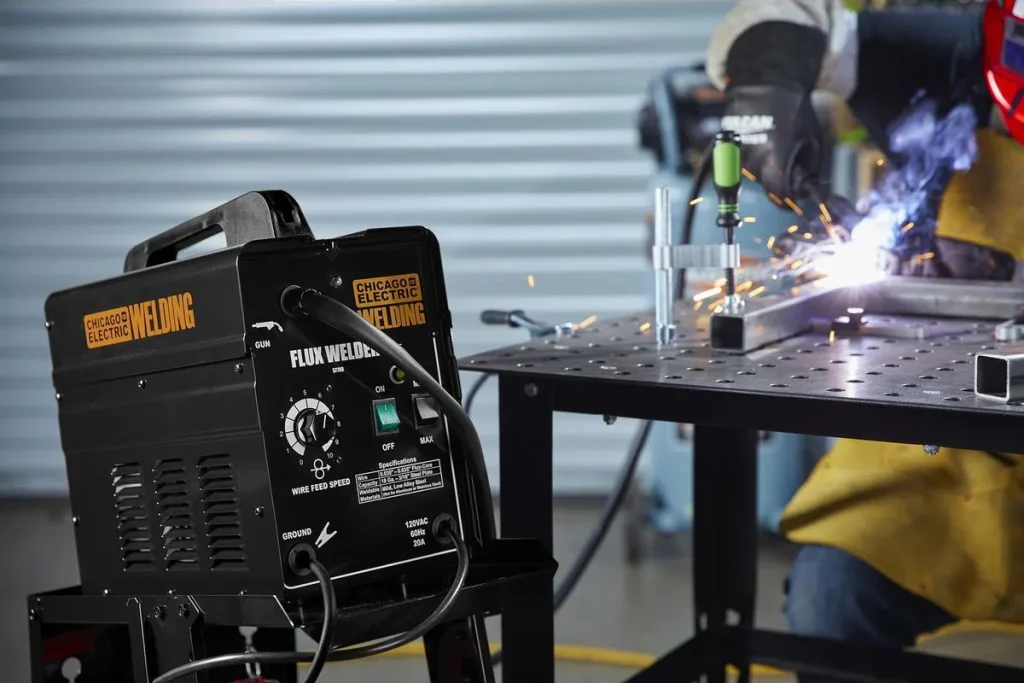
- Inspect and Clean Components: Regularly check and clean the contact tip, wire feed rolls, and other critical components to prevent buildup of dirt, dust, or debris, which can interfere with the welder’s operation.
- Replace Worn Parts: Carefully inspect the welding cables, ground clamps, and other consumable parts for signs of wear or damage. Replace these items as needed to maintain the welder’s optimal performance.
- Lubricate Moving Parts: Apply a small amount of lubricant to the moving parts of the welder, such as the wire feed mechanism, to ensure smooth operation and reduce wear.
Troubleshooting Common Issues
- Erratic Arc or Unstable Welding: If you experience an unstable arc or inconsistent welding performance, check the welding cable connections, the condition of the contact tip, and the wire feed mechanism for any issues.
- Excessive Spatter or Porosity: Excessive spatter or the presence of porosity in the weld may indicate problems with the welding parameters, such as incorrect wire feed speed, welding current, or shielding gas flow (if applicable).
- Welding Machine Failure: If the welder fails to start or experiences other electrical issues, inspect the power cable, circuit breakers, and internal components for any damage or malfunctions.
By following a regular maintenance routine and addressing any issues promptly, you can ensure that your 125 flux core welder continues to operate at peak efficiency and provide reliable, high-quality welding performance for years to come.
Conclusion
The 125 flux core welder is a versatile and cost-effective welding solution that offers numerous advantages for a wide range of steel welding applications. From its ability to weld in any position without the need for shielding gas to its relatively low initial investment, this machine is an excellent choice for small workshops, DIY enthusiasts, and professionals alike.By mastering the proper setup, welding techniques, and maintenance procedures, you can leverage the full potential of the 125 flux core welder to tackle a variety of welding projects with confidence and efficiency. Remember to always prioritize safety, follow best practices, and continuously refine your welding skills to ensure the highest quality and most reliable results.With the comprehensive knowledge and guidance provided in this article, you are now well-equipped to unleash the power of the 125 flux core welder and take your welding capabilities to new heights.
Leave a Reply