Metal welding helmets are more than just protective gear; they are a fundamental component of welding safety protocol. These helmets safeguard the welder’s eyes, face, and head from the hazardous elements produced during welding processes, such as intense light, ultraviolet (UV) and infrared (IR) radiation, sparks, metal spatter, and debris. The importance of a metal welding helmet cannot be overstated, as it directly impacts the welder’s health and safety, preventing short-term injuries and long-term health conditions.
Understanding the Metal Welding Helmet
Overview of the Key Components
- Face Shield and Protective Lens: The face shield provides a barrier against physical hazards while the protective lens filters out harmful light emissions. Advanced helmets feature lenses that can automatically adjust their tint to protect the welder’s eyes from the bright flare of the welding arc without compromising visibility.
- Headgear and Fit: The design of the headgear is crucial for both safety and comfort. It must be adjustable to fit various head sizes and shapes securely, ensuring that the helmet remains in place even during vigorous movements.
- Material and Durability: High-quality welding helmets are constructed from materials that can resist the extreme conditions of welding, such as high temperatures, impact from debris, and exposure to UV and IR radiation. Materials like thermoplastic or carbon fiber are popular for their strength and lightweight properties.
Advantages of Using a Metal Welding Helmet
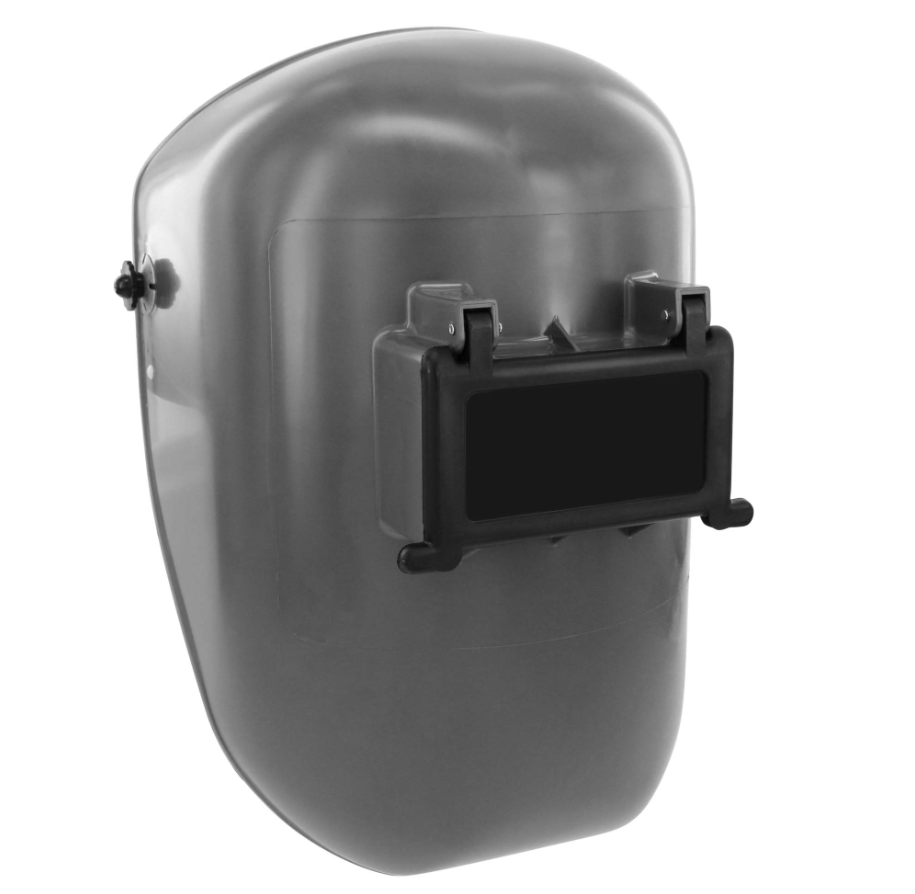
- Eye Protection: Welding helmets protect against eye damage from the intense light of the welding arc, which can cause arc eye (photokeratitis) or contribute to the development of cataracts over time.
- Face and Head Protection: In addition to protecting the eyes, helmets shield the skin and hair from hot metal, sparks, and spatter that can cause burns and other injuries.
- UV and Infrared Ray Shielding: Specialized lens coatings and filters in the helmet’s lens block harmful UV and IR radiation, preventing skin burns and eye damage.
Features to Look for in a Quality Metal Welding Helmet
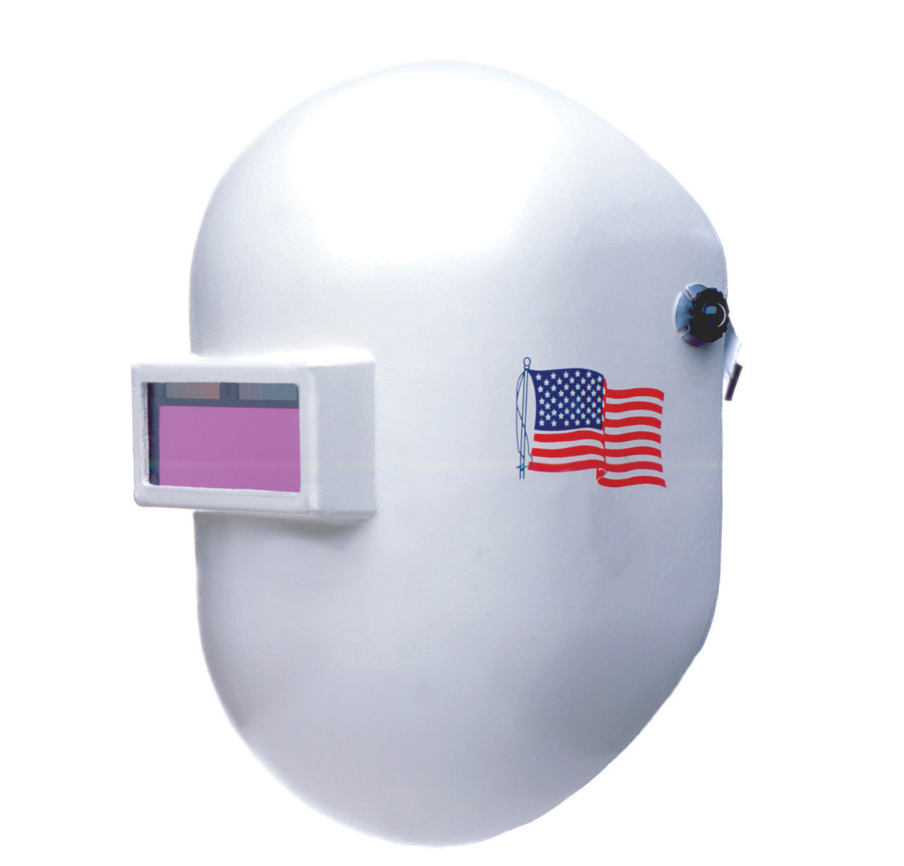
Auto-Darkening Technology
This feature allows the lens to automatically adjust its darkness level in response to the welding arc’s brightness, offering continuous protection without sacrificing visibility. The technology ensures that welders can work efficiently without needing to manually raise and lower the helmet.
Adjustable Shade Levels
Different welding tasks may require different levels of protection. A helmet with adjustable shade levels allows the welder to set the darkness of the lens according to the specific requirements of the welding process being used.
Comfort and Ergonomics
A helmet that is uncomfortable or poorly balanced can distract the welder and even lead to neck strain over long periods. Features like adjustable headbands, padded interiors, and balanced weight distribution are important for comfort and prolonged use.
Consideration of Helmet Weight and Ventilation
A lighter helmet reduces the risk of neck fatigue, while adequate ventilation helps to keep the welder cool and comfortable, reducing the risk of heat stress and ensuring clear visibility by minimizing lens fogging.
Tips on Effectively Using a Metal Welding Helmet
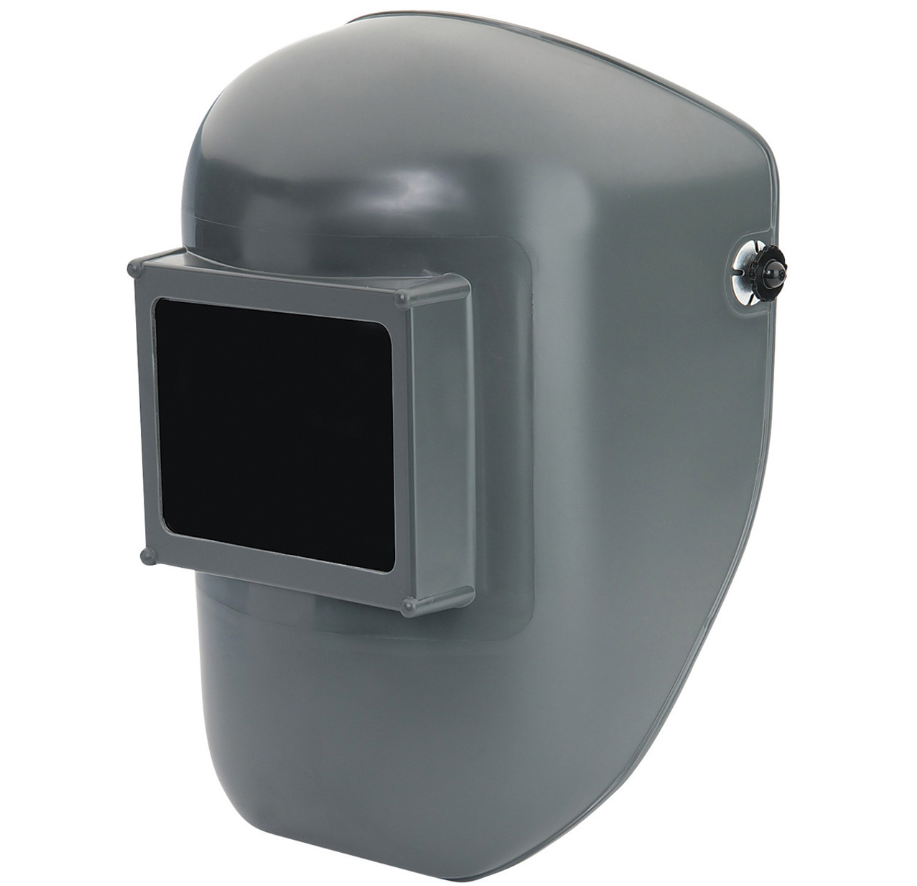
Proper Helmet Adjustment for a Secure Fit
A helmet should be adjusted to fit snugly to prevent it from slipping or shifting, which could expose the welder to hazards or distract them from their work.
Ensuring the Right Shade Level for Different Welding Tasks
It’s important to select the appropriate shade level for the task at hand to ensure optimal visibility and protection. The helmet’s manual usually includes a guide for selecting shade levels based on welding processes and amperage.
Maintenance and Cleaning Practices
Regular maintenance, including cleaning the lens to remove dust and spatter and checking for damage, ensures the helmet provides effective protection and functions correctly.
Importance of Regular Inspections and Replacements
Regularly inspect the helmet for signs of wear, such as cracks in the shield or deterioration of the headgear, and replace any damaged parts promptly to maintain protection.
Proper Storage to Prolong the Helmet’s Lifespan
When not in use, the helmet should be stored in a safe, dry place away from direct sunlight and extreme temperatures to prevent damage to the lens and the helmet’s materials.
Real-Life Applications and User Experiences
Showcasing Scenarios Where a Metal Welding Helmet is Indispensable
From industrial welding applications, where heavy-duty protection is a must, to artistic metalworking that requires precision and flexibility, a quality welding helmet is key to safety and success.
User Testimonials and Success Stories with Using Metal Welding Helmets
Stories from professional welders and hobbyists highlight how the right helmet has made a significant difference in their work, from enhancing safety to improving welding quality and comfort during long projects.
Conclusion
The conclusion from the analysis of metal welding helmets emphasizes their importance in ensuring safety and improving work efficiency. By exploring the main components, benefits, and essential features, it highlights the significance of protecting the eyes and face, the advancement of technologies like auto-darkening, and the focus on comfort and proper maintenance. Real-life testimonials further illuminate their indispensable value in various welding situations. This discussion guides the selection and use of these essential protective tools effectively, ensuring safety and efficiency in welding activities.
Leave a Reply