Introduction
The automotive industry has seen tremendous advancements over the past few decades, with technology playing a pivotal role in enhancing vehicle performance, safety, and manufacturing efficiency. Among these advancements, auto weld chassis technology stands out as a critical innovation. Automated welding systems, designed to construct the chassis of a vehicle, have revolutionized the way vehicles are built. This article explores the significance of auto weld chassis technology, shedding light on its benefits, challenges, and future trends.
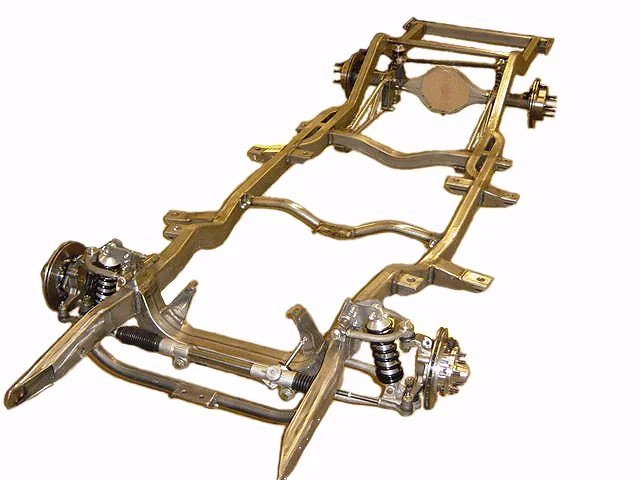
What is Automated Welding?
Automated welding, also known as robotic welding, refers to the use of programmable tools and machines to perform welding operations. This technology leverages robotics and computer control to carry out precise and consistent welding tasks, eliminating the variability associated with manual welding.
What is a Chassis?
The chassis is the foundational frame of a vehicle, providing structural support and housing various components such as the engine, transmission, and suspension system. It plays a crucial role in ensuring the vehicle’s stability, safety, and overall performance.
The integration of automated welding technology in chassis manufacturing has brought about numerous advantages, from improved weld quality to increased production efficiency. In the following sections, we will delve deeper into the history, benefits, challenges, and future prospects of auto weld chassis technology.
The Evolution of Chassis Welding Techniques
History
The journey of chassis welding techniques has been marked by significant milestones, evolving from traditional manual methods to advanced automated systems. Initially, chassis welding was performed manually by skilled welders who relied on their expertise and experience to create strong, durable welds. However, manual welding posed several challenges, including inconsistencies in weld quality, slower production times, and higher labor costs.
As the automotive industry grew and the demand for vehicles increased, there was a pressing need to improve the efficiency and precision of chassis welding. This led to the development of semi-automated welding systems, where welders used machines to assist with the welding process. These systems improved productivity but still required considerable human intervention.
Significant Milestones
The introduction of fully automated welding robots in the late 20th century marked a turning point in chassis manufacturing. These robots, equipped with sophisticated sensors and control systems, could perform welding tasks with high precision and repeatability. Key milestones in the evolution of chassis welding include:
- Introduction of Welding Robots (1980s):
The adoption of industrial robots for welding tasks revolutionized the automotive manufacturing process. These robots were capable of performing consistent and precise welds, significantly reducing human error and variability. - Advancements in Welding Technology (1990s):
The development of advanced welding techniques such as laser welding and friction stir welding further enhanced the quality and strength of chassis welds. These methods offered improved penetration and reduced heat distortion, making them ideal for chassis construction. - Integration of Computer Control (2000s):
The integration of computer control systems with welding robots allowed for greater customization and flexibility in the welding process. Programmable logic controllers (PLCs) and computer-aided design (CAD) software enabled precise control over welding parameters, ensuring optimal weld quality. - Adoption of Collaborative Robots (2010s):
Collaborative robots, or cobots, emerged as a game-changer in chassis welding. These robots could work alongside human operators, combining the strengths of both human dexterity and robotic precision. Cobots enhanced productivity while maintaining safety and flexibility on the production floor.
Impact on the Automotive Industry
The evolution of chassis welding techniques has had a profound impact on the automotive industry. Automated welding systems have enabled manufacturers to produce high-quality chassis at a faster rate and lower cost. The consistency and precision of automated welds have improved vehicle safety and performance, meeting stringent industry standards.
Moreover, the use of advanced welding technologies has allowed for the creation of lighter and more durable chassis, contributing to improved fuel efficiency and reduced emissions. As the industry continues to evolve, further advancements in welding technology are expected to drive innovation and enhance the competitiveness of automotive manufacturers.
Benefits of Automated Welding in Chassis Manufacturing
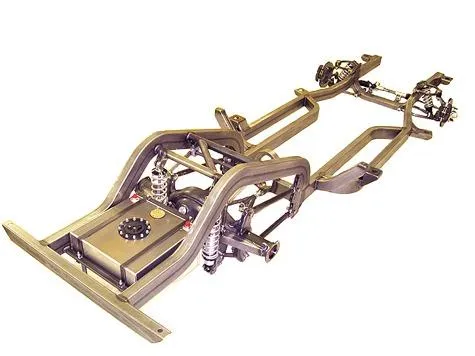
Improved Weld Quality
One of the most significant benefits of automated welding in chassis manufacturing is the remarkable improvement in weld quality. Automated systems are designed to execute precise and consistent welds, which are critical for the structural integrity of a vehicle chassis. The key factors contributing to improved weld quality include:
- Consistency: Automated welding robots can perform the same weld repeatedly with identical parameters, ensuring uniform quality across all chassis components. This consistency is difficult to achieve with manual welding, where human factors can introduce variability.
- Precision: Advanced sensors and control systems allow welding robots to execute welds with high precision, reducing the likelihood of defects such as porosity, incomplete fusion, and weld spatter. Precise welds enhance the strength and durability of the chassis.
- Advanced Techniques: Automated systems can utilize advanced welding techniques such as laser welding, which offers deep penetration and minimal heat distortion. These techniques are particularly beneficial for complex chassis designs and high-strength materials.
Increased Production Efficiency
Automated welding significantly boosts production efficiency, enabling manufacturers to meet the growing demand for vehicles. The main aspects of increased production efficiency include:
- Speed: Welding robots can operate at higher speeds than human welders, significantly reducing the time required to complete each weld. This increased speed translates to higher throughput and shorter production cycles.
- 24/7 Operation: Automated welding systems can operate continuously without the need for breaks, maximizing production uptime. This capability is particularly advantageous for high-volume manufacturing environments.
- Reduced Labor Costs: By automating the welding process, manufacturers can reduce reliance on manual labor, leading to cost savings in terms of wages, training, and labor-related overheads. The workforce can be reallocated to other critical areas such as quality control and system maintenance.
Enhanced Safety
Safety is a paramount concern in manufacturing environments, and automated welding systems contribute to a safer workplace in several ways:
- Reduced Exposure to Hazards: Welding involves exposure to high temperatures, intense light, and harmful fumes. Automated systems minimize human exposure to these hazards, reducing the risk of burns, eye injuries, and respiratory issues.
- Ergonomic Benefits: Manual welding can be physically demanding, leading to musculoskeletal disorders over time. Automation alleviates these physical demands, promoting better ergonomic conditions for workers.
- Predictable and Controlled Environment: Automated systems operate within controlled parameters, reducing the likelihood of accidents caused by human error. This predictability enhances overall workplace safety.
Cost Savings
The integration of automated welding systems in chassis manufacturing can lead to significant cost savings in various areas:
- Material Efficiency: Automated systems optimize the use of welding materials, reducing waste and improving overall material efficiency.
- Quality Control: Consistent and precise welds reduce the need for rework and repairs, saving costs associated with quality control and defect rectification.
- Energy Efficiency: Advanced welding techniques such as laser welding consume less energy compared to traditional methods, contributing to lower energy costs and a smaller environmental footprint.
The combination of improved weld quality, increased production efficiency, enhanced safety, and cost savings makes automated welding an indispensable technology in modern chassis manufacturing. In the next section, we will explore how automated welding enhances the durability and safety of vehicle chassis.
How Automated Welding Enhances Chassis Durability and Safety
Structural Integrity
Automated welding plays a crucial role in enhancing the structural integrity of vehicle chassis. The precision and consistency of automated welds ensure that each joint is uniformly strong and free from defects. This uniformity is essential for maintaining the overall strength and stability of the chassis, which is the backbone of any vehicle. Key aspects include:
- Consistent Weld Penetration: Automated systems can maintain consistent weld penetration, ensuring that each weld joint is fully fused and structurally sound. This consistency is particularly important in critical load-bearing areas of the chassis.
- Reduced Weld Defects: The advanced sensors and control mechanisms in automated welding systems help detect and correct any deviations during the welding process, minimizing common weld defects such as cracks, voids, and inclusions.
Enhanced Safety
The safety of a vehicle heavily depends on the integrity of its chassis. Automated welding systems contribute to vehicle safety in several ways:
- Crashworthiness: A well-welded chassis can better absorb and dissipate energy during a collision, protecting the occupants of the vehicle. Automated welding ensures that all weld joints are robust and capable of withstanding impact forces.
- Fatigue Resistance: Vehicles are subjected to continuous vibrations and stresses during operation. Automated welding enhances the fatigue resistance of the chassis by producing high-quality welds that are less prone to failure under cyclic loading conditions.
- Corrosion Resistance: Consistent and precise welds reduce the likelihood of gaps and inconsistencies where moisture and contaminants can accumulate, thus improving the corrosion resistance of the chassis. Some automated welding processes also include post-weld treatments that further enhance corrosion protection.
Use of Advanced Materials
Automated welding systems can handle advanced materials that offer superior strength and durability compared to traditional materials. These materials, such as high-strength steel and aluminum alloys, require precise control during welding to maintain their properties. Benefits include:
- High-Strength Steel: Automated welding techniques like laser welding are particularly effective for high-strength steel, providing deep penetration and minimal thermal distortion. This results in strong, lightweight chassis structures.
- Aluminum Alloys: Aluminum alloys are favored for their light weight and excellent corrosion resistance. Automated welding systems can perform techniques such as friction stir welding, which is ideal for joining aluminum without compromising its mechanical properties.
Integration with Quality Control Systems
Automated welding systems can be integrated with advanced quality control systems that continuously monitor the welding process. This integration ensures that any deviations from the desired welding parameters are immediately detected and corrected. Features include:
- Real-Time Monitoring: Sensors and cameras monitor the weld pool, arc characteristics, and joint alignment in real time, providing immediate feedback and adjustments to maintain weld quality.
- Data Logging and Analysis: Automated systems can log welding data for each joint, enabling detailed analysis and traceability. This data can be used to optimize the welding process and identify areas for improvement.
The combined effect of these enhancements is a chassis that is not only durable and safe but also optimized for performance and longevity. The next section will delve into the challenges faced in auto weld chassis production and the solutions to overcome them.
Challenges and Solutions in Auto Weld Chassis Production
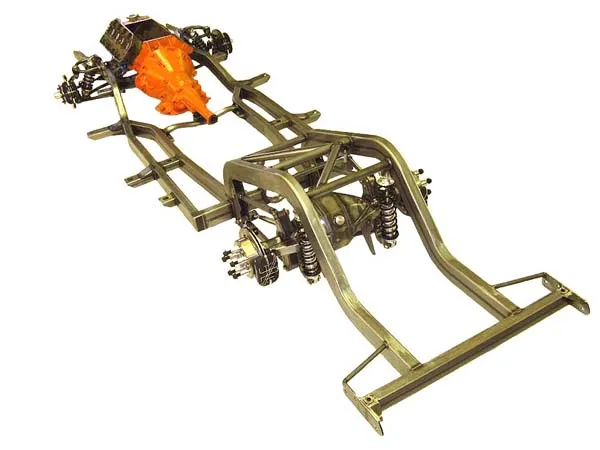
Common Challenges
Despite the numerous benefits, integrating automated welding systems into chassis production is not without its challenges. These challenges must be addressed to ensure high-quality welds and efficient production processes. The most common challenges include:
- Material Compatibility:
- Challenge: Different materials used in chassis construction, such as high-strength steel and aluminum, require specific welding techniques and parameters. Incompatibility can lead to poor weld quality and structural weaknesses.
- Solution: Advanced welding systems are equipped with multi-material welding capabilities and can be programmed to adjust welding parameters automatically based on the material being welded. Additionally, hybrid welding techniques that combine different welding processes can be employed to handle diverse materials.
- Joint Accessibility:
- Challenge: Some areas of the chassis are difficult to access, making it challenging for welding robots to perform accurate welds.
- Solution: Flexible robotic arms and end-effectors with multiple degrees of freedom can reach complex joints. The use of collaborative robots (cobots) that work alongside human operators can also help access hard-to-reach areas while maintaining precision.
- Heat Management:
- Challenge: Excessive heat input during welding can cause distortion, warping, and weakening of the chassis material. Managing heat effectively is crucial to maintaining weld quality.
- Solution: Advanced welding techniques such as laser welding and friction stir welding generate less heat and offer better control over heat input. Additionally, real-time temperature monitoring and adaptive cooling systems can help manage heat during the welding process.
- Alignment and Fixturing:
- Challenge: Proper alignment of components and secure fixturing are essential for accurate and consistent welds. Misalignment can lead to defective welds and compromised structural integrity.
- Solution: Precision fixturing systems and automated alignment tools can ensure that components are correctly positioned before welding. Vision systems and sensors can provide real-time feedback and adjustments to maintain alignment.
- Quality Control:
- Challenge: Ensuring consistent weld quality across all chassis components is challenging, especially in high-volume production.
- Solution: Integration of real-time quality monitoring systems with automated welding robots can detect and correct defects during the welding process. Non-destructive testing (NDT) methods such as ultrasonic testing and X-ray inspection can be used to verify weld quality without damaging the components.
Best Practices and Solutions
Implementing best practices and solutions can help overcome the challenges in auto weld chassis production, ensuring high-quality welds and efficient manufacturing processes. Key strategies include:
- Training and Skill Development:
- Ensuring that operators and technicians are well-trained in using automated welding systems and understanding welding parameters for different materials is crucial. Regular training programs and certifications can enhance their skills and knowledge.
- Continuous Process Improvement:
- Implementing a continuous improvement approach, such as Lean Manufacturing and Six Sigma methodologies, can help identify and eliminate inefficiencies in the welding process. Regular audits and process reviews can lead to incremental improvements in weld quality and production efficiency.
- Collaboration with Equipment Manufacturers:
- Working closely with welding equipment manufacturers can provide access to the latest technologies and best practices. Collaborative development of customized welding solutions can address specific challenges faced in chassis production.
- Adoption of Advanced Technologies:
- Leveraging advanced technologies such as artificial intelligence (AI) and machine learning (ML) can optimize welding parameters and predict potential defects. AI-driven systems can analyze welding data and suggest improvements to enhance weld quality and efficiency.
By addressing these challenges and implementing effective solutions, manufacturers can maximize the benefits of automated welding systems in chassis production, leading to improved product quality, higher productivity, and reduced costs.
The next section will explore future trends in automated chassis welding, providing insights into the technologies and innovations shaping the future of this field.
Future Trends in Automated Chassis Welding
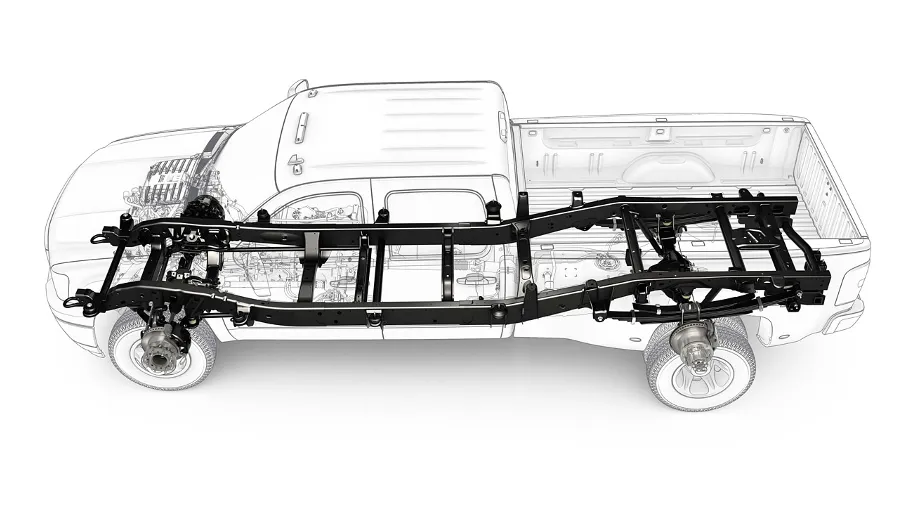
Emerging Technologies
The field of automated chassis welding is continually evolving, with new technologies and innovations enhancing the efficiency, precision, and capabilities of welding systems. Some of the most promising emerging technologies include:
- Artificial Intelligence and Machine Learning:
- Overview: AI and ML are revolutionizing automated welding by enabling predictive analytics, real-time monitoring, and adaptive control of welding parameters.
- Applications: AI algorithms can analyze vast amounts of welding data to identify patterns and optimize welding processes. Machine learning models can predict potential defects and suggest corrective actions, improving overall weld quality.
- Collaborative Robots (Cobots):
- Overview: Cobots are designed to work alongside human operators, combining the strengths of human dexterity and robotic precision.
- Applications: Cobots can assist in welding tasks that require complex maneuvers and fine adjustments, enhancing flexibility and efficiency on the production floor. Their ability to learn from human operators through intuitive programming interfaces makes them adaptable to various welding scenarios.
- Laser Welding and Hybrid Welding Techniques:
- Overview: Laser welding offers high precision and deep penetration with minimal heat input, making it ideal for advanced materials and complex geometries.
- Applications: Hybrid welding techniques, which combine laser welding with other methods such as arc welding, provide the benefits of multiple welding processes in a single operation. This approach can enhance weld strength and reduce cycle times.
- Internet of Things (IoT) and Industry 4.0:
- Overview: IoT and Industry 4.0 technologies enable the integration of welding systems with other manufacturing processes, creating a connected and intelligent production environment.
- Applications: IoT sensors can monitor welding parameters in real-time, providing valuable data for process optimization. Industry 4.0 frameworks facilitate seamless communication between welding robots, quality control systems, and production management software.
- Advanced Welding Materials:
- Overview: The development of new welding materials and consumables enhances the capabilities of automated welding systems.
- Applications: High-performance welding wires and coatings can improve weld quality and reduce the risk of defects. Research into nano-materials and advanced alloys is opening new possibilities for lightweight and high-strength chassis construction.
Impact on the Automotive Industry
The adoption of these emerging technologies is set to transform the automotive industry in several ways:
- Increased Customization and Flexibility:
- Automated welding systems equipped with AI and machine learning can quickly adapt to different welding tasks, enabling manufacturers to produce customized chassis designs with high precision. This flexibility is essential for meeting the diverse demands of modern consumers.
- Enhanced Productivity and Efficiency:
- The integration of IoT and Industry 4.0 technologies allows for real-time monitoring and optimization of welding processes, leading to higher productivity and reduced downtime. Advanced robotics and hybrid welding techniques further streamline production, reducing cycle times and increasing throughput.
- Improved Quality and Safety:
- AI-driven quality control systems and advanced welding materials ensure that each weld meets stringent safety and performance standards. The use of collaborative robots enhances safety on the production floor by reducing human exposure to hazardous conditions.
- Sustainability and Environmental Impact:
- Advanced welding techniques such as laser welding and hybrid methods consume less energy and generate fewer emissions compared to traditional welding processes. The use of lightweight materials and efficient production methods contributes to the overall sustainability of the automotive industry.
Future Outlook
The future of automated chassis welding is bright, with continuous advancements driving innovation and efficiency. Key trends to watch include:
- Integration of Autonomous Systems:
- Fully autonomous welding systems that can operate independently with minimal human intervention are on the horizon. These systems will leverage AI, IoT, and advanced robotics to create self-optimizing production lines.
- Development of Smart Welding Solutions:
- Smart welding solutions that combine real-time data analytics, predictive maintenance, and adaptive control will enhance the reliability and performance of welding systems. These solutions will enable manufacturers to anticipate and address issues before they impact production.
- Expansion of Collaborative Technologies:
- The continued development of collaborative robots and human-robot interaction technologies will enhance the capabilities of welding systems, making them more versatile and user-friendly. This expansion will open new possibilities for complex and high-precision welding tasks.
The next section will present case studies of companies that have successfully implemented automated welding systems in their chassis production lines, highlighting the benefits they have achieved.
Case Studies: Successful Implementation of Auto Weld Chassis Systems
Case Study 1: Tesla, Inc.
Overview: Tesla, Inc. is renowned for its innovative approach to electric vehicle manufacturing. The company has heavily invested in automated welding systems to enhance the production of its vehicle chassis.
- Implementation: Tesla’s Gigafactory features state-of-the-art welding robots that perform high-precision welds on the chassis of the Model S, Model 3, Model X, and Model Y. The factory employs laser welding and friction stir welding techniques to ensure robust and lightweight chassis construction.
- Benefits:
- Increased Production Speed: Automated welding systems have significantly reduced the time required to assemble each chassis, enabling Tesla to scale production to meet high demand.
- Improved Weld Quality: The precision and consistency of automated welds have enhanced the structural integrity and safety of Tesla vehicles.
- Cost Savings: By reducing labor costs and minimizing material waste, Tesla has achieved substantial cost savings, contributing to its competitive pricing strategy.
Case Study 2: BMW Group
Overview: BMW Group has integrated advanced automated welding technologies across its production facilities to manufacture high-performance and luxury vehicles.
- Implementation: BMW’s production plant in Dingolfing, Germany, utilizes collaborative robots (cobots) and AI-driven welding systems for chassis assembly. These systems are capable of performing complex welds with high precision and minimal human intervention.
- Benefits:
- Enhanced Flexibility: The use of cobots allows BMW to quickly adapt to different vehicle models and customization requests, providing greater flexibility in production.
- Superior Quality Control: AI-driven quality control systems ensure that each weld meets BMW’s stringent standards, reducing the incidence of defects and rework.
- Safety Improvements: By automating hazardous welding tasks, BMW has improved workplace safety and reduced the risk of injuries among its workforce.
Case Study 3: Ford Motor Company
Overview: Ford Motor Company has a long history of innovation in automotive manufacturing. The company’s investment in automated welding technology has revolutionized its chassis production processes.
- Implementation: Ford’s Dearborn Truck Plant in Michigan employs a combination of robotic welding systems and advanced materials to construct the chassis of its F-150 trucks. The plant uses hybrid welding techniques to achieve strong and durable welds.
- Benefits:
- High-Strength Chassis: The use of advanced welding techniques and high-strength materials has resulted in chassis that are both lightweight and exceptionally durable, enhancing vehicle performance and fuel efficiency.
- Production Efficiency: Automated welding systems have increased the speed and efficiency of the chassis assembly line, allowing Ford to meet high production targets while maintaining quality.
- Sustainability: By optimizing energy use and reducing material waste, Ford’s automated welding systems contribute to the company’s sustainability goals.
Case Study 4: Toyota Motor Corporation
Overview: Toyota is a global leader in automotive manufacturing, known for its commitment to quality and efficiency. The company’s adoption of automated welding systems has been instrumental in maintaining its competitive edge.
- Implementation: Toyota’s Tsutsumi plant in Japan features cutting-edge welding robots and IoT-enabled systems that monitor and optimize the welding process in real time. The plant uses laser welding and spot welding techniques to assemble chassis components.
- Benefits:
- Consistent Quality: The integration of IoT and real-time monitoring ensures consistent weld quality, minimizing the risk of defects and enhancing vehicle safety.
- Lean Manufacturing: Automated welding systems support Toyota’s lean manufacturing principles by reducing waste and improving process efficiency.
- Cost Efficiency: The use of automated systems has led to significant cost savings in terms of labor and material costs, contributing to Toyota’s overall profitability.
These case studies demonstrate the transformative impact of automated welding systems on chassis production. The successful implementation of these technologies has enabled leading automotive manufacturers to achieve higher quality, efficiency, and cost-effectiveness in their operations.
The next section will provide a guide on selecting the right automated welding system for different types of chassis production needs.
Choosing the Right Automated Welding System for Chassis Manufacturing
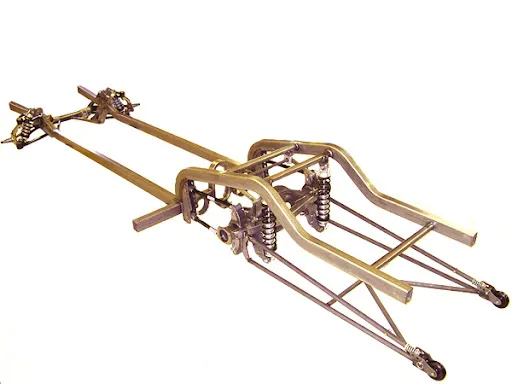
Factors to Consider
Selecting the appropriate automated welding system for chassis manufacturing involves evaluating several critical factors to ensure optimal performance and compatibility with production requirements. Key considerations include:
- Material Compatibility:
- Consideration: The welding system must be compatible with the materials used in chassis construction, such as high-strength steel, aluminum alloys, and composites.
- Solution: Choose welding systems that offer flexibility in handling various materials and can be easily programmed to adjust welding parameters for different materials.
- Welding Techniques:
- Consideration: Different welding techniques are suited for specific applications and materials. Common techniques include laser welding, friction stir welding, and resistance spot welding.
- Solution: Evaluate the advantages and limitations of each welding technique to determine the most suitable method for your chassis production needs. Hybrid systems that combine multiple techniques can offer added flexibility and performance.
- Production Volume:
- Consideration: The system should be capable of meeting the production volume requirements, whether for high-volume mass production or low-volume custom manufacturing.
- Solution: For high-volume production, fully automated systems with high-speed capabilities are ideal. For lower volumes, flexible systems that can be quickly reconfigured for different tasks are preferable.
- System Scalability:
- Consideration: The chosen system should be scalable to accommodate future production increases or changes in product design.
- Solution: Opt for modular welding systems that can be expanded or upgraded as needed, allowing for easy integration of additional robots or advanced technologies.
- Integration with Existing Systems:
- Consideration: The new welding system should integrate seamlessly with existing production lines and quality control systems.
- Solution: Ensure compatibility with current manufacturing infrastructure and consider systems that support Industry 4.0 standards for connected and intelligent manufacturing.
- Cost and ROI:
- Consideration: The initial investment and ongoing operational costs should be weighed against the expected return on investment (ROI).
- Solution: Conduct a thorough cost-benefit analysis, considering factors such as reduced labor costs, increased production efficiency, and improved product quality. Look for systems with a proven track record of delivering positive ROI.
Steps to Select the Right System
- Needs Assessment:
- Conduct a detailed assessment of your specific welding needs, including material types, production volumes, and quality requirements.
- Identify any unique challenges or constraints in your manufacturing process that the welding system must address.
- Market Research:
- Research available welding systems and technologies, focusing on those that align with your needs assessment.
- Engage with welding equipment manufacturers and suppliers to gather information on the latest innovations and capabilities.
- Vendor Evaluation:
- Evaluate potential vendors based on their expertise, reputation, and ability to provide comprehensive support, including installation, training, and maintenance.
- Request demonstrations or pilot projects to assess the performance and suitability of their systems in your production environment.
- Technical Specifications:
- Review the technical specifications of shortlisted systems, ensuring they meet your requirements for material compatibility, welding techniques, and scalability.
- Consider the ease of programming and customization to accommodate different chassis designs and production scenarios.
- Implementation Plan:
- Develop a detailed implementation plan, including timelines, resource allocation, and risk management strategies.
- Ensure that all stakeholders, including production staff and maintenance teams, are involved in the planning process to ensure smooth integration.
- Training and Support:
- Invest in comprehensive training programs for operators and technicians to maximize the effectiveness of the new welding system.
- Establish a support and maintenance agreement with the vendor to ensure ongoing reliability and performance.
Example Scenario
Scenario: A mid-sized automotive manufacturer looking to upgrade its chassis production line with an automated welding system.
- Needs Assessment: The manufacturer uses high-strength steel and aluminum alloys in its chassis designs and requires a system that can handle both materials. The production volume is moderate, with the potential for future expansion.
- Market Research: The company identifies several vendors offering laser welding and friction stir welding systems, both of which are suitable for their materials.
- Vendor Evaluation: After evaluating three vendors, the manufacturer selects a system that provides flexibility in handling different materials and offers excellent scalability for future growth.
- Technical Specifications: The chosen system includes modular robotic arms, advanced sensors, and AI-driven quality control, ensuring precise and consistent welds.
- Implementation Plan: The implementation plan includes a phased rollout, starting with a pilot project on one production line, followed by full-scale deployment.
- Training and Support: Operators and technicians undergo extensive training, and the vendor provides ongoing support to ensure the system operates at peak performance.
By carefully considering these factors and following a structured selection process, manufacturers can choose the right automated welding system to enhance their chassis production capabilities.
The next section will discuss the environmental impact of automated welding in chassis manufacturing and highlight eco-friendly practices and technologies.
Environmental Impact of Automated Welding in Chassis Manufacturing
Environmental Benefits
Automated welding systems offer several environmental benefits, contributing to more sustainable manufacturing practices. These benefits include:
- Reduced Energy Consumption:
- Efficiency: Advanced welding techniques such as laser welding and friction stir welding are more energy-efficient compared to traditional welding methods. These techniques require less heat and power, leading to lower overall energy consumption.
- Precision: Automated systems minimize unnecessary welding operations and optimize energy use by precisely targeting weld areas, reducing waste.
- Lower Emissions:
- Fewer Pollutants: Automated welding generates fewer emissions compared to manual welding, primarily due to better control over the welding process and reduced need for corrective rework.
- Cleaner Processes: Advanced welding methods, such as laser welding, produce fewer fumes and particulates, contributing to a cleaner working environment and reducing the impact on air quality.
- Material Efficiency:
- Reduced Waste: Automated welding systems optimize material usage by ensuring precise and consistent welds, reducing scrap and rework. This efficiency not only conserves materials but also minimizes the environmental impact associated with waste disposal.
- Advanced Alloys: The ability to work with advanced, lightweight materials such as high-strength steel and aluminum alloys can lead to the production of lighter vehicles, which consume less fuel and emit fewer greenhouse gases over their lifecycle.
- Enhanced Recycling:
- Recycling-Friendly Design: Automated welding systems can be programmed to use techniques that facilitate easier disassembly and recycling of vehicle components at the end of their lifecycle.
- Material Recovery: Improved weld quality reduces the risk of material degradation, ensuring that more components can be recycled or reused, further reducing environmental impact.
Eco-Friendly Practices
In addition to the inherent environmental benefits of automated welding, manufacturers can adopt several eco-friendly practices to further enhance sustainability:
- Green Manufacturing Initiatives:
- Implementing green manufacturing initiatives, such as using renewable energy sources and reducing water usage in the production process, can significantly reduce the environmental footprint of chassis manufacturing.
- Lifecycle Analysis:
- Conducting a comprehensive lifecycle analysis of the chassis production process can help identify areas for improvement in energy consumption, emissions, and material usage. This analysis enables manufacturers to make informed decisions and implement strategies that minimize environmental impact.
- Waste Management:
- Developing robust waste management programs that prioritize recycling and reusing materials can help reduce landfill waste and conserve natural resources. Automated systems can assist by generating detailed waste reports and identifying opportunities for waste reduction.
- Sustainable Supply Chain:
- Partnering with suppliers that adhere to sustainable practices and sourcing eco-friendly materials can enhance the overall sustainability of the manufacturing process. Manufacturers can establish criteria for evaluating and selecting suppliers based on their environmental performance.
- Employee Training and Awareness:
- Training employees on sustainable practices and raising awareness about the environmental impact of manufacturing activities can foster a culture of sustainability within the organization. Engaged and informed employees are more likely to contribute to environmental initiatives and support sustainable practices.
Case Study: Eco-Friendly Practices in Automated Welding
Scenario: An automotive manufacturer aims to reduce the environmental impact of its chassis production line by implementing automated welding systems and eco-friendly practices.
- Implementation: The manufacturer installs energy-efficient laser welding systems and integrates them with a renewable energy source, such as solar panels, to power the welding operations. Additionally, the company adopts a zero-waste policy, focusing on recycling and reusing materials.
- Benefits:
- Energy Savings: The use of renewable energy and energy-efficient welding systems significantly reduces the overall energy consumption and carbon footprint of the manufacturing process.
- Waste Reduction: By optimizing material usage and recycling scrap materials, the manufacturer minimizes waste and reduces the environmental impact associated with waste disposal.
- Cleaner Production: The adoption of advanced welding techniques and waste management practices results in cleaner production processes, with fewer emissions and pollutants.
By embracing these eco-friendly practices, the manufacturer not only enhances its environmental performance but also achieves cost savings and improves its reputation as a sustainable and responsible company.
Conclusion
Summary of Key Points
In this article, we have explored the transformative impact of automated welding systems on chassis manufacturing. Key points covered include:
- Introduction: Automated welding technology is essential for modern chassis manufacturing, offering numerous benefits over traditional methods.
- Evolution: The progression from manual to fully automated welding systems has significantly improved the efficiency, precision, and quality of chassis production.
- Benefits: Automated welding enhances weld quality, increases production efficiency, improves safety, and reduces costs.
- Durability and Safety: High-quality automated welds enhance the structural integrity, crashworthiness, and overall safety of vehicle chassis.
- Challenges and Solutions: Addressing common challenges in automated welding through advanced technologies and best practices ensures optimal performance.
- Future Trends: Emerging technologies such as AI, machine learning, and collaborative robots are shaping the future of automated welding.
- Case Studies: Successful implementations of automated welding systems by leading automotive manufacturers demonstrate the tangible benefits of this technology.
- Choosing the Right System: Factors to consider when selecting an automated welding system include material compatibility, welding techniques, production volume, and scalability.
- Environmental Impact: Automated welding systems contribute to sustainability by reducing energy consumption, emissions, and material waste, while eco-friendly practices further enhance environmental performance.
Importance of Automated Welding
The integration of automated welding systems in chassis manufacturing is not just a technological advancement but a necessity for meeting the demands of modern automotive production. These systems offer unparalleled precision, efficiency, and quality, ensuring that vehicles are safe, durable, and environmentally friendly.
Future Outlook
As technology continues to advance, the future of automated welding in chassis manufacturing looks promising. The ongoing development of AI-driven systems, collaborative robots, and sustainable practices will further enhance the capabilities and environmental performance of welding systems. Manufacturers that embrace these innovations will be well-positioned to lead the industry and meet the evolving needs of consumers and regulatory bodies.
Leave a Reply