Welding is a fundamental process in manufacturing and construction that involves joining materials, typically metals, by causing coalescence. This is usually done by melting the workpieces and adding a filler material to form a strong joint upon cooling. Welding is crucial in various industries, including automotive, aerospace, construction, and shipbuilding, where durable and reliable joints are necessary.
There are numerous welding techniques, each with its unique principles, advantages, and applications. Understanding these techniques is essential for selecting the appropriate method for a specific project, ensuring quality and efficiency in the welding process.
In this article, we will delve into some of the most popular welding techniques, their characteristics, applications, and benefits. Additionally, we will explore ways to enhance welding skills, essential safety measures, and the latest technological trends in welding.
Common Welding Techniques
MIG Welding (Metal Inert Gas)
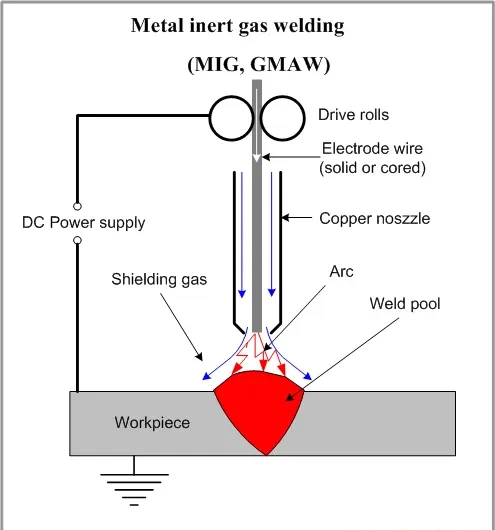
Characteristics and Working Principle
MIG welding, also known as Gas Metal Arc Welding (GMAW), is a process where a continuous solid wire electrode is fed through a welding gun into the weld pool, joining the two base materials together. An external gas, usually argon or a mixture of argon and CO2, shields the weld pool from contaminants in the atmosphere.
Applications and Benefits
MIG welding is widely used in the automotive industry, particularly in the manufacturing of car bodies and frames. It is also common in the construction of steel structures and pipelines. The benefits of MIG welding include:
- High welding speed.
- Ability to weld thin and thick materials.
- Produces clean and precise welds with minimal spatter.
TIG Welding (Tungsten Inert Gas)
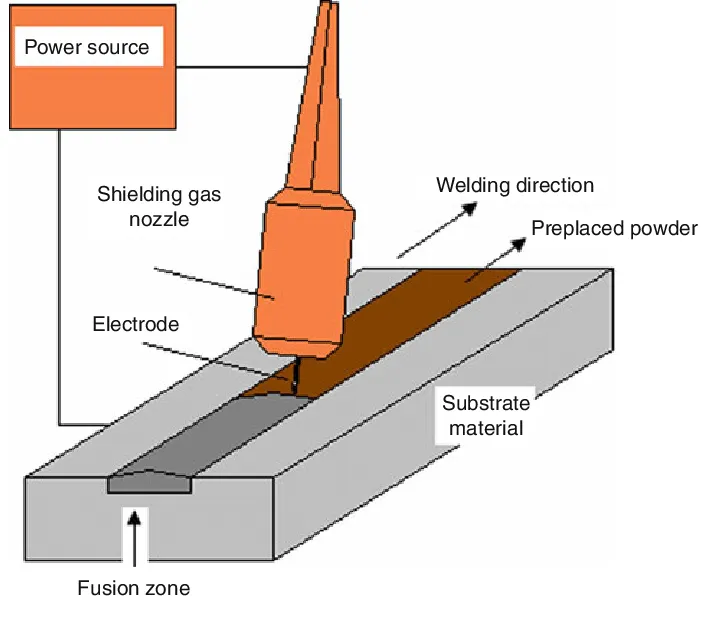
Characteristics and Working Principle
TIG welding, or Gas Tungsten Arc Welding (GTAW), uses a non-consumable tungsten electrode to produce the weld. The weld area is protected from atmospheric contamination by an inert gas, typically argon. A filler material may or may not be used, depending on the application.
Applications and Benefits
TIG welding is favored in industries requiring high precision and quality, such as aerospace and medical device manufacturing. It is also used for welding thin materials like stainless steel and non-ferrous metals. The advantages of TIG welding include:
- Produces high-quality, precise welds.
- Suitable for a wide range of metals, including aluminum and magnesium.
- Allows for excellent control over the welding process.
Stick Welding (Shielded Metal Arc Welding – SMAW)
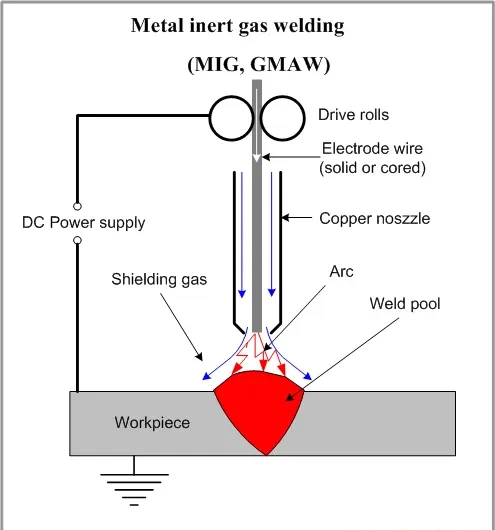
Characteristics and Working Principle
Stick welding, or Shielded Metal Arc Welding (SMAW), involves the use of a consumable electrode coated in flux. An electric current passes through the electrode, creating an arc that melts both the electrode and the base material. The flux coating disintegrates, producing a shielding gas and slag that protect the weld from oxidation and contamination.
Applications and Benefits
Stick welding is versatile and can be used in various environments, including outdoors and underwater. It is commonly used in construction, shipbuilding, and repair work. The benefits of stick welding include:
- Equipment is relatively simple and inexpensive.
- Effective on rusty or dirty surfaces.
- Suitable for welding thicker materials and heavy steel structures.
Spot Welding
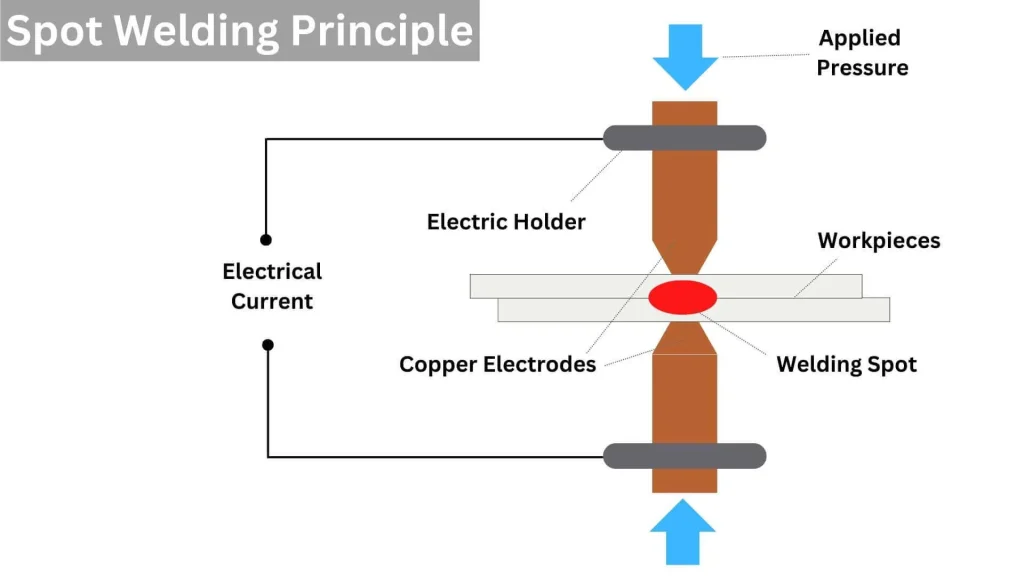
Characteristics and Working Principle
Spot welding is a resistance welding method primarily used for joining sheet metal. It involves pressing two metal sheets together and passing an electric current through the contact points to generate heat and form a weld. This technique is quick and efficient, making it ideal for mass production.
Applications and Benefits
Spot welding is extensively used in the automotive industry for assembling car bodies. It is also employed in the manufacturing of household appliances and metal furniture. The advantages of spot welding include:
- High production speed and efficiency.
- Low cost per weld.
- Minimal deformation of the workpieces.
Laser Welding
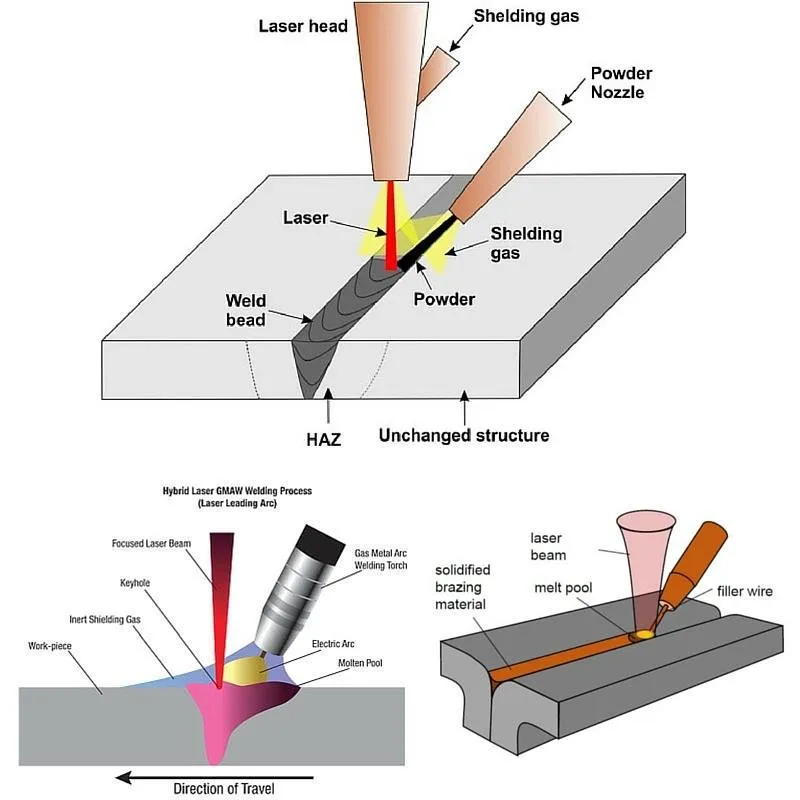
Characteristics and Working Principle
Laser welding uses a concentrated laser beam to melt and join materials. The process offers high precision and control, making it suitable for delicate and intricate work. Laser welding can be performed in different modes, including continuous and pulsed, depending on the application.
Applications and Benefits
Laser welding is widely used in industries requiring precision and cleanliness, such as electronics, medical devices, and jewelry. It is also employed in the aerospace and automotive sectors for welding small components. The benefits of laser welding include:
- High precision and minimal heat-affected zones.
- Suitable for joining small, delicate, and complex parts.
- High welding speed and automation potential.
Applications of Welding Techniques
MIG Welding Applications
- Automotive Industry: Used for assembling car bodies and frames due to its high speed and clean welds.
- Construction: Ideal for structural steel and pipeline welding, ensuring strong and reliable joints.
TIG Welding Applications
- Aerospace: Essential for high-precision welding of aircraft components, ensuring safety and durability.
- Medical Devices: Used for manufacturing surgical instruments and implants requiring precision and cleanliness.
Stick Welding Applications
- Construction: Suitable for welding heavy steel structures and repairing infrastructure like bridges and buildings.
- Shipbuilding: Effective for assembling and repairing ship hulls and other marine structures.
Spot Welding Applications
- Automotive Assembly: Widely used for attaching metal sheets in car manufacturing.
- Household Appliances: Commonly used in the production of metal frames and casings for appliances.
Laser Welding Applications
- Electronics: Crucial for joining small and intricate components in electronic devices.
- Jewelry: Used for precise and clean welding of precious metals in jewelry making.
Improving Welding Skills
Training and Certification
- Courses: Enroll in welding courses offered by technical schools or community colleges to gain foundational knowledge and hands-on experience.
- Certification: Obtain certifications from recognized institutions like the American Welding Society (AWS) to validate your skills and enhance job prospects.
Tips and Techniques
- Practice: Regular practice is essential to improve hand-eye coordination and welding precision.
- Equipment: Invest in high-quality welding equipment and maintain it properly for consistent performance.
- Mentorship: Seek guidance from experienced welders to learn advanced techniques and troubleshooting skills.
Safety Measures in Welding
Personal Protective Equipment (PPE)
- Welding Helmet: Protects the eyes and face from harmful UV and infrared radiation, as well as sparks and debris. Modern helmets come with auto-darkening filters that adjust to the light intensity.
- Gloves: Insulated gloves protect hands from burns, electric shock, and sharp objects. They should be made of durable materials like leather.
- Protective Clothing: Flame-resistant clothing, such as welding jackets and aprons, shields the body from sparks and heat. Avoid synthetic fabrics that can melt and cause burns.
- Safety Glasses and Face Shields: Wear safety glasses under the welding helmet and use face shields when grinding or cutting to protect against flying particles.
- Respiratory Protection: Use appropriate respirators or masks to protect against inhaling hazardous fumes and gases generated during welding.
Workplace Safety Measures
- Ventilation: Ensure proper ventilation in the workspace to disperse fumes and gases. Use local exhaust ventilation systems or portable fume extractors if necessary.
- Fire Safety: Keep a fire extinguisher nearby and remove flammable materials from the welding area. Regularly inspect and maintain equipment to prevent electrical fires.
- Work Area: Maintain a clean and organized work area to reduce the risk of accidents. Ensure that all tools and equipment are in good condition and properly stored.
- Training: Provide thorough safety training for all welding personnel, including the correct use of PPE and emergency procedures. Regularly update training programs to address new hazards and best practices.
Common Welding Hazards
- Electric Shock: Welding involves high voltage, and electric shock is a significant risk. Always check connections and ensure the equipment is properly grounded.
- Fumes and Gases: Inhaling welding fumes and gases can lead to respiratory issues and long-term health problems. Use ventilation systems and respiratory protection to mitigate this risk.
- Radiation: UV and infrared radiation from the welding arc can cause eye damage and skin burns. Wearing appropriate PPE is crucial to protect against these hazards.
- Noise: Welding operations can be noisy, leading to hearing damage over time. Use ear protection like earplugs or earmuffs in high-noise environments.
Conclusion
Welding is a critical process in various industries, providing strong and durable joints essential for manufacturing and construction. Understanding the different welding techniques, their applications, and the necessary safety measures is vital for producing high-quality welds and ensuring a safe working environment.
From MIG and TIG welding to stick and laser welding, each technique offers unique benefits and is suited for specific applications. Improving welding skills through training, practice, and proper equipment maintenance can enhance productivity and job satisfaction.
By prioritizing safety and staying informed about the latest technological advancements, welders can continue to meet the demands of modern industry while protecting their health and well-being.
Leave a Reply