Welding is a fundamental process in the manufacturing and construction industries, allowing for the joining of materials, primarily metals, through the application of heat and pressure. This technique is crucial for creating everything from small household items to large infrastructure projects, ensuring structural integrity and durability.
Understanding the types of electrical currents used in welding is essential for selecting the right method for a given application. The two primary types of current used in welding are Alternating Current (AC) and Direct Current (DC).
Alternating Current (AC) is characterized by its flow direction changing periodically. This means the electric charge oscillates back and forth, which can be beneficial in certain welding scenarios but may introduce some instability in the welding arc.
Direct Current (DC), on the other hand, involves a unidirectional flow of electric charge. This steady and continuous flow provides a more stable arc, making it easier to control and manage during the welding process.
The objective of this article is to provide a comprehensive comparison between AC and DC welding, highlighting their respective advantages, disadvantages, and suitable applications. By understanding these differences, welders and engineers can make informed decisions that enhance the quality and efficiency of their welding projects.
Overview of AC Welding (Alternating Current Welding)
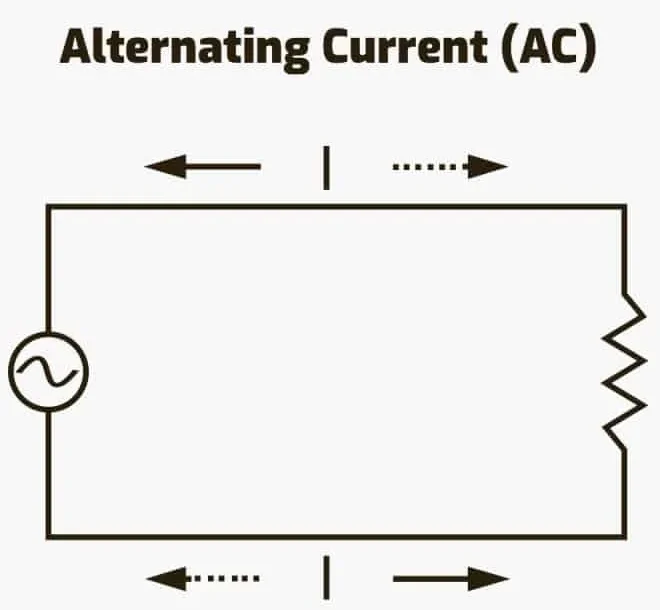
Working Principle of AC Welding
Alternating Current (AC) welding operates on the principle that the electric current reverses direction periodically. In an AC welding setup, the current flows in one direction for a half-cycle and then switches to the opposite direction for the next half-cycle. This oscillation typically occurs at a frequency of 50 or 60 Hz (cycles per second), depending on the electrical standards of the region.
The constant switching of the current direction can cause the welding arc to extinguish and reignite with each half-cycle. This phenomenon can be both an advantage and a challenge, depending on the specific welding application.
Common Applications of AC Welding
AC welding is commonly used in several applications, particularly when working with magnetic materials or in environments where arc stability is less critical. Some typical uses include:
- Welding aluminum and other non-ferrous metals.
- Applications where cost is a significant concern, such as in some construction and repair projects.
- Situations where the welder must deal with magnetized workpieces, as the alternating current can help mitigate magnetic arc blow.
Advantages of AC Welding
- Lower Cost: AC welding equipment is generally less expensive than DC welding equipment. This makes it a cost-effective choice for many applications, especially for small businesses or hobbyists.
- Self-Cleaning of the Weld Surface: The rapid switching of the current helps to clean the weld area by removing oxides and other impurities. This self-cleaning action is particularly beneficial when welding aluminum.
- Less Affected by the Magnetic Field of the Material: In scenarios where the workpiece is magnetized, DC welding can suffer from arc blow, which can cause the arc to become unstable. AC welding’s periodic current reversal can help counteract this issue, providing a more stable welding process.
Disadvantages of AC Welding
- Less Stable Arc: The inherent nature of AC, with its constant current direction changes, can lead to a less stable welding arc. This instability can make it challenging to produce consistent, high-quality welds.
- More Difficult to Control Compared to DC: Due to the arc’s instability, AC welding requires more skill and experience to manage effectively. Welders may find it harder to control the arc and achieve the desired results compared to using DC welding.
Overview of DC Welding (Direct Current Welding)
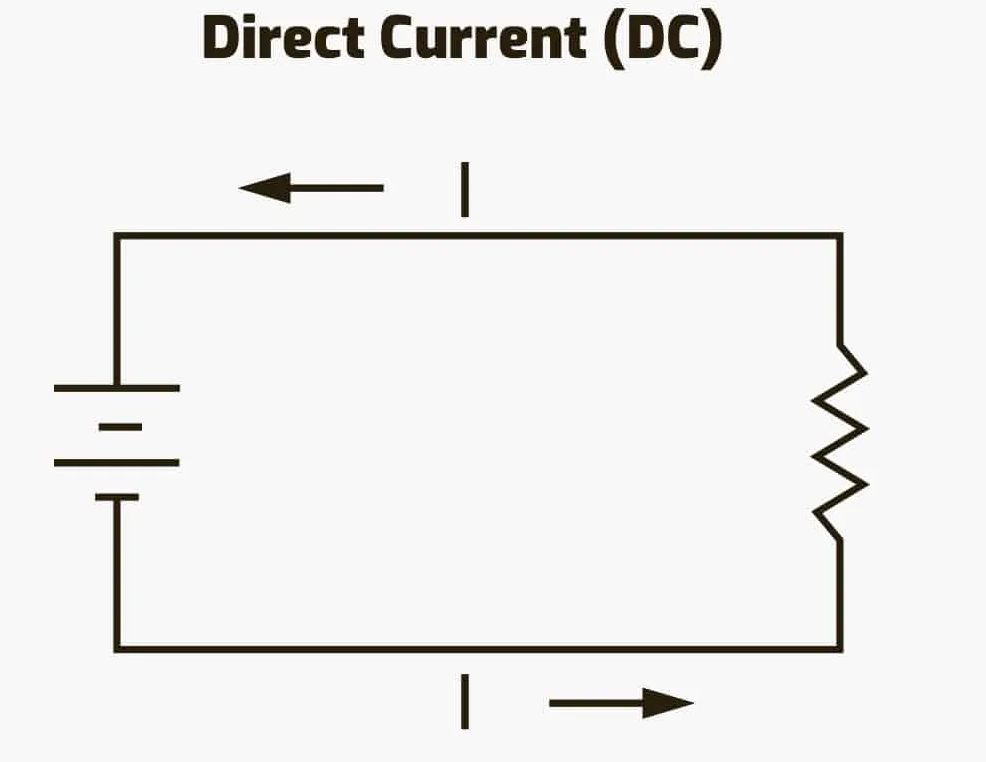
Working Principle of DC Welding
Direct Current (DC) welding operates on the principle of a unidirectional flow of electric charge. In DC welding, the current flows steadily in one direction, either from the electrode to the workpiece (DC electrode negative, DCEN) or from the workpiece to the electrode (DC electrode positive, DCEP). This constant flow of electricity provides a stable arc, which is easier to control and manage during the welding process.
Common Applications of DC Welding
DC welding is widely used in various applications due to its stability and ease of control. Some common uses include:
- Precision welding tasks requiring a stable arc and consistent results.
- Welding ferrous metals like steel and stainless steel.
- Applications requiring deep penetration and high-quality welds.
- Situations where thin materials are welded, as DC provides better control over the heat input.
Advantages of DC Welding
- More Stable Arc: DC welding provides a steady and continuous arc, making it easier to achieve consistent, high-quality welds. This stability is particularly beneficial for tasks requiring precision and accuracy.
- Better Control and Easier Adjustment of the Welding Current: The constant flow of DC allows for finer control over the welding process. Welders can easily adjust the current to suit different materials and thicknesses, resulting in better weld quality.
- Less Affected by Temperature Changes: DC welding is less sensitive to fluctuations in temperature, making it suitable for environments with varying thermal conditions. This reliability ensures consistent performance across different working conditions.
Disadvantages of DC Welding
- Higher Cost: DC welding equipment is generally more expensive than AC welding equipment. This higher initial cost can be a barrier for small businesses or hobbyists.
- More Affected by the Magnetic Field of the Material: DC welding can suffer from arc blow, a phenomenon where the arc becomes unstable due to the magnetic field of the material. This issue can make it challenging to weld magnetized workpieces or those with strong magnetic properties.
General Comparison between AC vs DC Welding
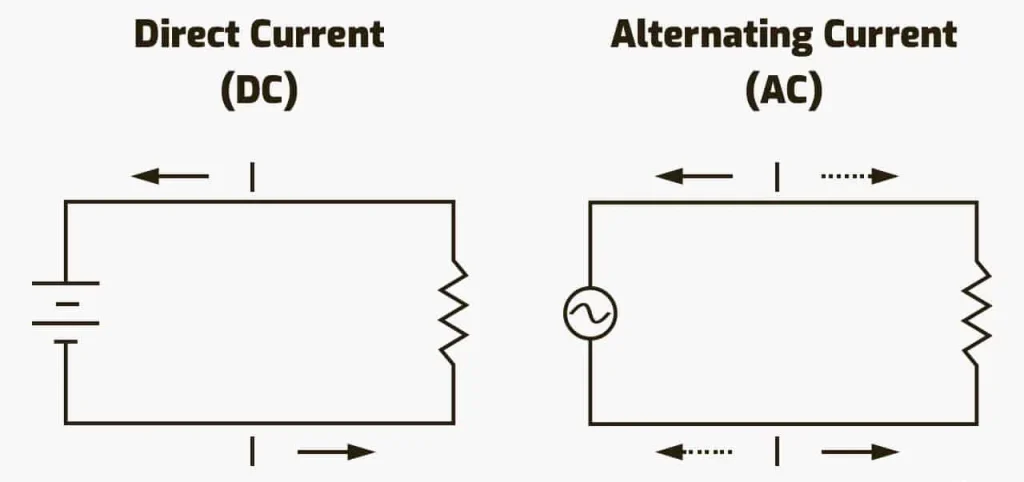
Arc Stability
One of the most significant differences between AC and DC welding is the stability of the welding arc.
- AC Welding: The arc in AC welding is less stable due to the constant change in current direction. This can result in the arc extinguishing and reigniting multiple times per second, which can cause fluctuations and make it harder to maintain a consistent weld.
- DC Welding: The arc in DC welding is much more stable because the current flows in a single direction. This stability makes DC welding easier to control, especially for precision work and when welding thin materials.
Control and Adjustability
- AC Welding: Due to the inherent instability of the arc, controlling AC welding can be more challenging. Adjusting the weld parameters to achieve the desired outcome requires more skill and experience.
- DC Welding: The stable arc in DC welding allows for better control and finer adjustments. Welders can easily manipulate the current settings to suit different materials and thicknesses, resulting in higher quality welds.
Effect of the Material’s Magnetic Field
- AC Welding: AC welding is less affected by the magnetic properties of the material being welded. The alternating nature of the current helps mitigate issues such as arc blow, which can be problematic in magnetized workpieces.
- DC Welding: DC welding can be significantly affected by the magnetic field of the material. Arc blow, caused by the interaction between the magnetic field and the unidirectional current, can lead to arc instability and inconsistent welds. This issue requires careful management, especially when working with magnetized materials.
Cost and Economic Efficiency
- AC Welding: Generally, AC welding equipment is less expensive than DC welding equipment. This cost-effectiveness makes AC welding an attractive option for budget-conscious projects or for applications where precision is not as critical.
- DC Welding: DC welding equipment tends to be more costly, both in terms of initial investment and maintenance. However, the higher cost is often justified by the improved weld quality, ease of control, and versatility in different applications.
Suitable Applications for Each Type of Welding
- AC Welding: Best suited for welding tasks where cost is a primary concern and precision is less critical. Commonly used for welding non-ferrous metals like aluminum and for projects where magnetized materials are involved.
- DC Welding: Ideal for applications requiring high-quality, precise welds. Commonly used for welding ferrous metals, in precision manufacturing, and for tasks involving thin materials or requiring deep penetration.
Factors to Consider When Choosing Between AC and DC Welding
Choosing the appropriate welding method—AC or DC—depends on various factors specific to the welding task at hand. Here are some critical factors to consider:
Type of Material Being Welded
- Ferrous Metals (e.g., Steel, Stainless Steel): DC welding is generally preferred for ferrous metals due to its stable arc and better control. It provides deeper penetration and higher-quality welds, which are essential for these materials.
- Non-Ferrous Metals (e.g., Aluminum, Magnesium): AC welding is often the go-to method for non-ferrous metals. The self-cleaning action of AC helps to remove oxides and impurities from the weld area, which is particularly beneficial when welding materials like aluminum.
Thickness of the Material
- Thin Materials: DC welding offers better control over the heat input, making it ideal for welding thin materials. The stable arc allows for precise adjustments, reducing the risk of burning through the material.
- Thick Materials: Both AC and DC welding can be used for thicker materials, but the choice often depends on other factors such as material type and welding conditions. DC welding’s deeper penetration can be advantageous for thick materials, but AC welding can also be effective in specific applications.
Working Conditions
- Indoor vs. Outdoor: DC welding tends to perform better in outdoor conditions due to its stable arc, which is less susceptible to disturbances from wind or environmental factors. However, AC welding can still be used effectively indoors where conditions are controlled.
- Wet Environments: In environments with high moisture or humidity, AC welding may have an advantage due to its self-cleaning properties, which help maintain weld quality despite potential contamination.
Magnetic Properties of the Material
- Magnetized Materials: AC welding is less affected by magnetic arc blow, making it a better choice for welding magnetized materials. The alternating current helps to counteract the magnetic fields that can cause instability in the arc.
- Non-Magnetized Materials: For non-magnetized materials, DC welding provides a more stable and controllable arc, leading to higher-quality welds.
Required Strength and Aesthetics of the Weld
- High-Strength Welds: DC welding is often preferred for applications requiring high-strength welds due to its deeper penetration and consistent weld quality. This makes it suitable for structural components and critical applications.
- Aesthetic Considerations: For welds where appearance is important, such as in artistic or decorative work, the stable arc and precise control of DC welding can produce cleaner and more visually appealing welds.
Conclusion
The choice between AC and DC welding depends on various factors, including the type of material being welded, material thickness, working conditions, magnetic properties, and the specific requirements for weld strength and aesthetics. Each welding method has its unique advantages and disadvantages, making them suitable for different applications.
AC Welding:
- Advantages: Lower cost, self-cleaning action, less affected by the magnetic field of materials.
- Disadvantages: Less stable arc, more difficult to control.
AC welding is ideal for applications where cost is a primary concern, precision is less critical, and when welding non-ferrous metals or magnetized materials.
DC Welding:
- Advantages: More stable arc, better control, less affected by temperature changes, suitable for high-strength and aesthetic welds.
- Disadvantages: Higher cost, more affected by magnetic arc blow.
DC welding is the preferred choice for applications requiring high-quality, precise welds, particularly with ferrous metals and in situations where control and stability are paramount.
Recommendations:
- For Beginners and Hobbyists: AC welding equipment might be a more cost-effective starting point, especially for general repairs and non-critical projects.
- For Professional Welders and Industrial Applications: DC welding is recommended due to its superior arc stability and control, which are crucial for high-quality and demanding welding tasks.
In conclusion, selecting the right welding method ensures the quality and efficiency of the welding process, contributing to the overall success of the project. By understanding the strengths and limitations of both AC and DC welding, welders can make informed decisions that align with their specific needs and conditions.
Leave a Reply