Welding cables are essential components in the welding industry, providing the necessary electrical connection between welding machines and the electrodes or workpieces. The efficiency and safety of welding operations significantly depend on the quality and specifications of the welding cables used. Among the various sizes available, the 1/0 welding cable is a popular choice due to its optimal balance of flexibility, durability, and current-carrying capacity.
Overview of 1 0 welding cable
Welding cables are essential components in the welding industry, providing the necessary electrical connection between welding machines and the electrodes or workpieces. The efficiency and safety of welding operations significantly depend on the quality and specifications of the welding cables used. Among the various sizes available, the 1/0 welding cable is a popular choice due to its optimal balance of flexibility, durability, and current-carrying capacity.
In this guide, we will delve into the details of 1/0 welding cables, exploring their types, specifications, and applications. Whether you are a professional welder or a DIY enthusiast, understanding these aspects will help you make informed decisions when selecting welding cables for your projects.
What is a 1/0 Welding Cable?
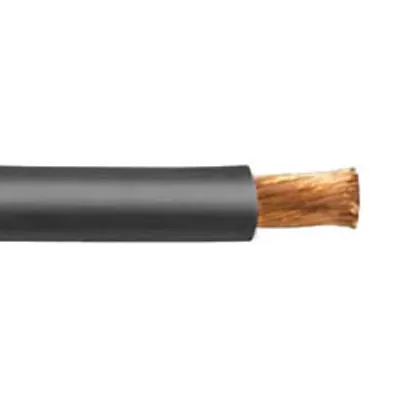
Definition and General Uses
A 1/0 welding cable, often referred to as a “one-ought” or “one-zero” cable, is a specific size of welding cable that is designed to carry a significant amount of current. The “1/0” designation indicates the American Wire Gauge (AWG) size, which is crucial in determining the cable’s capacity to handle electrical loads. This size is larger than most standard cables, making it suitable for heavy-duty welding tasks.
1/0 welding cables are commonly used in various industrial and commercial applications where high-current welding operations are performed. These cables are designed to withstand harsh environments, ensuring consistent performance even under demanding conditions. Their robust construction makes them ideal for tasks that require reliable power transmission over longer distances.
Characteristics and Features
1/0 welding cables are known for their exceptional characteristics, which contribute to their widespread use in the welding industry. Some of the key features include:
- High Flexibility: The construction of 1/0 welding cables includes numerous fine copper strands, which enhance the cable’s flexibility. This feature is particularly beneficial in welding applications that require frequent movement and bending of the cable.
- Durability: These cables are designed to be resistant to abrasion, chemicals, oils, and moisture, ensuring longevity and reliability in various working conditions.
- High Conductivity: The use of high-quality copper conductors ensures excellent electrical conductivity, minimizing voltage drops and ensuring efficient power transmission.
- Temperature Resistance: 1/0 welding cables can withstand high temperatures, making them suitable for use in environments where heat is a significant factor.
Types of 1/0 Welding Cables
Welding cables come in various types, each designed to meet specific needs and preferences. Understanding the different types of 1/0 welding cables can help you choose the most suitable option for your welding projects.
Standard 1/0 Welding Cable
Description and Uses
The standard 1/0 welding cable is the most commonly used type. It features a robust construction with numerous fine copper strands bundled together and insulated with a durable jacket. This type of cable is versatile and can be used in a wide range of welding applications, from light to heavy-duty tasks.
Standard 1/0 welding cable is ideal for:
- General Welding: Suitable for MIG, TIG, and Stick welding processes.
- Industrial Applications: Frequently used in construction sites, shipyards, and fabrication shops.
- Home and DIY Projects: Excellent choice for hobbyists and small-scale welding projects.
1/0 Ultra Flex Welding Cable
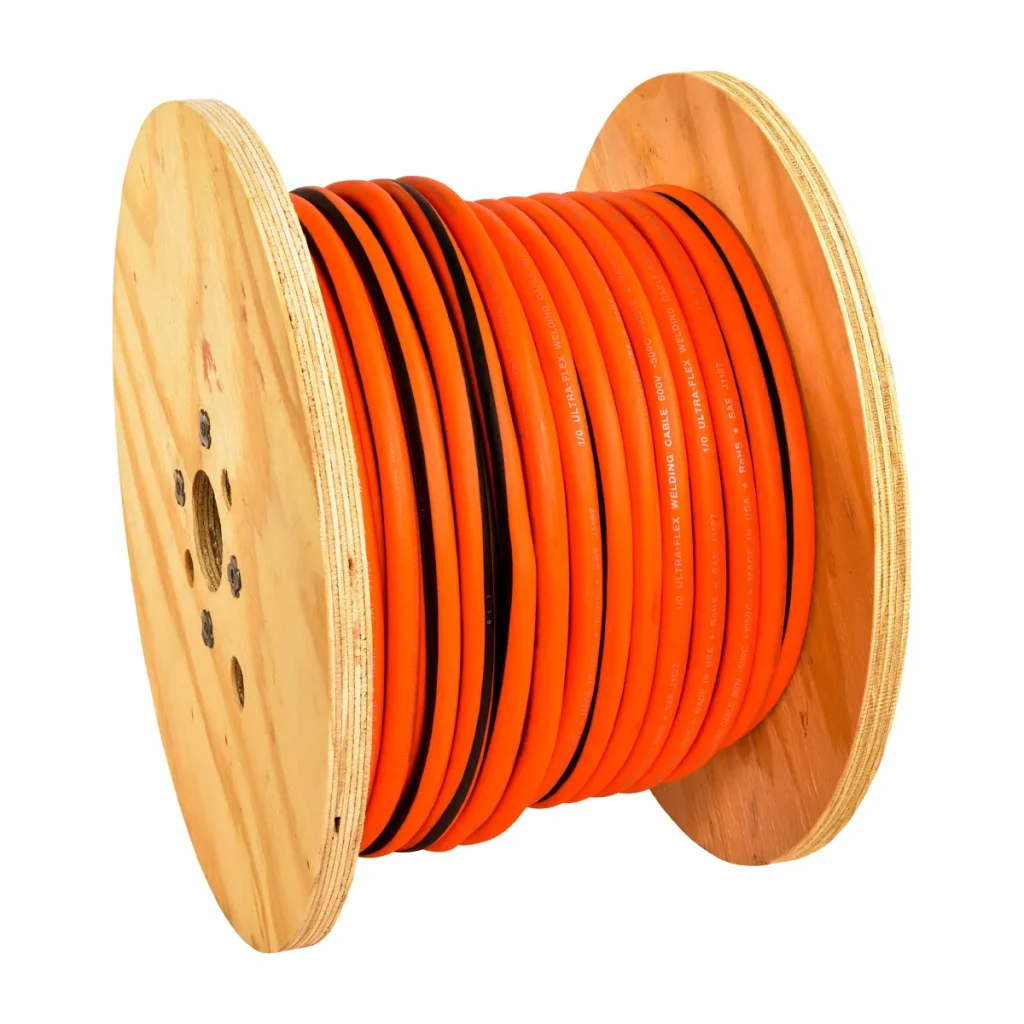
Unique Features
The 1/0 ultra flex welding cable is designed to provide even greater flexibility than the standard version. This is achieved by using a higher number of finer copper strands and a more pliable insulation material. The ultra flex design allows for easier handling and maneuverability, especially in confined spaces or when the cable needs to be frequently repositioned.
Advantages Over Standard Cables
- Enhanced Flexibility: The increased number of finer copper strands allows the cable to bend and flex more easily without compromising its structural integrity.
- Improved Handling: Easier to coil, uncoil, and route around obstacles, making it ideal for applications requiring high mobility.
- Increased Durability: The flexible insulation is typically more resistant to cracking and damage caused by repeated bending and twisting.
The 1/0 ultra flex welding cable is particularly beneficial in situations where standard cables may be too rigid or cumbersome to work with. It offers superior performance in terms of flexibility and durability, making it a preferred choice for many professional welders.
Specifications of 1/0 Welding Cables
Understanding the specifications of 1/0 welding cables is crucial for selecting the right cable for your needs. These specifications determine the cable’s performance, compatibility, and safety.
Diameter
Standard Diameter of 1/0 Welding Cables
The diameter of a 1/0 welding cable is an important specification that affects its current-carrying capacity and overall performance. Typically, a 1/0 welding cable has a diameter of approximately 0.53 inches (13.46 mm). This size allows it to handle substantial currents without overheating or experiencing significant voltage drops.
Comparison with Other Sizes
When compared to other welding cable sizes, the 1/0 welding cable falls between the smaller and larger options. For instance:
- 2 AWG Welding Cable: Smaller in diameter, handling less current, and suitable for lighter welding tasks.
- 2/0 Welding Cable: Larger in diameter, capable of carrying higher currents, and used for more demanding welding applications.
Choosing the right diameter depends on the specific requirements of your welding project, including the type of welding process, distance, and power source.
Length Options
Common Lengths Available (e.g., 100 ft)
Welding cables are available in various lengths to accommodate different applications and setups. One of the most popular lengths for 1/0 welding cables is 100 feet. This length provides a good balance between flexibility and reach, allowing welders to move around freely without needing to frequently reposition their power source.
Other common lengths include:
- 25 ft and 50 ft: Suitable for smaller workspaces or when the power source is close to the welding area.
- 150 ft and 200 ft: Ideal for larger work areas or when the power source is farther away from the welding site.
How to Choose the Right Length
When selecting the length of your welding cable, consider the following factors:
- Workspace Size: Measure the distance between your power source and the welding area to determine the minimum length required.
- Mobility Needs: If you need to move around frequently, choose a longer cable to avoid constant repositioning.
- Power Loss: Longer cables can experience voltage drops, so ensure the length you choose does not compromise the efficiency of your welding operations.
Applications of 1/0 Welding Cables
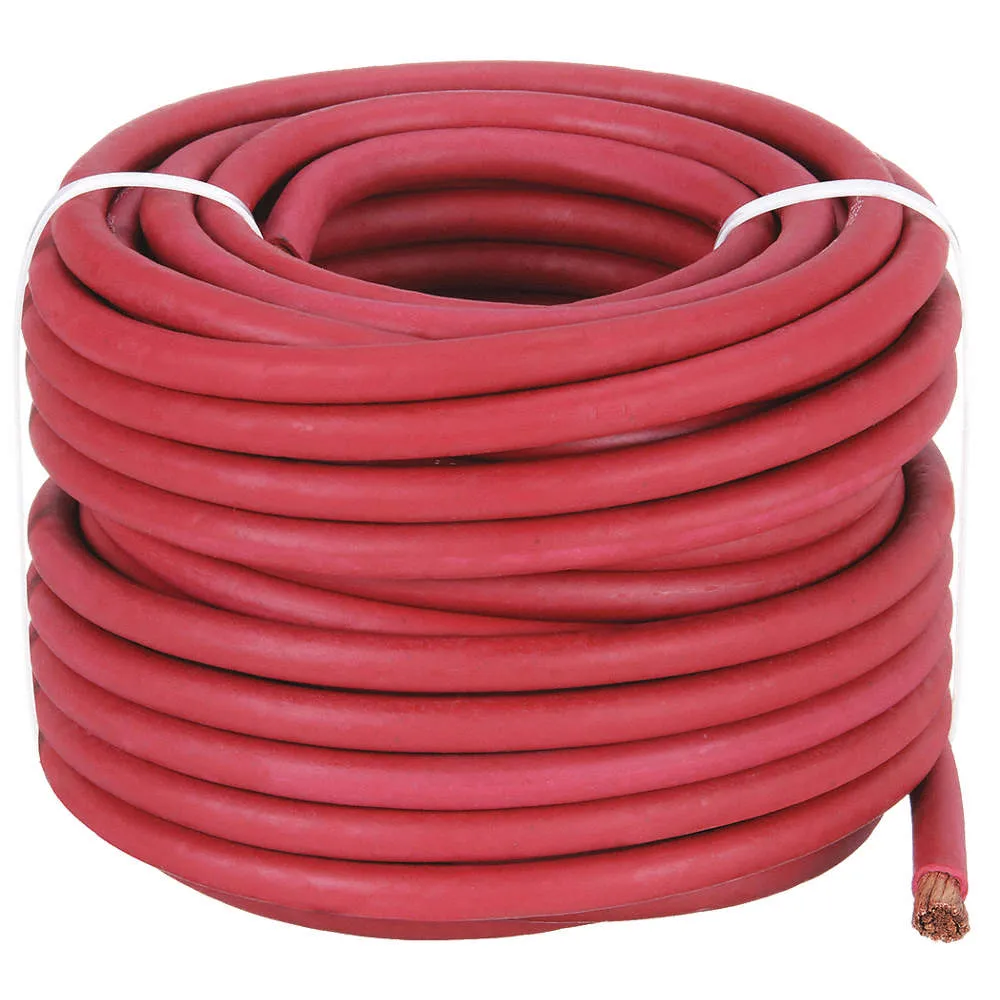
1/0 welding cables are versatile tools used across a variety of applications due to their ability to handle high currents and their durability. Below are some of the primary applications of these cables:
Industrial Uses
In industrial settings, 1/0 welding cables are essential for heavy-duty welding tasks. Industries that commonly use these cables include:
- Construction: Used for structural welding on buildings, bridges, and other infrastructure projects.
- Manufacturing: Employed in the fabrication of machinery, vehicles, and other metal products.
- Shipbuilding: Crucial for welding tasks in shipyards, where large-scale welding is necessary.
Home and DIY Projects
1/0 welding cables are also popular among home welders and DIY enthusiasts. They provide the robustness needed for various projects, such as:
- Automotive Repairs: Ideal for welding tasks in auto repair and restoration projects.
- Metal Art and Sculptures: Used by artists and hobbyists for creating metal artworks and sculptures.
- Home Improvement: Suitable for various home improvement projects that require welding, such as building metal fences or gates.
Safety Considerations
Safety is a critical aspect when working with welding cables. 1/0 welding cables are designed to meet stringent safety standards, ensuring:
- Electrical Insulation: The insulation material protects against electrical shocks and prevents short circuits.
- Heat Resistance: The cables can withstand high temperatures without degrading, reducing the risk of fires.
- Durability: The rugged construction ensures the cable can endure physical wear and tear, minimizing the risk of damage during use.
Benefits of Using 1/0 Welding Cables
Choosing the right welding cable can significantly impact the efficiency and safety of your welding projects. Here are some of the key benefits of using 1/0 welding cables:
Durability and Flexibility
1/0 welding cables are known for their exceptional durability. The high-quality materials used in their construction make them resistant to:
- Abrasion: The outer jacket protects against cuts and scrapes.
- Chemicals: Resistance to oils, solvents, and other chemicals ensures longevity.
- Moisture: The cables are designed to perform well even in humid or wet conditions.
Their flexibility is another major advantage. The fine copper strands and pliable insulation allow for easy maneuverability, which is particularly useful in tight or complex welding environments.
Conductivity and Performance
The high conductivity of 1/0 welding cables ensures efficient power transmission, which is critical for maintaining stable welding arcs. Key performance benefits include:
- Minimal Voltage Drop: High-quality copper conductors reduce voltage drop over long distances, ensuring consistent welding performance.
- Stable Current Flow: The cables are capable of handling high currents without overheating, providing a stable and reliable power source.
Cost-Effectiveness
While 1/0 welding cables may have a higher initial cost compared to smaller or lower-quality cables, their long-term benefits make them a cost-effective choice. Factors contributing to their cost-effectiveness include:
- Longevity: The durable construction reduces the need for frequent replacements.
- Efficiency: High conductivity and performance minimize energy losses, reducing overall operational costs.
- Safety: Reduced risk of electrical hazards lowers potential costs related to accidents and equipment damage.
How to Choose the Right 1/0 Welding Cable
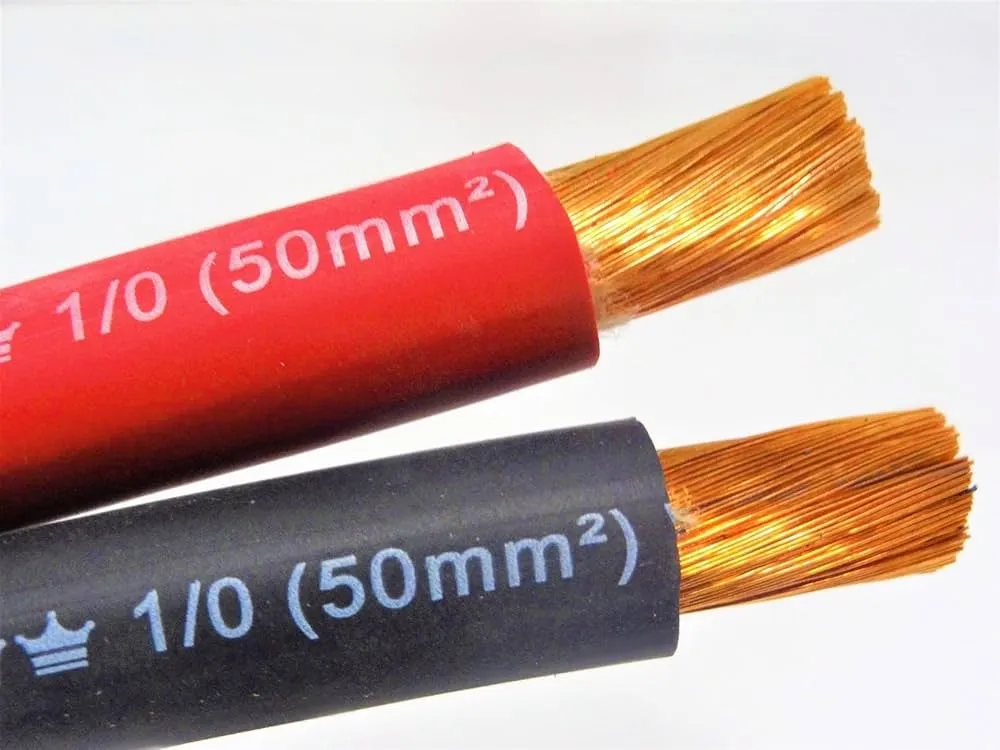
Selecting the right 1/0 welding cable for your specific needs involves considering several factors to ensure optimal performance and safety. Here are some key considerations:
Factors to Consider
- Environment: Consider the working environment. For example, if you are working in a harsh industrial setting, choose a cable with a robust outer jacket that can withstand physical wear and exposure to chemicals.
- Power Requirements: Ensure the cable can handle the current required for your welding machine and the specific welding tasks you are performing.
- Flexibility Needs: If you need to maneuver the cable frequently or work in tight spaces, opt for an ultra-flex cable.
Tips for Purchasing
- Check Specifications: Verify the specifications of the cable, including the diameter, length, and insulation type, to ensure they meet your requirements.
- Quality and Brand: Choose cables from reputable manufacturers known for quality and reliability.
- Reviews and Recommendations: Look for reviews and recommendations from other welders to gauge the performance and durability of the cable.
Installation and Maintenance
Proper installation and maintenance of 1/0 welding cables are essential to ensure their longevity and optimal performance. Here are some best practices for installing and maintaining these cables:
Proper Installation Techniques
- Correct Sizing: Ensure that the cable is the appropriate size for the welding machine and the task at hand. Using an undersized cable can lead to overheating and potential safety hazards.
- Secure Connections: Make sure all connections are tight and secure. Loose connections can lead to arcing and damage to the cable or welding machine.
- Avoid Sharp Bends: When routing the cable, avoid sharp bends or kinks, which can damage the internal copper strands and reduce the cable’s lifespan.
- Use Cable Clamps: Employ cable clamps or ties to keep the cable organized and prevent it from getting tangled or damaged during use.
- Protection from Elements: If working outdoors or in harsh environments, protect the cable from direct exposure to elements such as rain, snow, or excessive sunlight, which can degrade the insulation over time.
Maintenance Tips for Longevity
- Regular Inspections: Periodically inspect the cable for any signs of wear, such as cracks in the insulation, exposed copper strands, or corrosion at the connections.
- Cleanliness: Keep the cable clean by wiping it down after use. Dirt and debris can cause abrasion and damage to the insulation.
- Proper Storage: Store the cable in a cool, dry place when not in use. Avoid coiling the cable too tightly, as this can cause stress and damage over time.
- Monitor Performance: Pay attention to any changes in welding performance, such as inconsistent arcs or overheating, which may indicate an issue with the cable.
- Replace When Necessary: If the cable shows significant signs of wear or damage, replace it promptly to avoid safety hazards and ensure continued efficient performance.
Conclusion
The 1/0 welding cable is a vital component for many welding operations, offering a balance of durability, flexibility, and high current-carrying capacity. By understanding the types, specifications, and proper usage of these cables, you can enhance the efficiency and safety of your welding projects. Whether you’re working in an industrial setting or tackling DIY tasks at home, choosing the right 1/0 welding cable and maintaining it properly will contribute to successful and safe welding experiences.
Frequently Asked Questions (FAQs)
1. What is the difference between standard 1/0 welding cable and 1/0 ultra flex welding cable?
- Answer: The primary difference lies in the flexibility. Ultra flex welding cables have a higher number of finer copper strands and a more pliable insulation, making them more flexible and easier to maneuver compared to standard welding cables.
2. How do I determine the correct length of 1/0 welding cable for my needs?
- Answer: Measure the distance between your welding machine and the work area. Consider additional length for mobility and routing around obstacles. Common lengths range from 25 ft to 200 ft, with 100 ft being a popular choice for its balance of reach and flexibility.
3. Can I use a 1/0 welding cable for other applications besides welding?
- Answer: Yes, 1/0 welding cables can be used for other high-current applications such as power leads for inverters, battery cables, and industrial machinery connections, provided they meet the required specifications.
4. What should I do if my welding cable shows signs of wear or damage?
- Answer: Inspect the cable regularly for any signs of wear or damage. If you notice cracks in the insulation, exposed copper strands, or corrosion at the connections, replace the cable promptly to maintain safety and performance.
5. How can I ensure the longevity of my 1/0 welding cable?
- Answer: Follow proper installation techniques, perform regular inspections, keep the cable clean, store it properly, and monitor its performance. Avoid sharp bends, secure all connections, and replace the cable when necessary.
Leave a Reply