In the world of welding, selecting the right welding wire is crucial for achieving strong, reliable welds. Among the various options available, the 0.035-inch welding wire is highly regarded for its versatility and efficiency. This guide will explore the characteristics, applications, and best practices for using 0.035-inch welding wire, helping you make informed decisions for your welding projects.
What is 0.035 Inch Welding Wire?
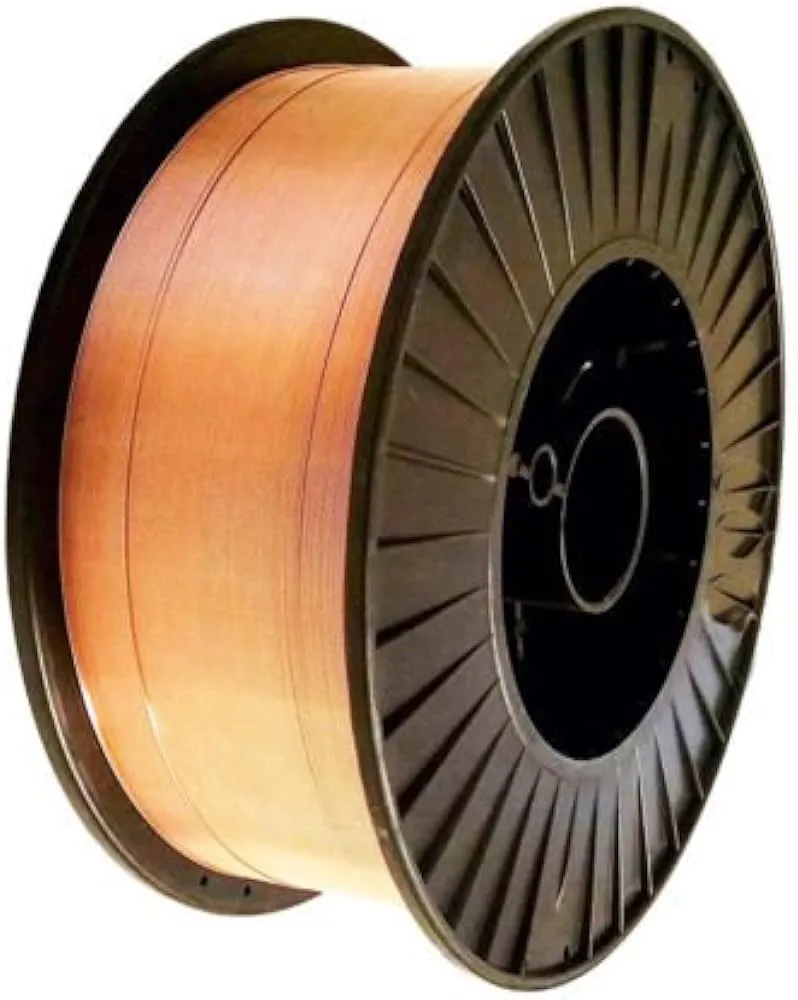
Definition and Characteristics
0.035-inch welding wire, commonly used in MIG (Metal Inert Gas) welding, is a consumable electrode with a diameter of 0.035 inches, equivalent to approximately 0.9 millimeters. This welding wire is available in various materials, including mild steel, stainless steel, and aluminum, each suited to different welding tasks. The diameter of 0.035 inches strikes a balance between strength and flexibility, making it a popular choice for both professional welders and hobbyists.
Key characteristics of 0.035-inch welding wire include:
- Versatility: Suitable for a range of welding applications.
- Strength: Provides robust welds on medium-gauge metal sheets and tubing.
- Ease of Use: Balances manageability and performance, ideal for diverse welding projects.
Common Applications
The versatility of 0.035-inch welding wire makes it a preferred choice for numerous applications across various industries. Some common uses include:
- Automotive Repairs: Ideal for welding car panels, frames, and exhaust systems.
- Construction Projects: Suitable for fabricating structural components and metal frameworks.
- Manufacturing: Used in the production of machinery, equipment, and metal goods.
- DIY Projects: Popular among hobbyists for home repairs and metalworking crafts.
035 welding wire 33 lbs
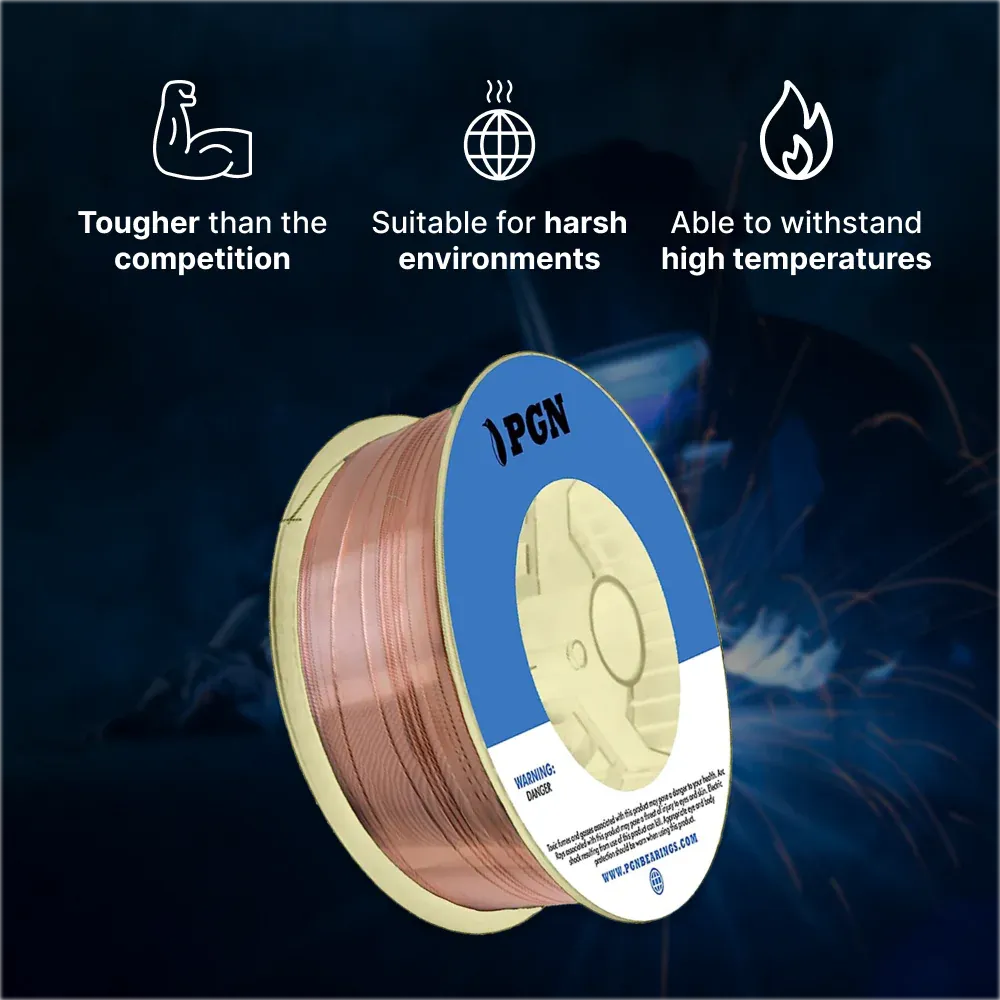
Overview
A 33 lbs spool of 0.035-inch welding wire is a common size used in various welding settings. This spool size is particularly beneficial for extended welding sessions, minimizing the need for frequent spool changes. The 33 lbs weight provides a substantial amount of wire, making it suitable for both industrial and large-scale projects.
Advantages and Disadvantages
Advantages
- Extended Use: With a 33 lbs spool, welders can work longer without interruptions, which is particularly advantageous in large projects or continuous production environments.
- Cost-Effective: Purchasing in larger quantities often reduces the cost per pound of wire, offering economic benefits over smaller spools.
- Consistency: Larger spools tend to feed more consistently, reducing the chances of wire feed issues that can disrupt welding quality.
Disadvantages
- Weight: The spool’s weight can be cumbersome, making it more challenging to handle and install, especially in mobile or less-equipped workspaces.
- Storage Requirements: Adequate storage space is necessary to keep the wire in optimal condition, preventing rust and contamination.
Suitable Applications and Fields of Use
The 33 lbs spool of 0.035-inch welding wire is suitable for various applications, particularly those requiring prolonged welding activities. Common fields of use include:
- Industrial Settings: Ideal for manufacturing plants where consistent, high-volume welding is required.
- Construction: Suitable for large-scale construction projects, such as building frames and heavy machinery.
- Automotive Industry: Used in the fabrication and repair of vehicle components.
- Metal Fabrication: Essential for creating and repairing metal structures and products.
Tips for Effective Storage and Usage
- Dry Storage: Store the spool in a dry, cool place to prevent rust and corrosion, which can compromise weld quality.
- Proper Handling: Use appropriate spool holders or carts to manage the weight and facilitate easy installation.
- Clean Environment: Maintain a clean welding environment to avoid contamination of the wire, ensuring better welds.
0.035 Inch Welding Wire 44 lbs
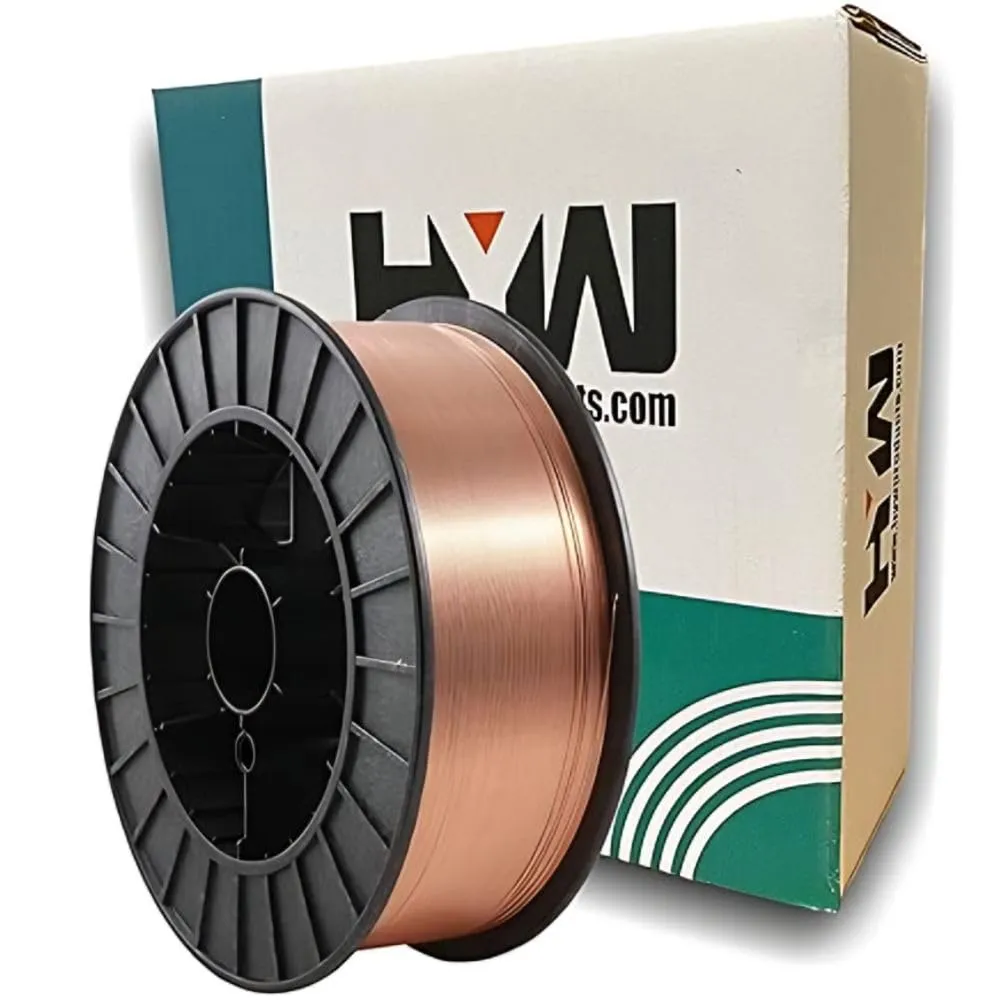
Overview
The 44 lbs spool of 0.035-inch welding wire is designed for very high-demand welding environments. This spool size is typically used in large-scale industrial applications where minimizing downtime is critical. The 44 lbs weight provides a significant amount of wire, allowing for extensive welding without the need for frequent spool changes.
Advantages and Disadvantages
Advantages
- Maximum Efficiency: The larger spool size means fewer interruptions for spool changes, leading to increased productivity and efficiency in welding operations.
- Cost Savings: Purchasing wire in bulk often results in lower costs per pound, making the 44 lbs spool more economical over time.
- Consistency and Quality: Fewer wire feed issues are encountered with larger spools, ensuring smoother and more reliable welding performance.
Disadvantages
- Heavier Weight: The 44 lbs spool is significantly heavier, which can make it more challenging to handle and install, especially without the proper equipment.
- Storage Space: Requires ample storage space to keep the wire in good condition, free from moisture and contaminants.
Suitable Applications and Fields of Use
The 44 lbs spool of 0.035-inch welding wire is best suited for applications that demand continuous and high-volume welding. Common fields of use include:
- Large-Scale Industrial Applications: Perfect for industries that require non-stop welding, such as shipbuilding and heavy machinery manufacturing.
- Construction: Used in the construction of large structures, bridges, and infrastructure projects.
- Fabrication: Ideal for extensive metal fabrication projects where large quantities of welding wire are necessary.
Tips for Effective Storage and Usage
- Controlled Environment: Store the spool in a controlled environment with stable humidity and temperature to prevent rust and degradation.
- Spool Management: Utilize industrial-grade spool holders or carts designed to handle the weight and size of the 44 lbs spool.
- Regular Inspection: Regularly inspect the wire for any signs of damage or contamination before use to ensure optimal welding performance.
Comparison Between 0.035 Inch Welding Wire 33 lbs and 44 lbs
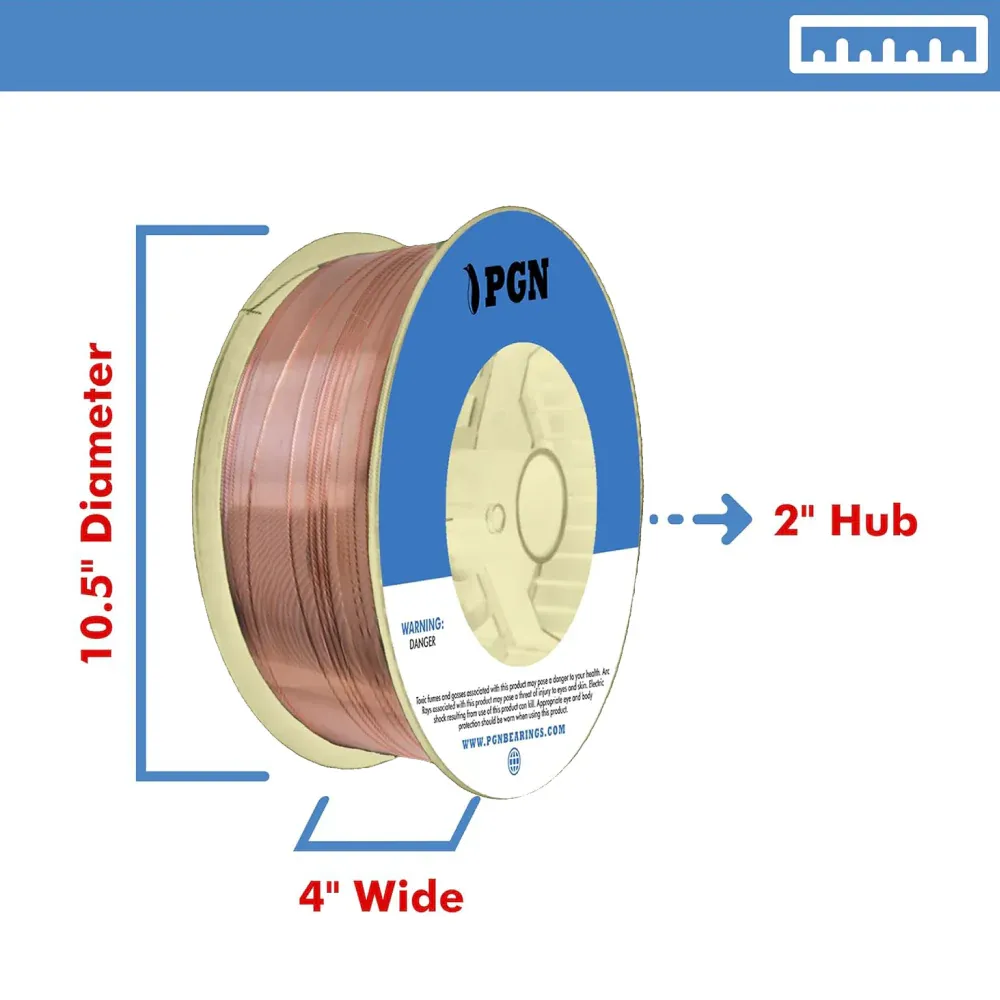
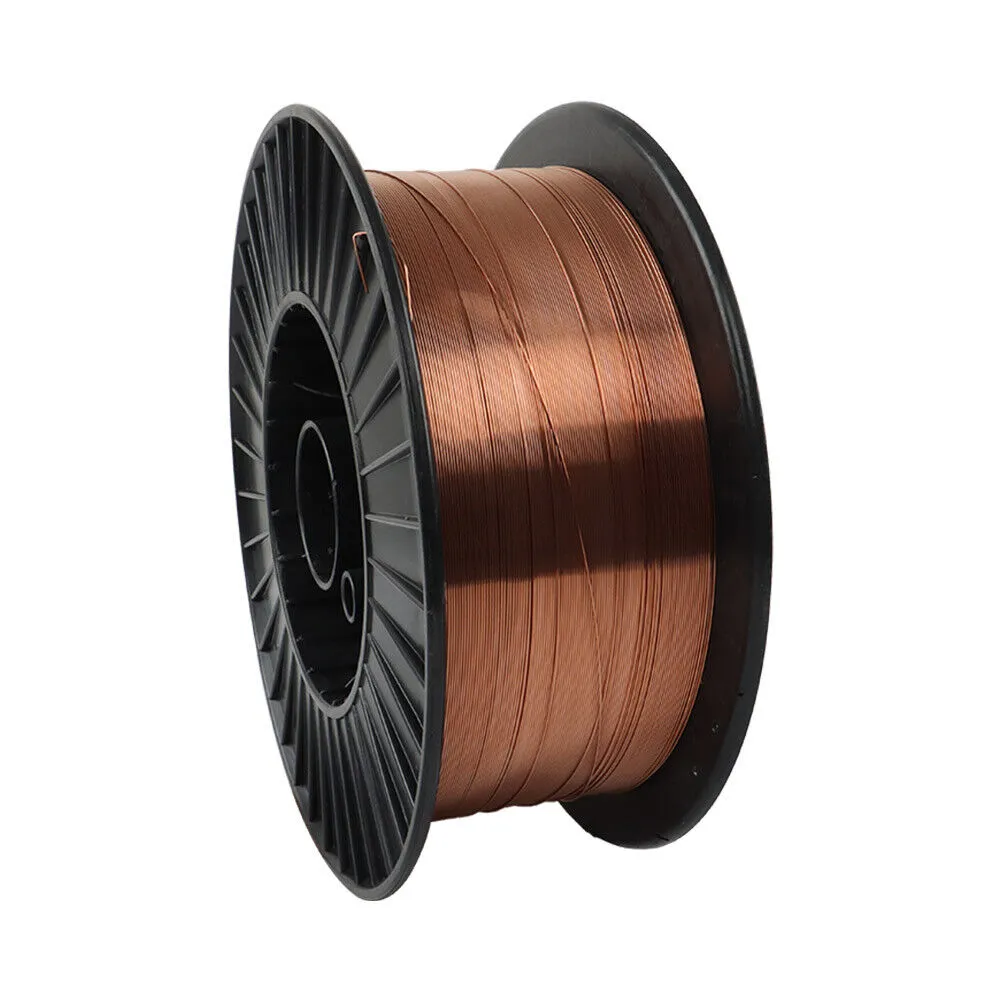
Key Differences
When comparing the 33 lbs and 44 lbs spools of 0.035-inch welding wire, several key differences emerge that can influence your choice based on the specific needs of your project.
- Weight and Handling:
- 33 lbs Spool: Easier to handle and install, making it suitable for medium to large projects where mobility and ease of use are important.
- 44 lbs Spool: Heavier and more cumbersome, requiring more effort and appropriate equipment to manage effectively. Best suited for stationary, high-demand environments.
- Application Scale:
- 33 lbs Spool: Ideal for projects that are substantial but not continuous, such as automotive repairs and medium-scale construction tasks.
- 44 lbs Spool: Designed for very large-scale and continuous welding operations, such as shipbuilding, heavy machinery manufacturing, and extensive industrial fabrication.
- Cost Efficiency:
- 33 lbs Spool: Offers a balance between quantity and manageability, often providing good value for medium-scale projects.
- 44 lbs Spool: Generally more cost-effective per pound, providing bulk savings that are advantageous for high-volume welding operations.
- Storage Requirements:
- 33 lbs Spool: Requires less storage space and can be more easily accommodated in smaller workshops or mobile welding setups.
- 44 lbs Spool: Demands more storage space and a controlled environment to ensure the wire remains in optimal condition.
Choosing the Right Welding Wire for Your Needs
Selecting the appropriate spool size depends on various factors, including the scale of your project, frequency of welding, and storage capabilities. Here are some considerations to help you make the right choice:
- Project Size: For medium to large projects, a 33 lbs spool is generally sufficient. However, for very large-scale or continuous projects, the 44 lbs spool is more appropriate.
- Frequency of Use: If you weld frequently, investing in a 44 lbs spool may be more economical and convenient, reducing the frequency of spool changes and potential downtime.
- Storage Capabilities: Ensure you have the necessary space and proper storage conditions to maintain the quality of the welding wire, especially if opting for the larger 44 lbs spool.
Guide to Buying 0.035 Inch Welding Wire
Factors to Consider
When purchasing 0.035-inch welding wire, several factors should be taken into account to ensure you select the best wire for your specific welding needs. These considerations will help you achieve optimal performance and results in your welding projects.
- Material:
- Mild Steel: Commonly used for general-purpose welding. It’s versatile and cost-effective, making it suitable for a wide range of applications.
- Stainless Steel: Provides corrosion resistance and is ideal for welding stainless steel materials. It’s used in environments where the weld needs to withstand harsh conditions.
- Aluminum: Lightweight and used for welding aluminum and other non-ferrous metals. It requires specific settings and techniques.
- Spool Size:
- 33 lbs Spool: Suitable for medium to large projects, offering a balance between quantity and ease of handling.
- 44 lbs Spool: Best for high-demand, continuous welding applications, providing more wire and reducing the need for frequent spool changes.
- Brand Reputation:
- Choose brands known for their quality and reliability. Reputable brands ensure consistent performance, which is crucial for achieving strong, reliable welds.
- Cost:
- Compare prices to find the best deal without compromising on quality. Consider the cost per pound of wire and any potential savings from buying in bulk.
Reviews of Popular and High-Quality Brands
- Lincoln Electric:
- Lincoln Electric is renowned for its high-quality welding products. Their 0.035-inch welding wire is praised for its consistent performance and reliability.
- Pros: High-quality, consistent feed, strong welds.
- Cons: Slightly higher price compared to some competitors.
- Hobart:
- Hobart offers a range of welding wires that are well-regarded in the welding community. Their wires are known for reliability and ease of use.
- Pros: Reliable, easy to use, good quality.
- Cons: Availability can be limited in some regions.
- ER70S-6:
- This type of wire is a popular choice for mild steel welding. It offers good weldability and produces clean, strong welds.
- Pros: Good weldability, clean welds, affordable.
- Cons: Not suitable for stainless steel or aluminum.
- Forney:
- Forney provides affordable options that do not compromise on quality. Their 0.035-inch welding wire is suitable for both hobbyists and professionals.
- Pros: Affordable, good quality, versatile.
- Cons: May require more frequent adjustments during welding.
Conclusion
Summary of Main Points
0.035-inch welding wire is a versatile and essential tool for many welding applications. Its balanced diameter makes it suitable for welding a wide range of materials, from mild steel to stainless steel and aluminum. Choosing between the 33 lbs and 44 lbs spools depends on the scale and frequency of your welding projects, as well as your storage capabilities. The 33 lbs spool is ideal for medium to large projects, while the 44 lbs spool is best for high-demand, continuous welding operations. Factors such as the material of the wire, spool size, brand reputation, and cost should all be considered when purchasing welding wire.
Final Advice on Selecting and Using 0.035-Inch Welding Wire
When selecting 0.035-inch welding wire, always consider the specific requirements of your project. Ensure that the wire material matches the metal you will be welding. Proper storage and handling are crucial to maintaining the quality of the wire. Keep the wire in a dry, clean environment, and use appropriate spool holders to manage the weight. By choosing the right wire and following best practices, you can achieve strong, reliable welds that meet your project’s needs.
FAQs (Frequently Asked Questions)
What Materials Can 0.035-Inch Welding Wire Be Used For?
0.035-inch welding wire is suitable for welding a variety of materials, including mild steel, stainless steel, and aluminum. The specific type of wire chosen should match the material being welded for optimal results. For example, use mild steel wire for general-purpose welding, stainless steel wire for corrosion-resistant applications, and aluminum wire for lightweight, non-ferrous metals.
How to Effectively Store Welding Wire?
To effectively store welding wire, follow these tips:
- Dry Environment: Store the wire in a dry, cool place to prevent rust and corrosion.
- Sealed Containers: Use sealed containers or plastic bags to protect the wire from moisture and contaminants.
- Proper Handling: Handle the spools carefully to avoid damaging the wire. Use spool holders or carts for larger spools.
- Regular Inspection: Regularly inspect the wire for any signs of damage or contamination before use.
Differences Between 0.035-Inch Welding Wire and Other Sizes?
0.035-inch welding wire offers a balance between strength and ease of use, making it suitable for a wide range of applications. Other sizes, such as 0.030-inch or 0.045-inch wires, may be more appropriate for lighter or heavier welding tasks, respectively. The choice of wire size depends on the thickness of the material and the specific requirements of the welding project. For example:
- 0.030-Inch Wire: Better for thinner materials and light-duty welding.
- 0.045-Inch Wire: Suitable for thicker materials and heavy-duty welding tasks.
By understanding these differences, you can select the most appropriate wire size for your welding needs.
Leave a Reply