Introduction to 030 Flux Core Welding Wire
Flux Core Welding Wire Explanation
Flux core welding wire is a type of welding wire that is used in flux-cored arc welding (FCAW). FCAW is a semi-automatic or automatic arc welding process that uses a continuously-fed consumable electrode containing a flux and a constant-voltage welding power supply. The process can be used with or without a shielding gas, depending on the type of flux core wire being used. This method is popular for its high welding speed and portability, making it a preferred choice for many industrial applications.
The core of flux-cored wire contains fluxing agents and other ingredients that help produce a protective gas shield, reduce oxidation, and improve the stability of the arc during welding. When the wire melts, the flux within the core vaporizes to form a gas that shields the weld pool from atmospheric contamination. This process helps ensure the integrity and strength of the weld.
Characteristics of 030 Flux Core Welding Wire
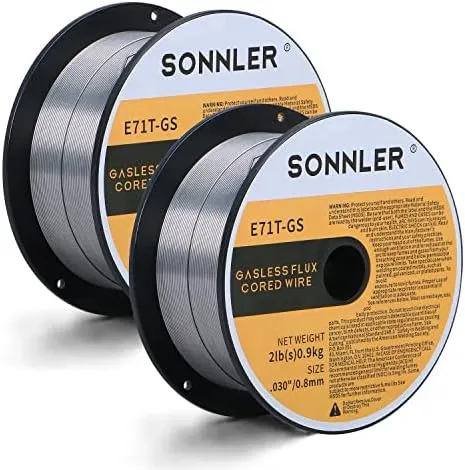
The 030 flux core welding wire, often designated as .030″ (0.8mm) in diameter, is one of the common sizes used in FCAW. It has specific characteristics that make it suitable for a range of applications:
- Versatility: The .030″ flux core wire is suitable for welding thinner materials, typically ranging from 18 gauge up to 1/4 inch thick. This makes it ideal for automotive repair, light structural work, and maintenance.
- Ease of Use: This wire size is easier to control compared to thicker wires, making it a good choice for novice welders or for those working on detailed projects that require precision.
- Penetration and Bead Profile: The .030″ wire provides good penetration and a smooth bead profile, which is essential for achieving strong, clean welds.
- Compatibility: The .030″ flux core wire can be used with most FCAW-capable welding machines. It operates well with both gasless (self-shielded) and gas-shielded setups, providing flexibility depending on the specific welding requirements and environment.
- Performance in Various Positions: This wire performs well in various welding positions, including flat, horizontal, vertical, and overhead, making it a versatile choice for different welding scenarios.
Lincoln 030 Flux Core Wire
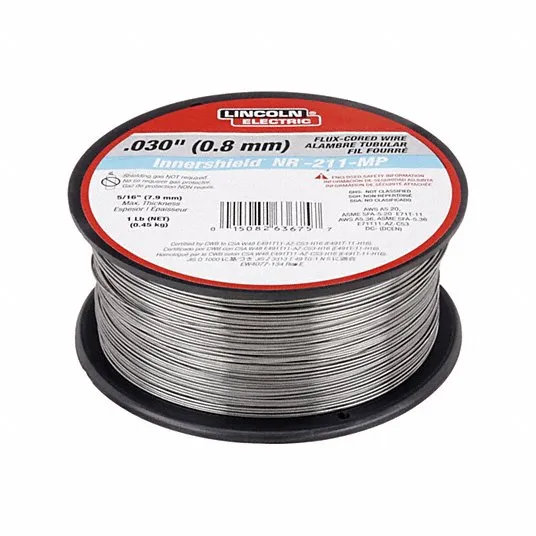
Introduction to Lincoln
Lincoln Electric is a renowned global manufacturer of welding products and a leading provider of welding solutions. Established in 1895, Lincoln has a long history of innovation and excellence in the welding industry. The company is known for its high-quality welding equipment, consumables, and automation solutions. Lincoln Electric’s commitment to quality and performance has made it a trusted name among professional welders and hobbyists alike.
Components and Quality of Lincoln 030 Flux Core Wire
Lincoln’s 030 flux core wire is designed with the needs of welders in mind, offering exceptional quality and reliability. Key components and aspects of this wire include:
- Core Composition: The flux core of Lincoln’s 030 wire contains a carefully formulated blend of fluxing agents, deoxidizers, and alloying elements. This formulation helps to produce a stable arc, minimize spatter, and ensure a clean weld.
- Outer Shell: The outer shell of the wire is made from high-quality steel, which provides durability and strength. This ensures consistent feedability and reduces the risk of wire breakage during welding.
- Quality Control: Lincoln Electric employs stringent quality control measures to ensure that each spool of 030 flux core wire meets the highest standards. This includes rigorous testing for chemical composition, mechanical properties, and weldability.
- Packaging: Lincoln’s 030 flux core wire is typically available in various spool sizes, including 1 lb, 2 lb, and 10 lb spools, catering to different usage needs. The packaging is designed to protect the wire from moisture and contaminants, preserving its quality and performance.
Advantages and Disadvantages of Lincoln 030 Flux Core Wire
Advantages:
- Consistent Performance: Lincoln’s 030 flux core wire is known for its consistent performance, providing a stable arc and smooth weld bead. This reliability makes it a preferred choice for many professional welders.
- High-Quality Welds: The wire’s composition ensures minimal spatter and excellent bead appearance, resulting in high-quality welds with good penetration and strength.
- Versatility: Suitable for various applications, including automotive repair, construction, and maintenance, the 030 wire from Lincoln is versatile and can be used in different welding positions.
- Ease of Use: Lincoln’s 030 flux core wire is user-friendly, making it an excellent option for both beginners and experienced welders. Its smooth feedability and stable arc make it easier to achieve precise welds.
Disadvantages:
- Cost: Lincoln Electric’s products are often priced higher than some competitors. While the quality justifies the cost, it might be a consideration for budget-conscious users.
- Availability: Depending on the region, there might be limited availability of Lincoln’s welding products, requiring users to source them from specific suppliers or online retailers.
- Smoke and Fumes: Like all flux core wires, Lincoln’s 030 wire produces smoke and fumes during welding, which necessitates proper ventilation and safety measures.
030 Flux Core Wire 10 lb
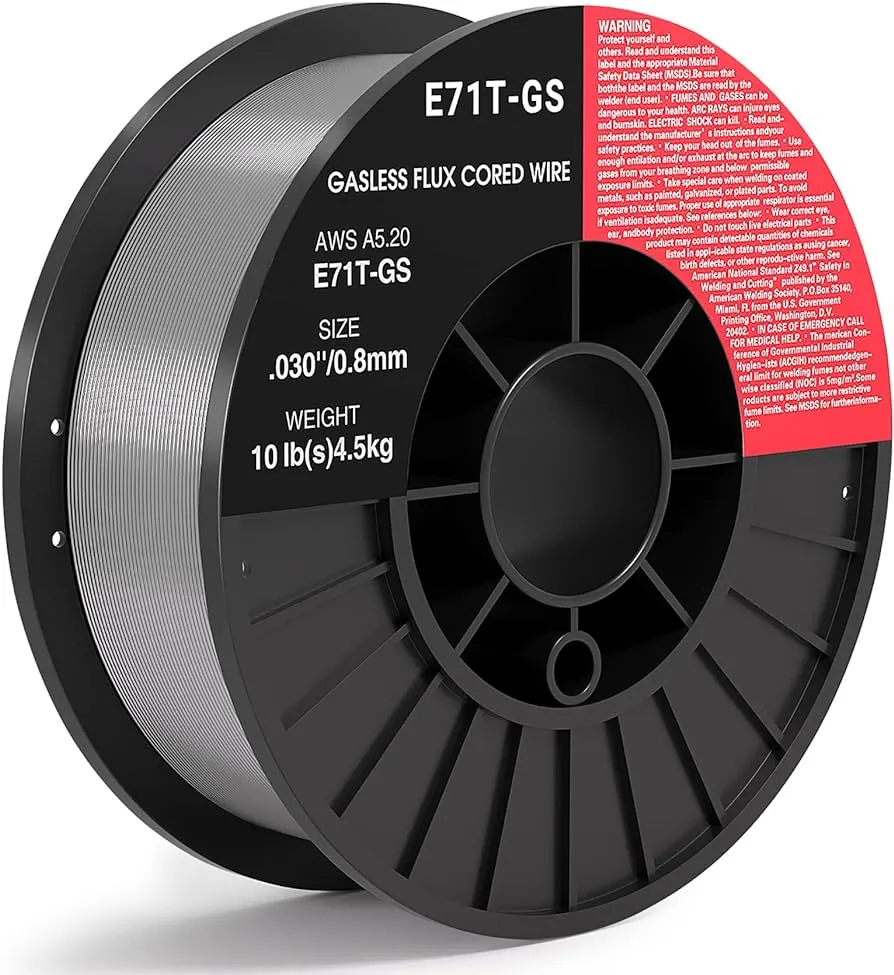
10 lb Mass of 030 Flux Core Wire
A 10 lb spool of 030 flux core wire is a popular choice among welders for several reasons. This larger spool size is suitable for extended welding projects, reducing the need for frequent spool changes and providing a more continuous welding experience. The 10 lb spool is designed to fit most welding machines that accommodate larger spools, ensuring compatibility and convenience.
The 10 lb mass offers several benefits, particularly for welders engaged in medium to large-scale projects. It provides ample wire to complete substantial welding tasks without interruption, which is essential for maintaining workflow and efficiency. Additionally, purchasing wire in larger quantities can be more cost-effective over time, as it often comes at a lower price per pound compared to smaller spools.
Advantages of Using 10 lb Wire
Using a 10 lb spool of 030 flux core wire comes with several advantages:
- Reduced Downtime: A larger spool means fewer spool changes during welding, which reduces downtime and increases productivity. This is particularly beneficial for professional welders working on large projects or in industrial settings.
- Cost Efficiency: Buying in bulk can be more economical. The cost per pound of wire is typically lower when purchased in larger quantities, providing savings over time.
- Consistent Quality: A single spool ensures consistency in the wire used throughout a project. This uniformity helps maintain the quality of welds, as there are no variations in wire composition or performance that might occur when switching between spools.
- Convenience: For welders who frequently engage in extensive welding tasks, having a 10 lb spool on hand is convenient. It ensures that there is always enough wire available, preventing interruptions due to running out of wire.
- Environmental Benefits: Using a larger spool reduces packaging waste compared to using multiple smaller spools. This is an environmentally friendly option, contributing to sustainability efforts in the welding industry.
Application of 030 Flux Core Wire 10 lb
The 10 lb spool of 030 flux core wire is suitable for a variety of applications across different industries. Some common uses include:
- Automotive Repair: The 030 wire is ideal for welding thin to medium-gauge steel, making it perfect for automotive bodywork and repair. The larger spool size ensures that welders can complete extensive repair jobs without needing to frequently replace the wire.
- Construction and Structural Work: In construction and structural applications, the 10 lb spool is beneficial for welding steel beams, frames, and other structural components. The consistent feed and quality of the wire ensure strong and reliable welds, which are crucial in these settings.
- Maintenance and Repair: For maintenance tasks in industrial settings, having a 10 lb spool of 030 flux core wire on hand is practical. It allows for quick and efficient repairs of machinery, equipment, and infrastructure, minimizing downtime and maintaining operational efficiency.
- Fabrication: In metal fabrication shops, where custom parts and structures are created, the 10 lb spool provides the necessary wire for continuous production. It supports the creation of intricate and precise welds, essential for high-quality fabricated products.
- Hobbyist and DIY Projects: Even for hobbyists and DIY enthusiasts, a 10 lb spool can be advantageous. It ensures that there is always enough wire available for various projects, from crafting metal art to building custom furniture.
030 vs 035 Flux Core Welding Wire
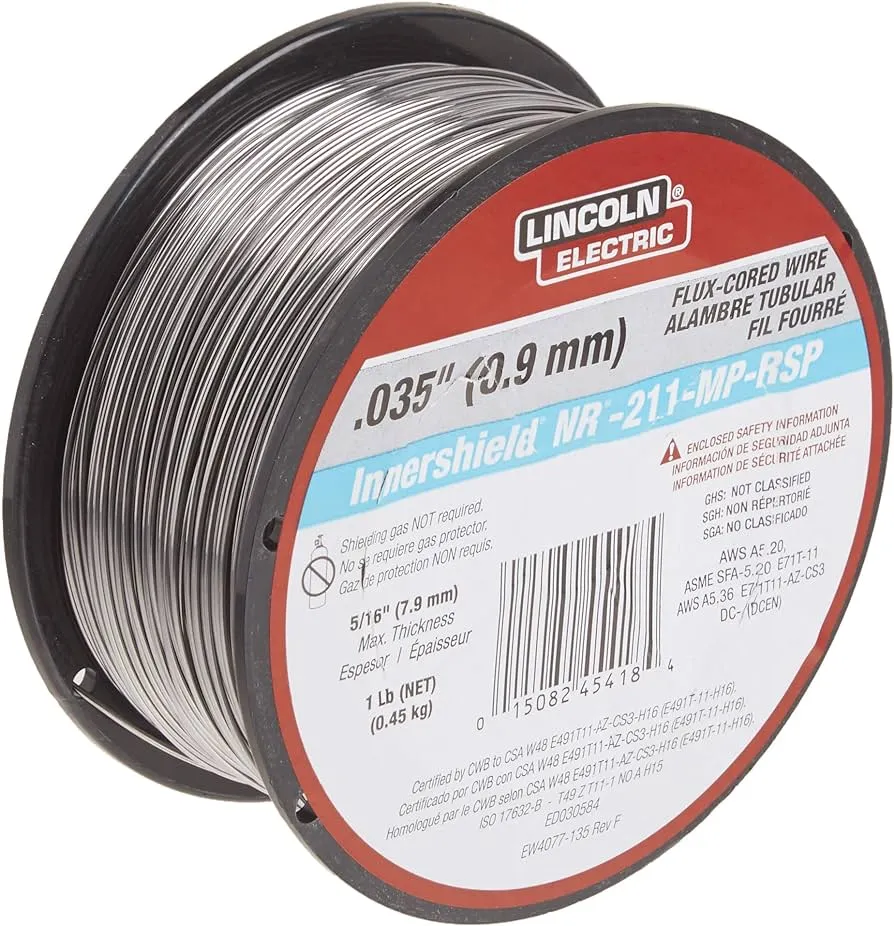
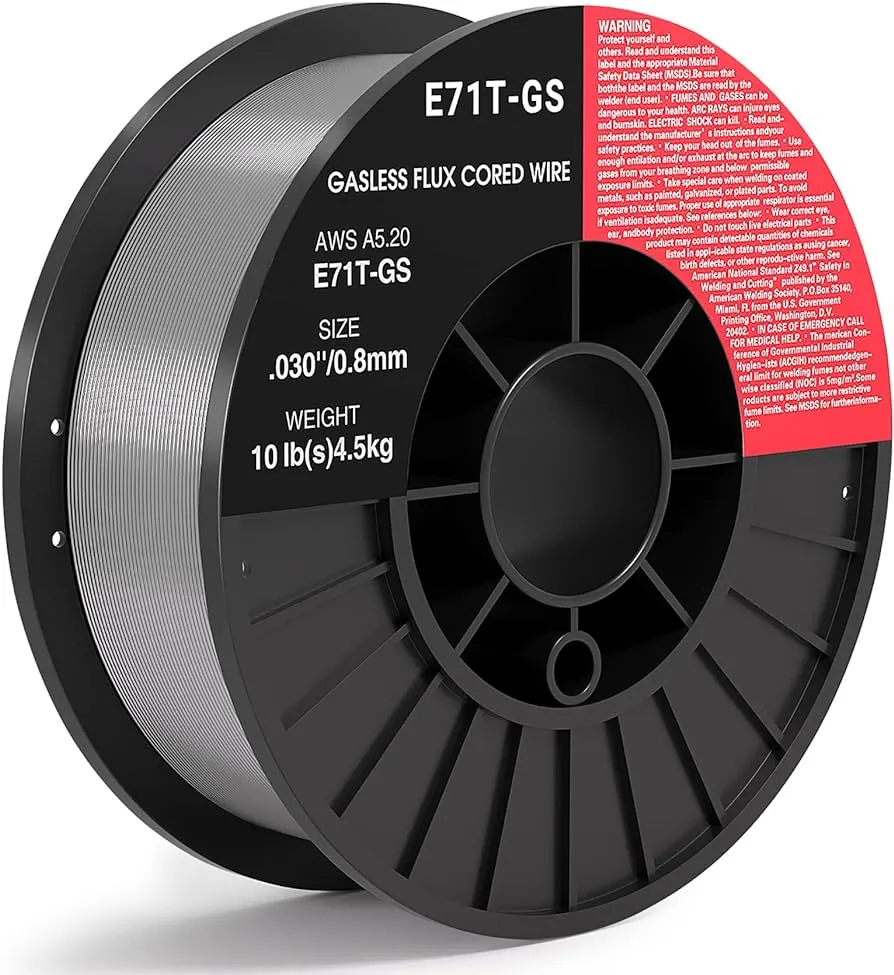
Comparison Between 030 and 035 Flux Core Welding Wire
When choosing between 030 and 035 flux core welding wire, it’s essential to understand the differences in their characteristics, performance, and applications. Both wire sizes have their unique benefits and are suited to different welding tasks.
- Diameter and Thickness: The primary difference between 030 and 035 flux core wire is their diameter. The 030 wire has a diameter of 0.030 inches (0.8 mm), while the 035 wire has a diameter of 0.035 inches (0.9 mm). This difference in thickness affects their performance and suitability for various materials and welding conditions.
- Current and Voltage Requirements: The thicker 035 wire generally requires higher current and voltage settings compared to the 030 wire. This means that welding machines need to be adjusted accordingly to achieve optimal performance with each wire size.
- Penetration and Heat Input: The 035 wire provides deeper penetration due to its larger diameter, making it suitable for welding thicker materials. On the other hand, the 030 wire offers more control and is better suited for thinner materials, reducing the risk of burn-through.
- Feedability and Arc Stability: Both wires are designed to feed smoothly through welding machines, but the 030 wire is often preferred for its ease of use, especially for beginners. The 035 wire, while slightly more challenging to feed, offers a stable arc and consistent performance once properly adjusted.
Characteristics and Applications of Each Type of Wire
030 Flux Core Welding Wire:
- Characteristics:
- Diameter: 0.030 inches (0.8 mm)
- Ideal for welding thin to medium-gauge materials
- Easier to control and provides smooth, consistent welds
- Lower current and voltage requirements
- Applications:
- Automotive repair and bodywork
- Light structural work and maintenance
- Metal fabrication of thin materials
- Hobbyist projects and DIY welding tasks
035 Flux Core Welding Wire:
- Characteristics:
- Diameter: 0.035 inches (0.9 mm)
- Suitable for welding medium to thick-gauge materials
- Provides deeper penetration and stronger welds
- Requires higher current and voltage settings
- Applications:
- Heavy structural work and construction
- Industrial maintenance and repair
- Fabrication of thicker metal components
- Projects requiring strong, deep welds
Choosing the Right One for Your Welding Needs
Selecting the appropriate flux core welding wire depends on several factors, including the material thickness, the specific application, and the welder’s experience level. Here are some considerations to help make the right choice:
- Material Thickness: For thinner materials, the 030 wire is generally the better option due to its ease of control and lower risk of burn-through. For thicker materials, the 035 wire provides the necessary penetration and strength.
- Welding Position: Both wire sizes can be used in various welding positions, but the 030 wire is often preferred for out-of-position welding due to its better control and smoother arc.
- Equipment Compatibility: Ensure that your welding machine can handle the specific wire size you choose. Some machines may have limitations on the wire diameters they can accommodate.
- Experience Level: Beginners may find the 030 wire easier to work with due to its smoother feed and more forgiving nature. Experienced welders can benefit from the deeper penetration and strength provided by the 035 wire for more demanding tasks.
- Project Requirements: Consider the specific requirements of your welding project. If you need strong, deep welds for heavy-duty applications, the 035 wire is the better choice. For more detailed, precise work, the 030 wire offers better control and finish.
Summary
Throughout this article, we have explored the various aspects of 030 flux core welding wire, from its characteristics and applications to a comparison with 035 flux core wire. Here is a concise summary of the key points discussed:
- Flux Core Welding Wire Explanation:
- Flux core welding wire is used in FCAW, an efficient welding process that employs a continuously-fed consumable electrode with a flux core.
- It can be used with or without external shielding gas, depending on the type of flux core wire.
- Characteristics of 030 Flux Core Welding Wire:
- The 030 wire has a diameter of 0.030 inches (0.8 mm), making it suitable for welding thinner materials.
- It is versatile, easy to control, and provides good penetration and smooth bead profiles.
- It performs well in various welding positions and is compatible with most FCAW machines.
- Lincoln 030 Flux Core Wire:
- Lincoln Electric is a reputable manufacturer known for high-quality welding products.
- Lincoln’s 030 flux core wire is made with a carefully formulated core and durable outer shell, ensuring consistent performance and high-quality welds.
- Advantages include consistent performance, high-quality welds, versatility, and ease of use. Disadvantages may include higher cost and limited availability in some regions.
- 030 Flux Core Wire 10 lb:
- A 10 lb spool is ideal for extended welding projects, offering reduced downtime, cost efficiency, consistent quality, convenience, and environmental benefits.
- Common applications include automotive repair, construction, maintenance, fabrication, and hobbyist projects.
- 030 vs 035 Flux Core Welding Wire:
- The 030 wire (0.030 inches) is better suited for thin to medium-gauge materials, offering ease of control and smooth welds with lower current and voltage requirements.
- The 035 wire (0.035 inches) is suitable for medium to thick-gauge materials, providing deeper penetration and stronger welds but requiring higher current and voltage settings.
- The choice between the two depends on material thickness, welding position, equipment compatibility, experience level, and specific project requirements.
In summary, 030 flux core welding wire is a versatile and efficient option for various welding tasks, particularly for thinner materials. Lincoln’s 030 wire stands out for its quality and performance, making it a preferred choice for many welders. The 10 lb spool size offers practical benefits for extended projects, while the comparison with 035 wire helps determine the best choice for specific welding needs. Understanding these aspects ensures that welders can make informed decisions and achieve optimal results in their welding projects.
Leave a Reply