Flux Cored Arc Welding (FCAW) is a semi-automatic or automatic arc welding process that requires a continuously-fed consumable tubular electrode containing a flux and a constant-voltage or, less commonly, a constant-current welding power supply. It is distinguished by its high efficiency, deep penetration, and the superior quality of the weld it produces. FCAW is particularly valued for its versatility, being suitable for outdoor work and on materials that have some degree of surface contamination.
Factors to Consider when Optimizing Flux Cored Welding Technique
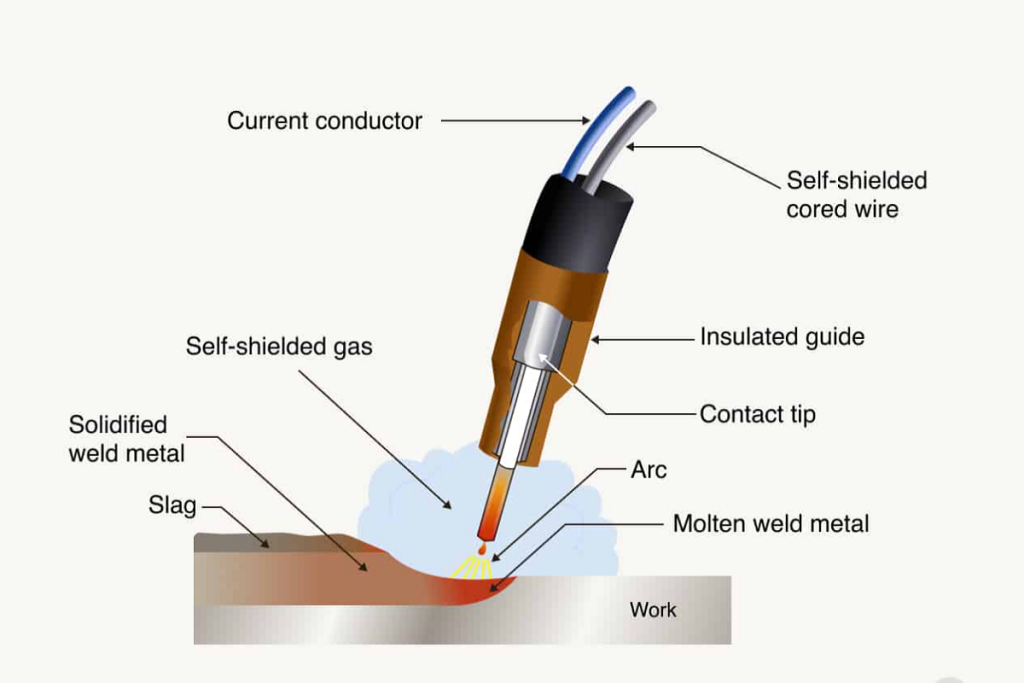
Materials and Types of Welding Wire
Choosing the right material and type of welding wire is crucial for successful flux cored welding. Wires are categorized based on their compatibility with either carbon steel, stainless steel, or specific alloys, and whether they require a shielding gas. The selection depends on the material being welded and the desired properties of the weld.
Setup and Adjustment of Welding Machine and Current Settings
Proper setup of the welding machine and adjustment of current settings are vital for achieving optimal results. This includes selecting the appropriate voltage, wire feed speed, and polarity. A balance between voltage and feed speed must be found to ensure the arc is stable and the weld penetration is adequate.
The primary advantages of flux cored welding include:
- High Welding Speed: FCAW allows for faster welding speeds compared to other methods, such as shielded metal arc welding (SMAW), due to the continuous electrode feed and the high deposition rates.
- Flexibility: It can be used with various metals and alloys, including low-alloy steels, stainless steels, and some nickel-based alloys.
- Reduced Cleanup: The flux in the core of the wire produces slag that covers the weld bead, protecting it during cooling and reducing the amount of spatter and cleanup required.
- Superior Penetration: FCAW provides deep penetration, making it effective for welding thick sections.
Tips and Strategies for Efficient Flux Cored Welding
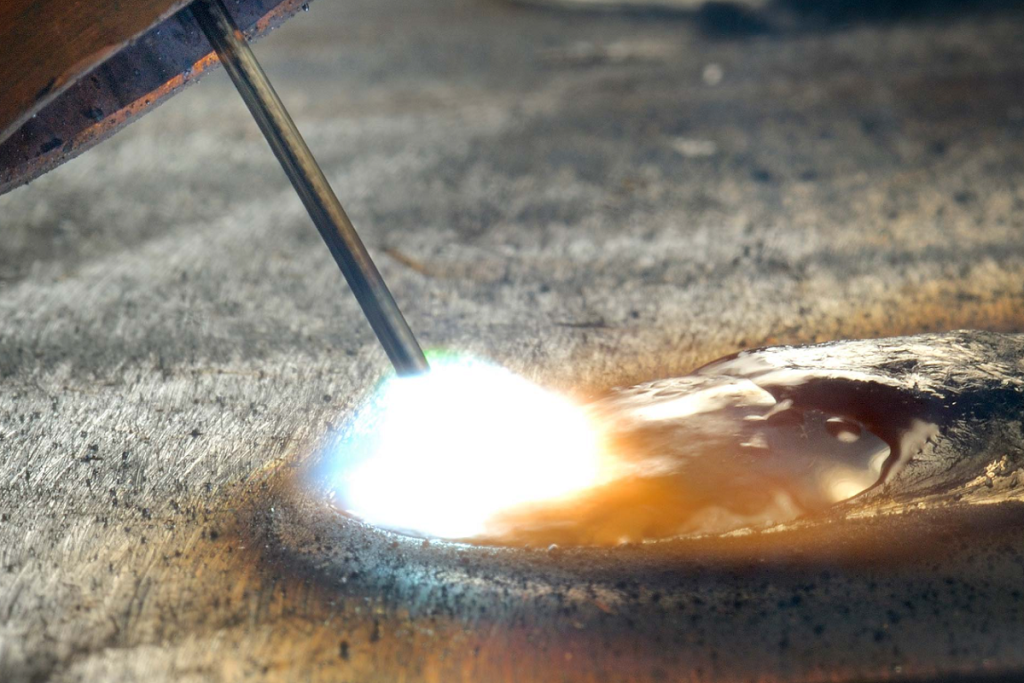
Surface Preparation and Inspection
Cleanliness and preparation of the welding surface are imperative. Any contaminants, such as oil, dirt, or rust, can significantly impact the quality of the weld. Therefore, thorough cleaning and inspection of the weld area before starting are essential.
Utilizing Appropriate Welding Techniques
The technique used during FCAW can greatly affect the outcome. Techniques such as maintaining a consistent travel speed and angle, and choosing the right type of weld pass (stringer versus weave), are important considerations for quality welds.
Monitoring and Adjusting the Welding Process During Work
Continuous monitoring and adjustment of the welding process are necessary to accommodate variations in the welding path or material thickness. This may involve adjusting the wire feed speed or voltage during welding to maintain a stable arc and consistent bead profile.
Maintenance and Storage of Welding Machines and Equipment
Regular maintenance and proper storage of welding machines and equipment are essential to ensure their longevity and reliability. This includes routine checks of the equipment, proper cleaning after use, and storage in a dry, protected environment.
Special Considerations when Working with Specific Applications and Materials
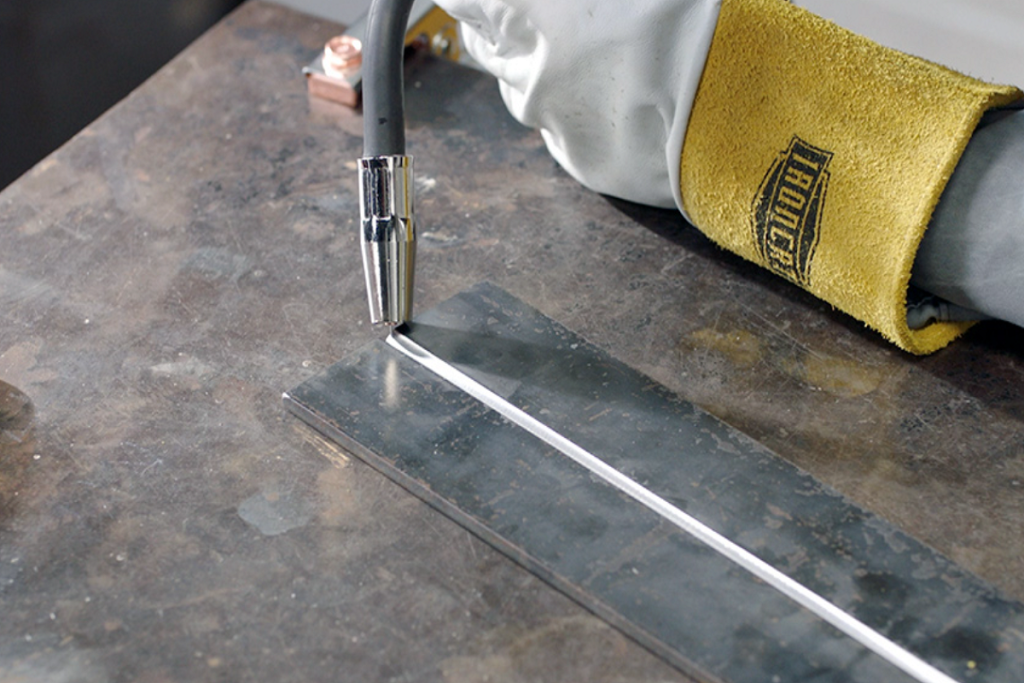
Industrial Applications
Flux cored welding is widely used in various industrial applications, including shipbuilding, heavy equipment repair, and bridge construction. Each application may require specific wire types, shielding gases (if used), and welding parameters to meet the demands of the job.
Welding Different Types of Metals and Alloys
When welding different metals and alloys, special considerations must be taken into account, such as thermal conductivity, melting point, and the potential for cracking. Adjusting the welding technique and parameters accordingly can mitigate these issues.
Conclusion
Flux cored welding is a highly effective and efficient welding process that, when optimized, can produce superior quality welds suitable for a wide range of applications. By understanding and implementing the correct techniques, maintaining equipment, and making informed choices about materials and settings, welders can achieve excellent results. The flexibility and adaptability of FCAW make it a valuable skill in the welding industry, capable of addressing the challenges of modern metal fabrication and repair.
Leave a Reply