The Chicago Electric Flux 125 Welder is an accessible and cost-effective choice for hobbyists and professionals. Its compact design provides portability and simplicity, making it a popular tool in garages and workshops. Proper usage is essential for safety, quality welds, and device longevity. Competency in handling the Flux 125 not only improves outcomes but also boosts user confidence. Despite its initial appearance, this welder is straightforward and versatile, capable of welding various metals like steel, stainless steel, and aluminum for diverse projects, including automotive repairs, DIY home improvements, and artistic creations.
Detailed Review of the Chicago Electric Flux 125 Welder
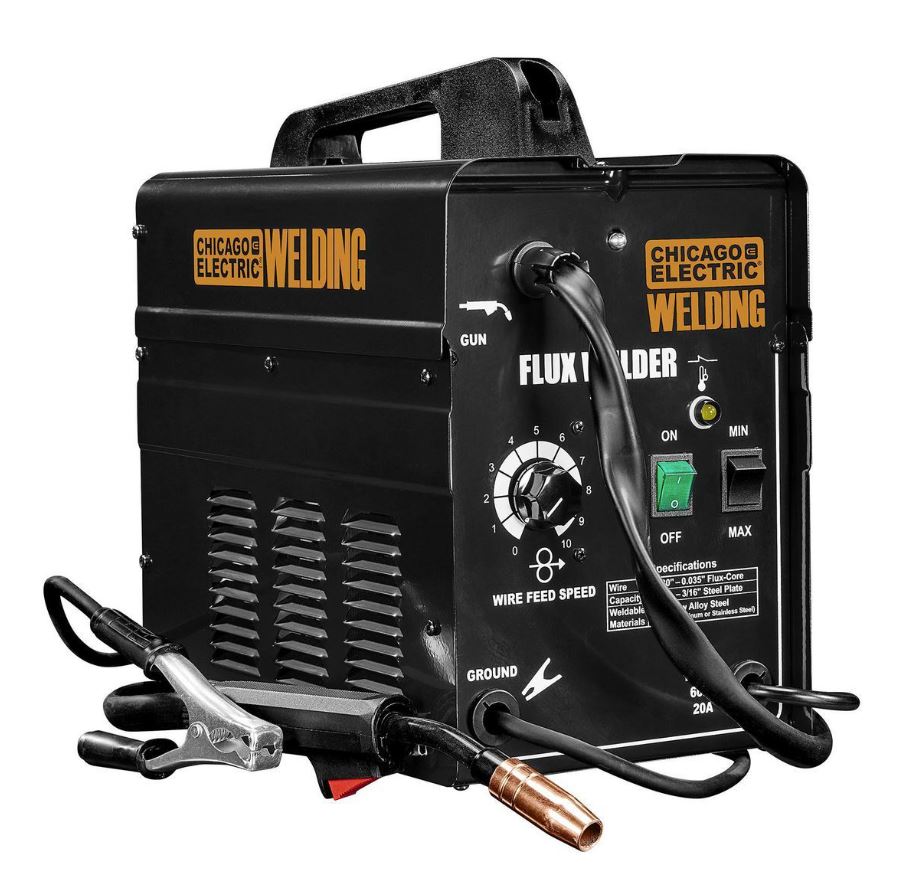
Key Features and Advantages of the Welding Machine
The Chicago Electric Flux 125 Welder boasts a suite of features that make it a standout choice among entry-level welding machines. Its no-nonsense flux core welding eliminates the need for gas, thereby simplifying the setup and welding process—a key advantage for beginners. The machine offers thermal overload protection, which preserves its longevity and ensures user safety during operation. Furthermore, the variable speed wire control enables users to handle different welding tasks with precision.
Its lightweight and compact nature means that the Flux 125 Welder can be easily transported to various job sites or moved around in a crowded workshop, making it a highly versatile tool in any welder’s arsenal.
Drawbacks and Limitations of the Welding Machine
While the Chicago Electric Flux 125 Welder is celebrated for its simplicity and cost-effectiveness, it does come with certain limitations. The most notable is its power output, which is lower than some commercial-grade welders. This limitation means it isn’t suitable for heavy-duty industrial tasks and may struggle with thicker materials.
Additionally, the Flux 125 Welder operates only on AC power, which can be less efficient than DC power in certain welding situations. Users may also find that the included welding gun and ground clamp are not as heavy-duty as those found with more expensive units and may need to be upgraded for more intensive work.
Comparison with Similar Products Available in the Market
When comparing the Chicago Electric Flux 125 Welder to its competitors, such as the Lincoln Electric Handy MIG or the Hobart Handler 140, we must consider various factors. The Lincoln Handy MIG offers the versatility of performing both MIG and flux-cored welding, giving it an advantage for those looking for multi-functionality.
On the other hand, the Hobart Handler 140 offers a higher power output suitable for a broader range of applications, but at a higher price point. Both of these alternatives tend to have better wire-feed systems and come with longer warranties. What stands out for the Flux 125, however, is its unparalleled ease of use for beginners and its affordability, making it an attractive option for casual or entry-level welders.
Benefits of Using the Chicago Electric Flux 125 Welder
The Chicago Electric Flux 125 welder offers beginners a user-friendly and affordable welding method. Its compact design ensures easy and flexible transportation and what more advantages:
Work Efficiency and Precision During the Welding Process
The Chicago Electric Flux 125 Welder contributes significantly to work efficiency, allowing users to begin welding operations almost immediately with minimal setup time. Its intuitive design simplifies the learning curve for beginners, enabling them to focus on mastering the welding process rather than configuring the equipment.
The variable speed wire control is particularly instrumental in achieving precise welds with consistent bead quality, even for those with limited experience. The welder’s effectiveness in handling thinner materials especially highlights its precision capabilities, making it an apt choice for detailed work where finesse is more critical than high power output.
Time and Cost Savings Compared to Other Welding Machines
The Chicago Electric Flux 125 Welder stands out for its cost-efficiency, not only in terms of the initial purchase price but also in the operational and maintenance costs over time. Unlike more complex welding machines that require additional gases and consumables, the Flux 125’s flux-core setup minimizes the need for extra materials, translating into significant long-term savings. The simplified preparation and workflow also save time, which can be particularly beneficial for small businesses and hobbyists who value quick project turnaround and simplicity over industrial-grade capabilities.
Flexibility in Handling a Variety of Welding Projects
Despite its limitations in power and heavy-duty performance, the Flux 125 Welder offers remarkable flexibility for different project types. Its ease of use makes it a go-to machine for quick repairs, small fabrications, and artistic metalwork where precision and the ability to manage thinner materials are paramount. Its compact size enables users to transport it effortlessly and work in constrained spaces where larger, more cumbersome machines would be impractical.
Notably, for educational environments and DIY enthusiasts, the Flux 125 provides a breadth of welding capabilities that encourage experimentation and learning without the intimidation factor of more sophisticated welding units.
Tips for Using the Chicago Electric Flux 125 Welder
Guidelines on Adjusting the Machine for Optimal Results
For welding enthusiasts seeking peak performance from the Chicago Electric Flux 125 Welder, fine-tuning machine settings is crucial. Adjust wire feed speed based on metal thickness, using slower speeds for thin materials and faster speeds for thicker metals. Set wire spool tension to prevent unraveling while ensuring smooth feeding. Gradually increase voltage settings during welding for a stable arc. Regularly inspect and replace the contact tip to maintain optimal electrical conductivity and prevent poor arc quality.
Maintenance and Storage Practices to Enhance Longevity and Performance
Ensuring that the Chicago Electric Flux 125 Welder is well-maintained and stored correctly is essential to extend its life and maintain peak performance. Regular maintenance checks should include inspecting the welding gun and cable for signs of wear or damage. Keeping the gun nozzle clean will ensure a consistent gas flow and improved weld quality.
It’s crucial to store the welder in a dry environment to prevent corrosion and to cover it to protect against dust and debris. Periodically checking for and securely tightening any loose connections can prevent power loss and overheating issues. Lastly, after each use, the welder should be allowed to cool down before storage to alleviate component stress.
Technical Suggestions and Important Considerations During Machine Usage
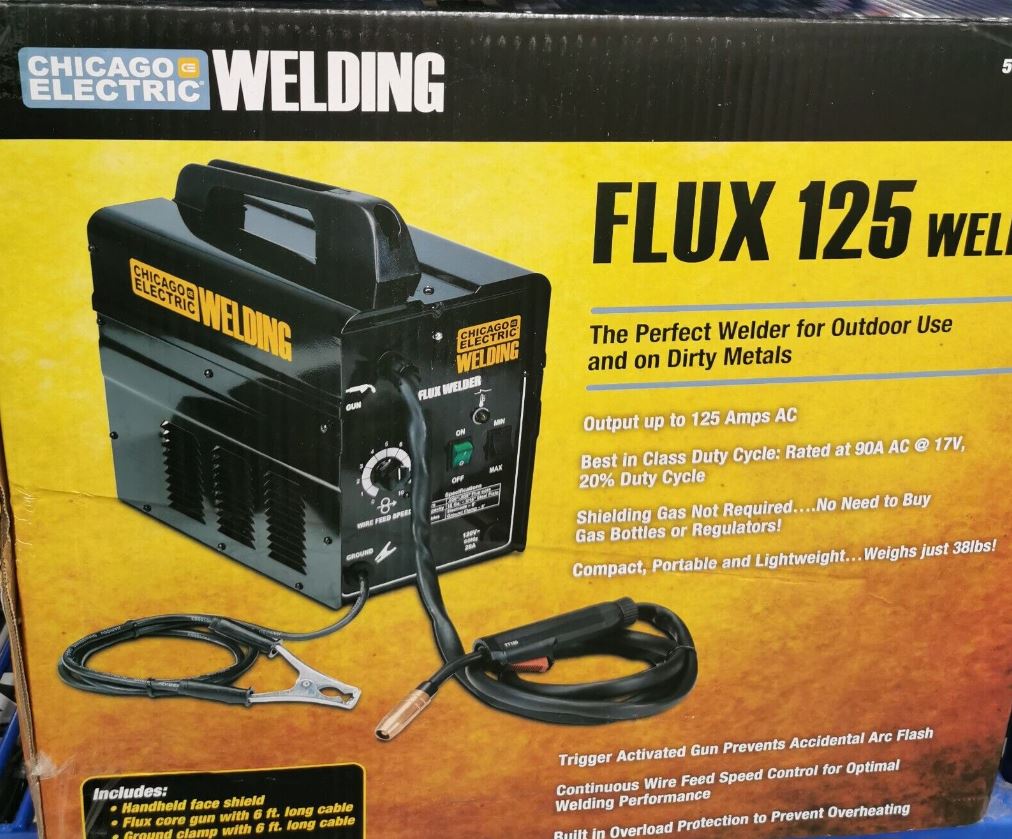
To achieve the best results with the Chicago Electric Flux 125 Welder, users must consider several technical aspects. Firstly, always ensure the work surface is clean and free of rust or paint, which can contaminate the weld. When welding, maintain a consistent angle and travel speed to prevent welding defects. Be mindful of the duty cycle, and avoid exceeding it to preserve the life of the machine.
For optimum performance, using the correct type and diameter of flux-core wire is critical. Attention must also be paid to safety practices, such as using appropriate welding gear to protect against hazardous fumes and ultraviolet radiation. Adherence to these guidelines will aid in delivering high-quality welds and prolonging the reliable function of the welder.
Frequently Asked Questions and Answers
Addressing Common User Queries About the Chicago Electric Flux 125 Welder
- Is the Chicago Electric Flux 125 Welder suitable for professional use?
While the Flux 125 is a robust and efficient tool, it is designed primarily for hobbyists, small repairs, and light fabrication. Its optimal use is in environments where the versatility and ease of movement are priorities over industrial-grade welding capacities.
- Can this welder be used on materials other than steel?
The Chicago Electric Flux 125 Welder is optimized for welding mild steel. It is not recommended for materials like aluminum or stainless steel due to its specific wire feed and power capabilities designed for steel.
- Do I need to use a separate shielding gas with this welder?
No, the Flux 125 Welder uses flux-core wire that produces its own shielding gas when the wire is consumed during the welding process. This eliminates the need for a separate gas supply.
- What is the thinnest metal I can weld with the Flux 125?
The welder performs well on metals as thin as 18-gauge, but care should be taken with wire speed and power settings to prevent burn-through.
- How long can I continuously use the welder before needing a cooldown?
The duty cycle of the Flux 125 Welder is 10% at its maximum setting. This means that at full power, you can weld for 2 minutes before needing to let the machine cool for 8 minutes. Adjusting the settings to lower outputs can extend operative time proportionally.
- What safety equipment do I need when using this welder?
You should always wear eye protection, a welding helmet with the appropriate shade, flame-resistant clothing, gloves, and ear protection. It is also advisable to work in a well-ventilated area or use a fume extraction system to avoid inhaling any harmful fumes.
- Can the wire feed speed be adjusted while welding?
Yes, the Flux 125 has a variable speed dial that can be adjusted on-the-fly to find the optimal feed for your project.
- What types of welding techniques can be performed with the Chicago Electric Flux 125 Welder?
This welder is best suited for mig welding techniques, particularly short-circuit mig. It is not appropriate for TIG or stick welding processes.
Providing Solutions to Common Issues Users May Encounter With the Chicago Electric Flux 125 Welder
Welding with the Chicago Electric Flux 125 Welder can sometimes present challenges that affect the quality and efficiency of your work. Here are common issues and their solutions:
- Excessive Spatter: If you’re experiencing excessive spatter, try reducing the wire feed speed and voltage, ensuring you’re using the correct wire type for the material you’re welding.
- Poor Arc Start: A difficult arc start could be due to a variety of factors such as incorrect voltage settings, a worn contact tip, or a lack of grounding. Verify that your settings are appropriate for the material and that all equipment, including the ground clamp, is in good condition and properly connected.
- Wire Feeding Problems: If the wire is not feeding smoothly, check for blockages or kinks in the liner, ensure the spool hub tension is correctly adjusted, and that the feed rollers match the wire diameter and are not worn.
- Unstable Arc: An unstable arc may result from dirty or rusty metal, incorrect settings, or insufficient contact tip-to-work distance. Clean the workpiece thoroughly and adjust settings and technique as required.
- Burn-Through: When dealing with thin materials, burn-through occurs if the heat input is too high. Utilize lower voltage and wire feed settings, and weld in short bursts to minimize heat.
- Inconsistent Welding Results: Consistency issues often stem from varying travel speeds and angles. Practice maintaining a steady travel speed and an even angle relative to the workpiece.
By addressing these common issues with the prescribed solutions, users can most often solve their welding problems quickly and efficiently.
Conclusion
In conclusion, the Chicago Electric Flux 125 Welder is a reliable and user-friendly tool for light to medium-duty welding tasks. Its portability, gas-free operation, and versatility make it ideal for hobbyists and small-scale fabricators working with mild steel. To maximize performance, users should follow provided technical suggestions, ensuring consistent, high-quality welds. With cost efficiency and comprehensive support, the Flux 125 is a recommended choice for those seeking a balanced blend of performance and affordability in welding.
Leave a Reply