Welding stainless steel demands precision and skill due to its unique properties, such as corrosion resistance, durability, and aesthetic appeal. Widely used in various industries, including construction, automotive, and culinary, stainless steel requires specialized welding techniques. Overcoming challenges like high thermal conductivity and potential corrosion risk, proper welding is essential for operational efficiency and longevity in these industries.
Some knowledge about stainless steel you need to keep in mind
Differentiating Common Types of Stainless Steel
Stainless steel comes in various types, each with distinct properties and applications. The most common include austenitic, ferritic, and martensitic stainless steel. Austenitic stainless steel, known for its superior corrosion resistance and weldability, is often employed in kitchen appliances and chemical processing equipment. Ferritic stainless steel, characterized by its high chromium and low carbon content, is usually used in automotive applications. Lastly, martensitic stainless steel, which balances high strength and moderate corrosion resistance, is commonly found in cutlery and engineering applications.
Basic Characteristics of Stainless Steel Affecting the Welding Process
Stainless steel’s unique characteristics significantly impact the welding process. Its high thermal conductivity means that it absorbs and disperses heat quickly, necessitating careful control of welding temperatures. Moreover, its strong resistance to corrosion can be compromised if the welding process is not performed correctly, leading to a phenomenon known as weld decay. This potential risk underlines the importance of a meticulous, skilled approach to welding stainless steel.
Preparation and safety when welding stainless steel
Checking and Preparing Materials
Before beginning any welding project, it is crucial to ensure that all materials are thoroughly checked and prepared. This includes inspecting the stainless steel for any surface impurities such as oils, grease, or rust that may hinder the welding process. The alloy should be cleaned with an appropriate solvent and then wiped dry to prevent contamination. Additionally, affirming the compatibility of filler materials with the base metal is essential to prevent any weld discrepancies and ensure structural integrity.
Safety Measures When Working with Electricity, Gas, and Materials
When welding stainless steel, safety must be at the forefront. Workers should be equipped with personal protective equipment (PPE) including gloves, welding helmets with appropriate filter shades, and protective clothing to shield against sparks and hot metal. Adequate ventilation is necessary to prevent the inhalation of toxic fumes. Precautions against electric shock are critical when working with electric welding equipment; therefore, maintaining dry work areas and using insulated tools and gloves are imperative. When utilizing gas welding techniques, proper storage and handling of gas cylinders are essential to prevent leaks and explosions. Following stringent safety protocols can minimize the risk of accidents and health hazards, ensuring a safe working environment.
How to set up welding machines and tools
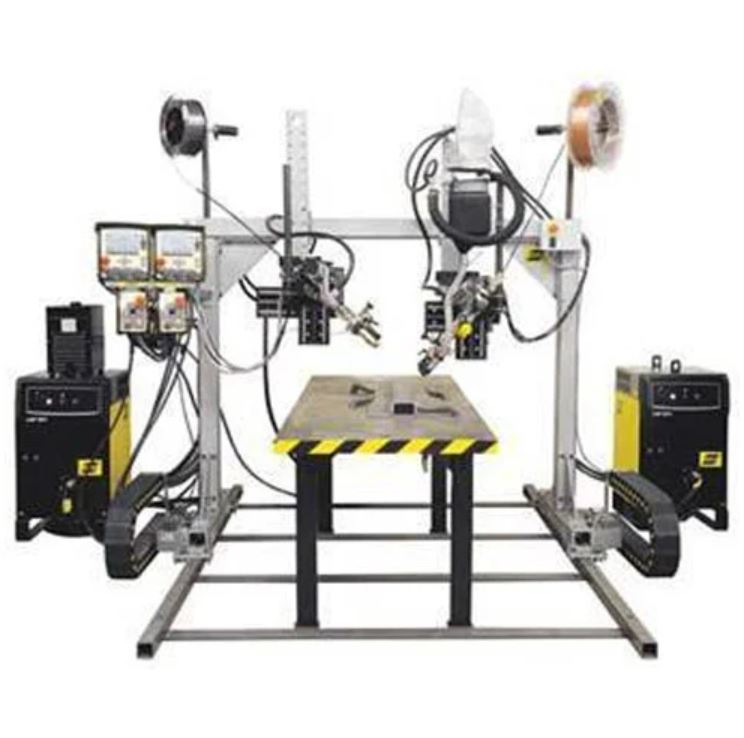
Selecting the right equipment and configuring it to the proper settings is a fundamental step in mastering the art of welding stainless steel. Welders must consider the specific type of stainless steel, the thickness of the material, and the final application to choose the most appropriate welding machine—be it TIG (Tungsten Inert Gas), MIG (Metal Inert Gas), or stick welding equipment. Each machine offers different benefits; for example, TIG welding allows for greater control and precision necessary for thinner gauges of stainless steel, while MIG welding can be advantageous for its speed in heavier industrial applications. Precise calibration of the machine to the correct amperage and voltage is vital to address stainless steel’s rapid heating and cooling properties.
Choosing the Right Welding Machine and Proper Settings
Identifying the correct machine and settings for stainless steel welding is vital for creating strong, durable welds. TIG welding machines are often preferred for their precision, especially when dealing with thinner stainless steel. The settings must be adjusted based on the type and thickness of the stainless steel, focusing on maintaining a stable arc and preventing burn-through. Pulse welding settings can help manage heat input on delicate or complex joints.
Using the Correct Electrodes and Gas
The selection of suitable electrodes and shielding gas plays a crucial role in achieving optimum weld quality. For TIG welding, using a high-quality tungsten electrode is essential, often with a thoriated, ceriated, or lanthanated type, depending on the application. The choice of gas is equally important; pure argon or a mix of argon and hydrogen is typically used for TIG welding of stainless steel, providing an inert environment to prevent oxidation and achieve clean, bright welds. When it comes to MIG welding, the use of an appropriate gas mixture, such as a tri-mix (helium, argon, CO2), is recommended to ensure deep weld penetration and good arc stability.
How to use stainless steel welding techniques
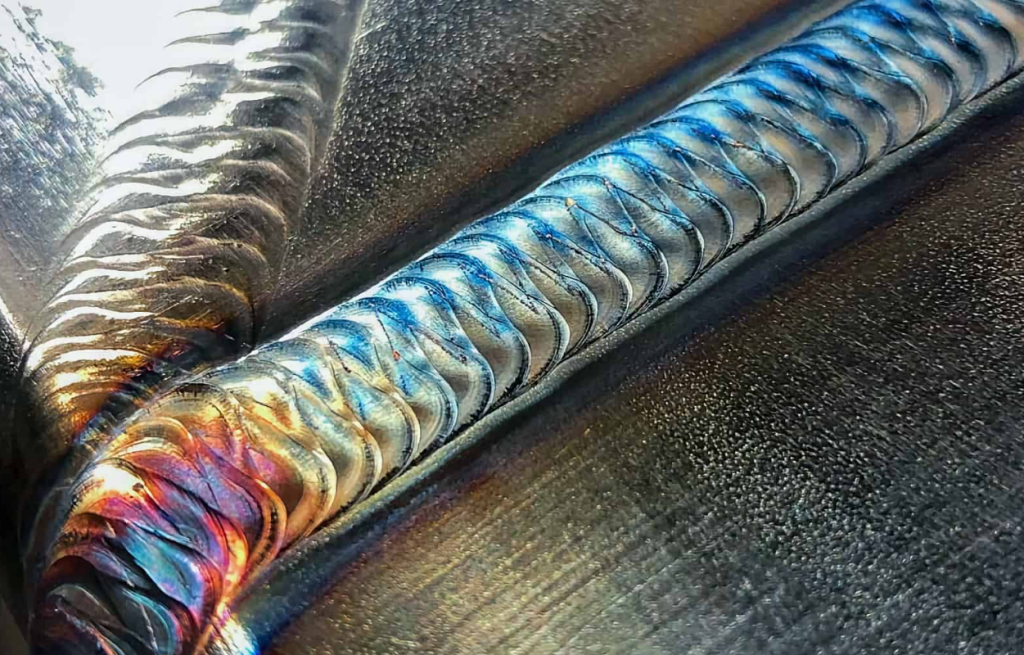
Proper welding techniques are essential to create not only aesthetically pleasing but also structurally sound and reliable welds in stainless steel applications. Mastery of these techniques reduces the risk of common welding defects such as warping, oxidation, and weld decay.
Welding From Starting Points to Seamless Connections
The initiation of a weld, known as the starting point, sets the stage for the entire welding process. Precision at this phase is critical. Welders should begin by striking an arc that is just powerful enough to create a pool of molten metal, then proceed by adding filler material and advancing the weld at a measured pace. The aim is to maintain a consistent weld pool size and temperature, ensuring a seamless transition between welded sections.
Employing TIG and MIG Welding Techniques
Two of the most popular techniques for welding stainless steel are TIG and MIG welding. TIG welding is renowned for its precision and control, which is necessary for welding complex shapes or thin materials. It requires the welder to maintain a short arc length and to control the heat input to protect the material’s integrity. MIG welding, on the other hand, is preferred for its efficiency and ease of use, particularly on thicker materials. This method involves continuously feeding a consumable wire electrode and a shielding gas through the welding gun, which can be more forgiving and quicker than TIG welding. In both cases, the welder must be adept at adjusting techniques and equipment settings in response to the material’s behavior during the welding process.
Temperature and Distortion Management
Effectively managing the temperature and addressing potential distortion are critical when welding stainless steel, which can significantly impact the quality and precision of the final product.
Adjusting Welding Temperature to Prevent Unwanted Distortion
When welding stainless steel, careful control of the welding temperature is crucial to prevent unwanted distortion, which can occur due to the metal’s expansion and contraction. To minimize these effects, welders should use a lower heat input and implement an intermittent welding technique, or ‘stitch welding,’ allowing the material to cool between weld passes. Pre-heating and post-weld heat treatments may also be used, depending on the composition and thickness of the stainless steel, to equalize temperatures throughout the welding process and reduce stress in the material.
Controlling Temperature to Preserve the Mechanical Properties of Stainless Steel
The mechanical properties of stainless steel, such as corrosion resistance and strength, can be compromised by excessive heat during welding. To preserve these properties, it is important to manage the heat input by using proper welding techniques and selecting the correct parameters on the welding equipment. Keeping the interpass temperature below a certain threshold—often recommended by the steel manufacturer or by welding codes—helps maintain the material’s mechanical integrity. Additionally, controlled cooling practices, such as using cooling jigs or forced air, can aid in bringing the welded stainless steel down to an appropriate temperature at a rate that prevents the formation of undesirable metallurgical phases.
How should the machine be maintained and serviced?
The reliability and durability of welded stainless steel structures depend heavily on the quality of the welding work. Failure to adhere to proper welding procedures can result in compromised structural integrity and shortened lifespan of the products. Furthermore, preventive maintenance is key to preserving the aesthetic and functional qualities of stainless steel welds over time.
Evaluating the Quality of Welded Structures
Post-weld evaluation is an integral part of ensuring the quality and safety of stainless steel structures. Inspections should be performed to check for any signs of corrosion, cracks, or other weld defects. Non-destructive testing methods, such as ultrasonic, radiographic, or dye penetrant inspection, can be utilized to detect subsurface or surface imperfections that are not visible to the naked eye. Regular evaluations help in identifying issues early on, potentially avoiding costly repairs or catastrophic failures.
Suggestions for Maintenance and Preservation of Stainless Steel Welding Products
Regular maintenance is essential to prolong the life of stainless steel welding products and preserve their corrosion resistance. This maintenance may include routine cleaning with appropriate agents to remove contaminants, periodic inspections for signs of wear, and immediate repair of small defects before they escalate. It is also advisable to keep the welded products in environments that minimize corrosive exposure. For instance, in chloride-rich environments, regular rinsing with clean water can mitigate the risk of corrosion. Protective coatings may also be applied for additional preservation, especially in aggressive service conditions.
Best advice when using stainless steel welding machine
To ensure weld quality and enhance the overall effectiveness of welding stainless steel, continuous learning and adaptation to new methods are indispensable.
Staying updated with technological advancements
Technological advancements in welding are constant, bringing forth new equipment and techniques that can significantly improve efficiency and results. Welders and fabricators should stay informed about the latest innovations in welding processes, materials, and equipment. Attending industry conferences, participating in webinars, and subscribing to trade publications are just a few ways to stay on the cutting edge of welding technology. Embracing these advancements can lead to better quality welds, increased productivity, and a competitive edge in the market.
Learning from experts in the field
The collective knowledge and experience of seasoned welding professionals are invaluable resources for both novice and experienced welders. Learning from experts can come in many forms, from formal apprenticeships and mentorship programs to informal networking opportunities and industry forums. Engaging with a community of welders allows for the sharing of tips, solutions to common problems, and strategies for handling complex welding projects. Striving for continuous improvement through expertise exchange not only broadens one’s skill set but also reinforces best practices within the welding community.
Conclusion
Effective welding of stainless steel demands precise techniques, temperature control, and material selection. Preventing distortion and maintaining material properties are crucial. Ongoing education is essential in the evolving welding industry to ensure quality, safety, and competitiveness. Regular inspections and knowledge-sharing within the welding community contribute to the advancement of the field.
Leave a Reply