Overview of Tungsten Welding
Tungsten welding, often referred to as Tungsten Inert Gas (TIG) welding, is a precise and versatile welding technique that uses a tungsten electrode to create an arc for welding. This method is widely recognized for its ability to produce high-quality welds with minimal spatter, making it ideal for applications requiring clean and accurate welds.
Tungsten, known for its high melting point and excellent conductivity, is used in this process because it maintains its shape even at high temperatures. This property is crucial for maintaining a stable arc and ensuring the quality of the weld.
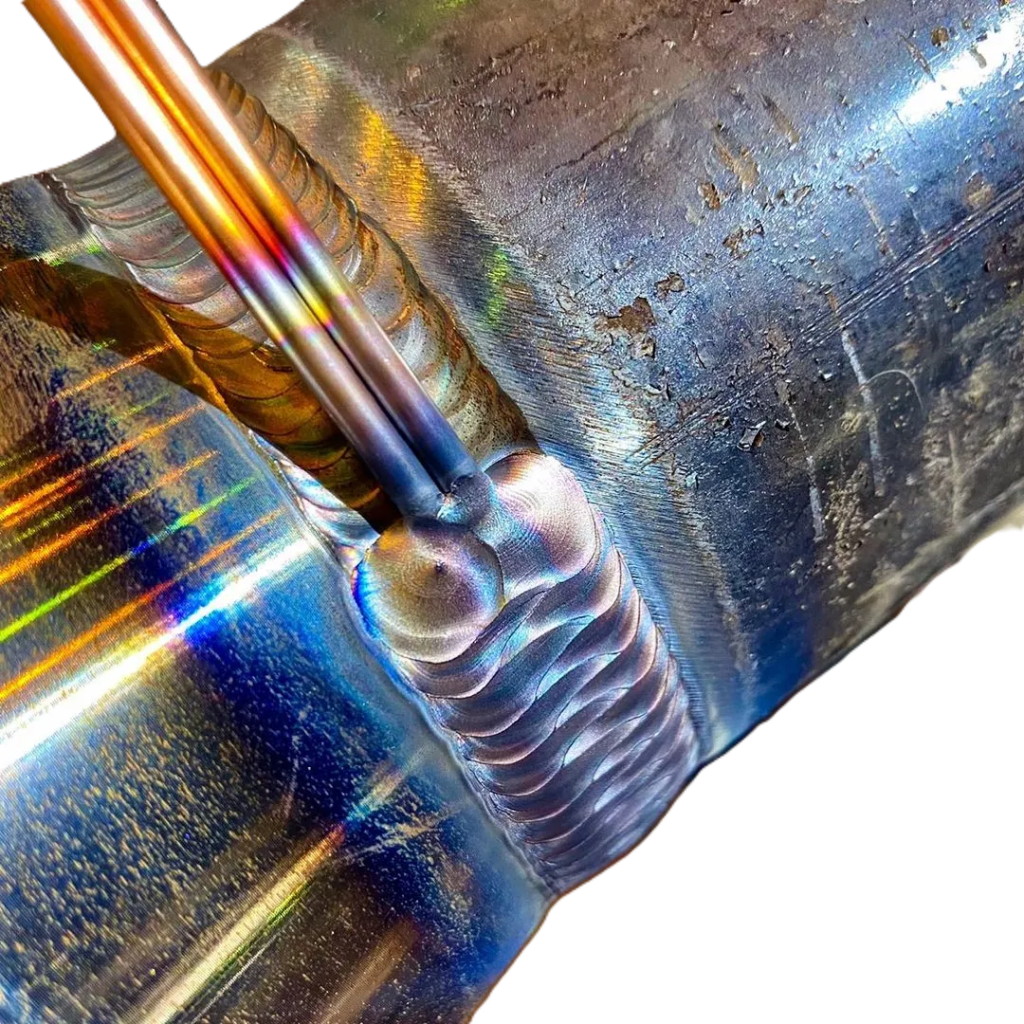
Importance and Applications of Tungsten Welding
Tungsten welding is particularly valuable in industries where precision and strength are essential. It is commonly used in the aerospace, automotive, and manufacturing sectors. Its ability to weld thin materials and its compatibility with a variety of metals, including stainless steel, aluminum, and magnesium, make it a preferred choice for many professionals.
Basic Steps for Tungsten Welding
Preparing Materials and Equipment
- Choosing the Right Tungsten Electrode: Selecting the appropriate tungsten electrode is crucial for achieving optimal results. Tungsten electrodes come in various types, such as pure tungsten, thoriated, and cerium, each suited for different applications. For most general-purpose welding, thoriated tungsten is commonly used due to its excellent arc stability and longevity.
- Setting Up the TIG Welder: Properly setting up your TIG welder involves configuring the machine according to the requirements of your welding project. Ensure that the welder is compatible with the type of tungsten electrode you are using and adjust the settings for current and polarity based on the material and thickness you’re working with.
- Preparing the Work Surface: Clean the work surface thoroughly to remove any contaminants such as rust, paint, or grease. A clean surface ensures better weld quality and reduces the risk of defects. Use a wire brush or chemical cleaner to prepare the surface before starting the welding process.
Setting Up the TIG Welder
- Adjusting the Current Intensity: Set the current intensity on your TIG welder according to the thickness of the material being welded. For thin materials, a lower current setting is typically used, while thicker materials may require higher current levels. Refer to the manufacturer’s guidelines for specific recommendations based on the material and electrode size.
- Choosing the Shielding Gas: Select the appropriate shielding gas for your welding project. Argon is the most commonly used gas for TIG welding due to its inert properties, which prevent contamination of the weld. For certain materials, a mixture of argon and helium may be used to enhance heat input and improve arc stability.
Tungsten Welding Process
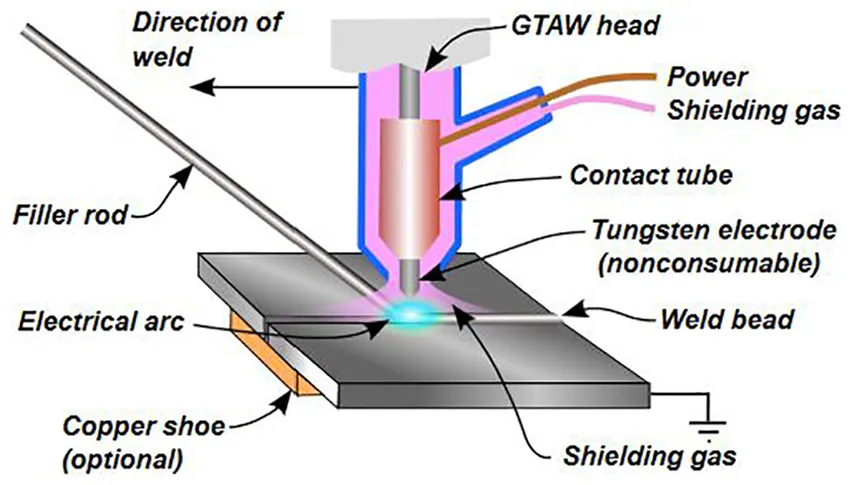
Starting the Welding Process
- Igniting the Arc: Begin the welding process by initiating the arc between the tungsten electrode and the workpiece. This can be done using a high-frequency start or a scratch start, depending on your TIG welder. High-frequency starts are preferred for their ability to start the arc without contacting the tungsten electrode with the workpiece, reducing contamination.
- Establishing the Arc Stability: Once the arc is ignited, adjust the arc length to maintain stability. A stable arc is essential for consistent weld quality and for preventing issues such as arc wander or sputtering. Keep the arc length short to ensure good control and a clean weld.
Welding the Joint
- Controlling the Welding Speed: Move the torch at a consistent speed along the weld joint. The welding speed should be adjusted according to the material thickness and the weld size. Moving too quickly can result in weak welds, while moving too slowly may cause excessive heat input and distortion.
- Managing Temperature and Weld Pool: Monitor the weld pool and temperature throughout the welding process. The temperature should be kept within the optimal range to ensure proper fusion of the materials. Use the foot pedal or torch control to adjust the heat as needed and maintain a stable weld pool.
Completing the Welding Process
- Ending the Arc: Once you have completed the weld, carefully extinguish the arc by lifting the torch away from the workpiece. Allow the weld to cool gradually to prevent cracking or distortion. Avoid moving the workpiece until it has cooled sufficiently.
- Cooling the Weld: Let the weld cool naturally or use a cooling fan if necessary. Rapid cooling can lead to defects such as thermal stress or warping. Ensure the weld area remains undisturbed during the cooling phase to maintain weld integrity.
Safety Considerations for Tungsten Welding
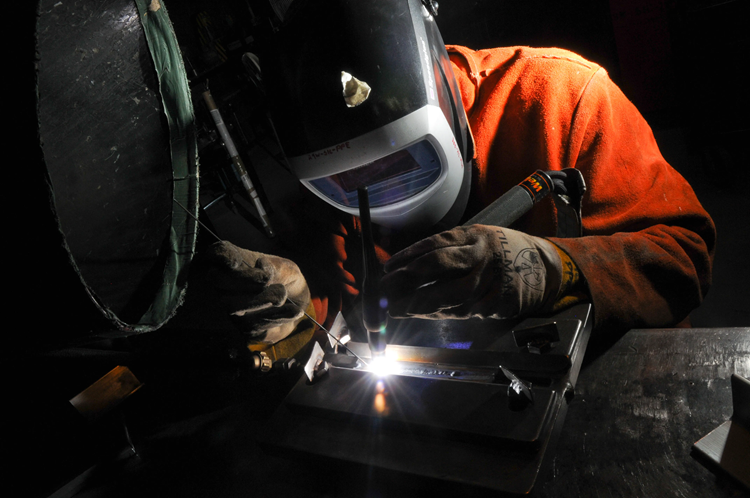
Using Personal Protective Equipment (PPE)
- Welding Helmet: Always wear a welding helmet with the appropriate shade to protect your eyes from the intense light and UV radiation produced during the welding process. A helmet with an auto-darkening feature can provide added convenience and protection.
- Protective Clothing: Wear flame-resistant clothing, including gloves and a jacket or apron, to shield your skin from heat, sparks, and spatter. Ensure that your clothing is made of materials designed to withstand high temperatures and provide adequate coverage.
Inspecting and Maintaining Equipment
- Checking the Welding Machine: Regularly inspect your TIG welder for any signs of wear or damage. Check cables, connectors, and the welding torch to ensure they are in good working condition. Address any issues immediately to prevent malfunctions during welding.
- Ensuring Electrical Safety: Ensure that all electrical connections are secure and that there are no exposed wires. Use a grounding clamp to prevent electrical shock and maintain a safe working environment. Keep the work area dry and free from water or other conductive materials.
Handling and Storing Shielding Gas
- Proper Gas Storage: Store shielding gas cylinders in an upright position and secure them to prevent tipping. Keep cylinders in a well-ventilated area away from sources of heat or flame. Follow the manufacturer’s instructions for safe handling and storage.
- Preventing Gas Leaks: Check for leaks in the gas lines and connections before starting the welding process. Use soapy water to detect any leaks and address them immediately. Proper maintenance of gas equipment ensures safe and effective welding operations.
Common Welding Issues and Solutions
Cracking in the Weld
- Causes: Cracking in the weld can be caused by several factors, including excessive heat, rapid cooling, or improper joint preparation. Cracks often appear as the weld cools and solidifies if the thermal stresses are not properly managed.
- Solutions:
- Control Heat Input: Adjust the welding parameters to avoid overheating the material. Ensure the heat is evenly distributed and avoid prolonged exposure to high temperatures.
- Slow Cooling: Allow the weld to cool gradually to minimize thermal stresses. Use cooling fans sparingly and avoid rapid cooling methods.
- Proper Preparation: Ensure the joint is clean and properly aligned before welding to reduce the risk of cracks forming.
Uneven Weld Bead
- Causes: An uneven weld bead can result from inconsistent welding speed, improper arc length, or fluctuations in heat input. This issue can affect the overall strength and appearance of the weld.
- Solutions:
- Maintain Consistent Speed: Move the torch at a steady pace and avoid varying your speed during welding. Practice to develop a smooth, consistent movement.
- Adjust Arc Length: Keep the arc length short and stable to ensure a uniform weld bead. Adjust the torch position as needed to maintain consistency.
- Monitor Heat Input: Regularly check and adjust the heat settings to match the requirements of the material being welded.
Oxidation of the Weld
- Causes: Oxidation occurs when the weld is exposed to air or improper shielding gas coverage. This can result in a discolored and weakened weld.
- Solutions:
- Ensure Proper Shielding: Use the correct type and flow rate of shielding gas to protect the weld from contamination. Check gas connections and flow regularly.
- Avoid Contamination: Keep the welding area free from drafts and contaminants that could affect the shielding gas. Ensure the work surface is clean and free of oils or rust.
- Use High-Quality Gas: Ensure that the shielding gas is of high quality and suitable for the welding material and process.
Conclusion
Summary of Tungsten Welding Techniques
Tungsten welding, or TIG welding, is a highly versatile and precise method used for creating high-quality welds with minimal spatter. By carefully preparing materials and equipment, following the correct welding procedures, and adhering to safety protocols, welders can achieve strong, clean welds suitable for a variety of applications. Key steps include proper setup of the TIG welder, maintaining a stable arc, and ensuring adequate shielding.
Benefits of Mastering Tungsten Welding
Mastering tungsten welding provides several advantages. It allows for greater control over the welding process, producing welds that are both aesthetically pleasing and structurally sound. The technique is particularly useful for welding thin materials and achieving high precision, making it a valuable skill in industries such as aerospace, automotive, and manufacturing. Additionally, proficiency in tungsten welding can enhance a welder’s ability to work with a wide range of metals and alloys, expanding their versatility and job opportunities.
Encouragement for Practice and Safety
To achieve proficiency in tungsten welding, continuous practice and adherence to safety guidelines are essential. Regularly review and refine your skills, stay updated with best practices, and always prioritize safety in the workplace. By doing so, you’ll ensure not only the quality of your welds but also your own well-being and that of your colleagues.
Leave a Reply