Introduction
Welding is an essential skill in many industries, from construction to automotive repair. One of the most popular types of welding is argon welding, which uses argon gas to create clean and precise welds. This guide aims to help beginners understand the importance of argon welding tanks, how to choose the right tank, and the basic steps to get started.
Argon welding, or Gas Tungsten Arc Welding (GTAW), is favored for its ability to produce high-quality, precise welds. Argon provides a protective shield, ensuring a cleaner, more controlled welding environment, making it valuable in industries requiring exacting standards. Argon welding tanks store argon gas under high pressure and deliver it through the welding torch to the weld area. The steady flow of argon gas displaces surrounding air, preventing contaminants like oxygen and nitrogen from reacting with the molten weld pool. This ensures a stronger, defect-free weld.
This guide will cover understanding argon welding tanks, choosing the right tank, using argon welding tanks safely and effectively, and common applications and benefits.
What is an Argon Welding Tank?
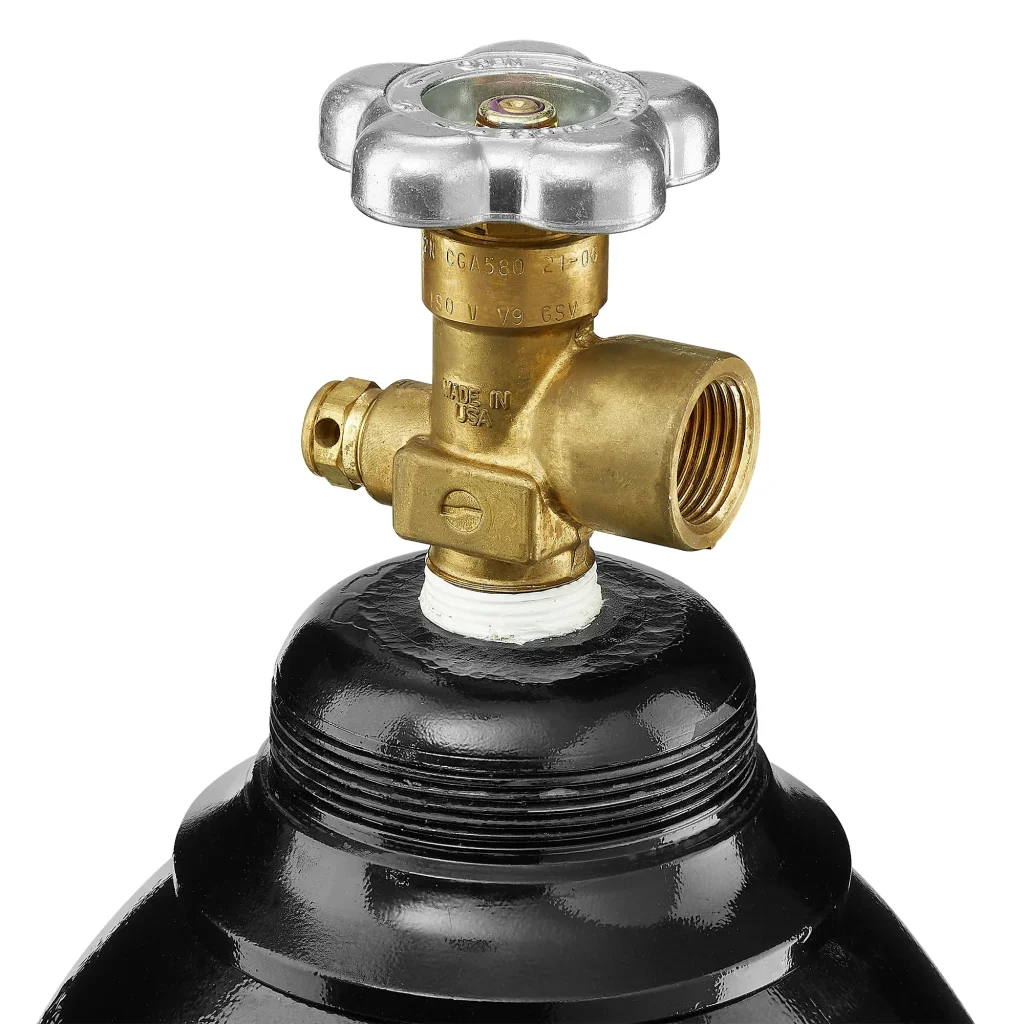
An argon welding tank is a cylinder that stores argon gas under high pressure, typically up to 3000 psi (pounds per square inch). Argon is an inert gas, meaning it does not react with other elements at room temperature. This inertness makes it ideal for welding, as it creates a protective atmosphere around the weld, preventing oxidation and contamination. During the welding process, the argon gas is released from the tank through a regulator, which controls the flow rate. The gas flows through a hose to the welding torch, where it is directed onto the weld area. This continuous flow of argon gas shields the weld from the air, ensuring a clean and strong bond.
Argon is primarily used in two types of welding processes: TIG (Tungsten Inert Gas) Welding and MIG (Metal Inert Gas) Welding. TIG welding uses a non-consumable tungsten electrode to produce the weld. Argon gas is used to protect the weld area, resulting in a clean and precise weld. This method is often used for welding thin materials and non-ferrous metals like aluminum, magnesium, and copper alloys. MIG welding uses a continuous wire feed as an electrode and filler material. Argon, sometimes mixed with other gases like carbon dioxide, shields the weld area. This method is suitable for welding thicker materials and is widely used in industrial applications. Argon provides cleaner welds, better control, and versatility, making it suitable for various materials and different welding projects.
Types of Argon Welding Tanks
Argon welding tanks come in various sizes and capacities to suit different needs. Small tanks (20-40 cubic feet) are portable and ideal for hobbyists or small-scale projects. They are easy to transport and store but require frequent refilling for continuous use. Medium tanks (80-125 cubic feet) strike a balance between portability and capacity. They are suitable for small to medium-sized projects and offer a longer welding time before needing a refill. Large tanks (250-330 cubic feet) are best for professional welders and large-scale projects. While they are less portable due to their size, they provide extended welding time and reduce the frequency of refills.
Argon tanks are typically made from high-strength materials to withstand the pressure of the gas they contain. Most argon tanks are made from steel due to its durability and ability to handle high pressure. Steel tanks are heavy but robust and long-lasting, making them a popular choice for industrial use. Aluminum tanks are lighter than steel tanks, making them easier to transport. However, they are generally more expensive and less durable than steel tanks. Aluminum tanks are often used by welders who need to move their equipment frequently.
When choosing an argon welding tank, it is essential to ensure it meets industry standards and regulations. In the United States, argon tanks must comply with the Department of Transportation (DOT) regulations, which specify the construction, testing, and labeling requirements for compressed gas cylinders. Look for tanks that are DOT-approved to ensure safety and compliance. Internationally, similar standards are set by bodies like the Transport Canada (TC) and the European Agreement concerning the International Carriage of Dangerous Goods by Road (ADR). Always check for relevant certifications and markings on the tank to verify its compliance with local regulations.
Selecting the right size of argon welding tank depends on your specific needs and usage patterns. For occasional home projects, a small tank might suffice. For regular use in a workshop, a medium tank offers a good balance. For professional or industrial use, investing in a large tank will be more economical in the long run due to fewer refills.
Choosing the Right Argon Welding Tank
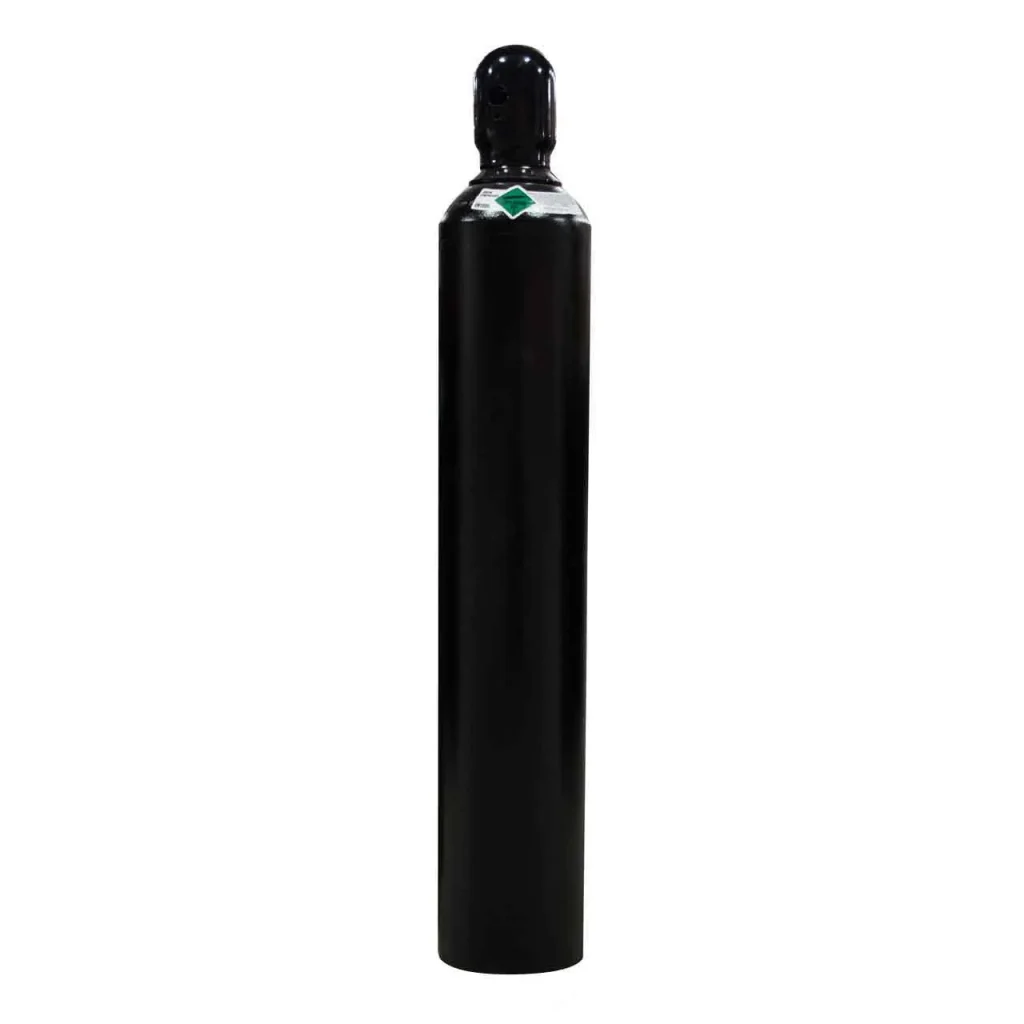
When selecting an argon welding tank, it’s important to consider the specific requirements of your welding projects. Key factors to evaluate include the frequency of use, project size and scope, and portability needs. Frequent welders, such as professionals or those with large-scale projects, will benefit from larger tanks, while hobbyists might find smaller tanks more convenient. Consider the size and complexity of the projects you will be working on. Larger projects that require continuous welding will need tanks with higher capacities to avoid frequent interruptions for refilling. If you need to move your welding equipment frequently, portability will be a significant factor. Aluminum tanks are lighter and easier to transport compared to steel tanks, making them suitable for mobile welders.
The cost of argon welding tanks can vary based on size, material, and brand. While larger tanks may have a higher upfront cost, they often prove more economical in the long run due to reduced refilling frequency. Calculate your expected usage to determine the most cost-effective option. Consider the cost of refilling the tank. Larger tanks may have higher refill costs, but the cost per cubic foot of gas is typically lower. Compare prices from different suppliers to find the best deal. Investing in a reputable brand can ensure better quality and safety. Cheaper tanks may save money initially but could lead to higher maintenance costs or safety issues down the line.
Choosing a reliable vendor is crucial for purchasing a high-quality argon welding tank. Look for suppliers with good reviews and a solid reputation in the industry. Recommendations from other welders or industry professionals can be valuable. Ensure the vendor provides tanks that comply with relevant standards and regulations. Ask for certification details to verify compliance. Good customer support can be vital, especially if you encounter issues with the tank. Choose a vendor that offers reliable support and has a clear return and warranty policy.
In addition to the argon welding tank itself, you will need a few essential accessories to get started. A regulator is necessary to control the flow of argon gas from the tank to the welding torch. Ensure you select a regulator compatible with your tank and welding setup. High-quality hoses and connectors are essential for ensuring a secure and leak-free connection between the tank and the welding equipment. Safety gear, such as welding helmets, gloves, and aprons, is crucial to protect yourself while welding.
Using Argon Welding Tanks Safely and Effectively
Proper use and maintenance of argon welding tanks are crucial for safety and efficiency. Always follow safety guidelines and best practices to ensure a safe working environment. Store argon tanks in a well-ventilated area, away from heat sources and direct sunlight. Secure tanks to prevent them from tipping over. Regularly inspect tanks, hoses, and regulators for leaks or damage. Use soapy water to check for leaks around connections. Always open the tank valve slowly to prevent pressure surges that can damage equipment.
Properly handling argon tanks during transportation is vital to avoid accidents. Secure tanks upright in a stable position and use protective caps on valve connections. When not in use, close the tank valve and release pressure from the regulator and hoses. Follow manufacturer guidelines for periodic maintenance and testing of tanks and equipment. Replace worn or damaged parts promptly to maintain safety and performance.
Common Applications and Benefits
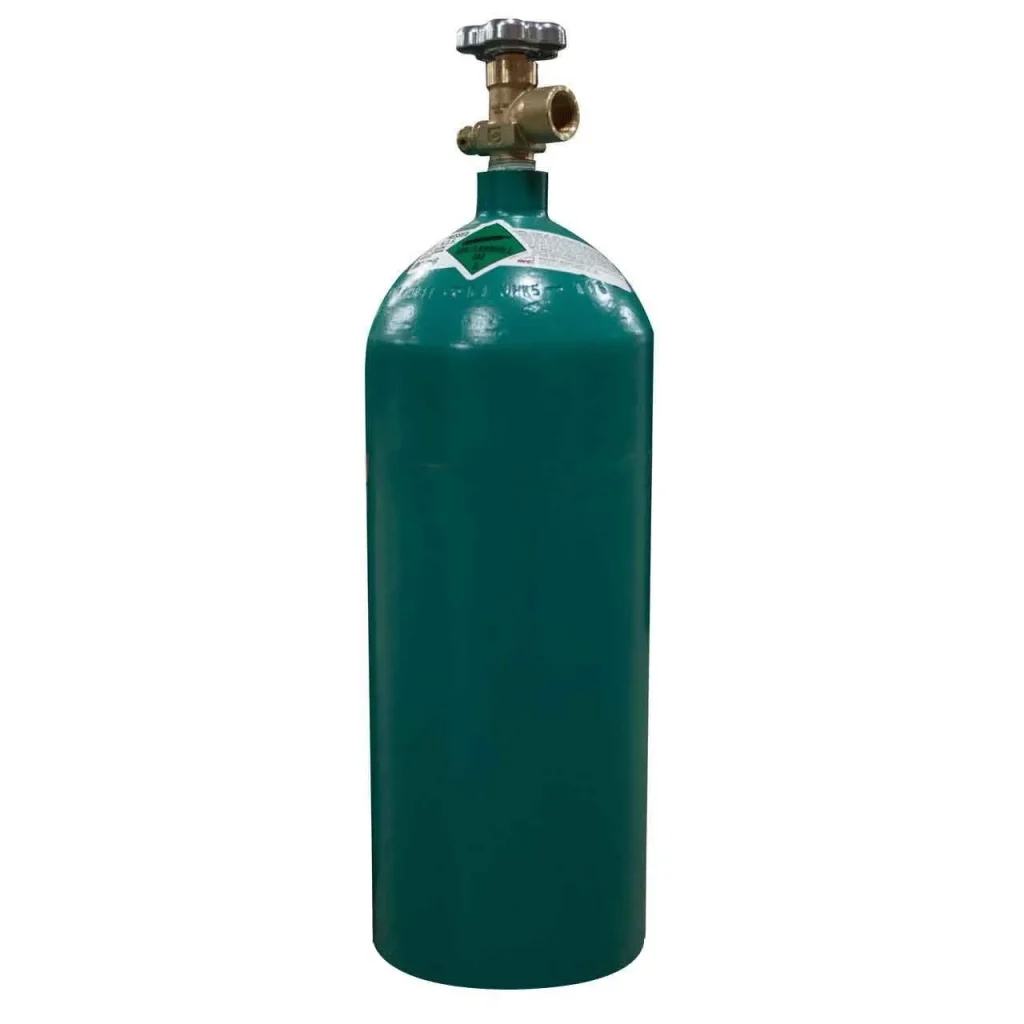
Applications
Argon welding is used across various industries due to its precision and high-quality results. Here are some common applications:
- Aerospace: In the aerospace industry, precision and strength are paramount. Argon welding is used for fabricating aircraft components, as it provides the necessary control and cleanliness required for high-performance parts.
- Automotive: Argon welding is widely used in the automotive industry for assembling and repairing vehicle parts. It is especially useful for welding thin materials and achieving clean, strong welds on body panels and frames.
- Manufacturing: Many manufacturing processes rely on argon welding for producing components that require high precision and durability. This includes the production of machinery, equipment, and metal structures.
- Art and Sculpture: Artists and sculptors use argon welding to create intricate metal artworks. The clean welds and precise control offered by argon make it ideal for detailed and aesthetically pleasing pieces.
- Construction: In construction, argon welding is used for tasks such as joining structural steel, fabricating metal frameworks, and installing piping systems. Its ability to produce strong, clean welds makes it suitable for critical structural applications.
Benefits
- Clean Welds: Argon creates a stable and inert atmosphere that prevents contamination from oxygen and nitrogen, resulting in clean and visually appealing welds. This is especially important for projects where appearance is crucial.
- Precision and Control: Argon welding allows for precise control over the welding process, making it ideal for intricate and detailed work. This precision is beneficial for tasks that require a high degree of accuracy.
- Versatility: Argon welding is suitable for a wide range of materials, including aluminum, stainless steel, and other non-ferrous metals. This versatility makes it a valuable tool for various welding applications.
- Strength and Durability: Welds produced with argon are strong and durable, ensuring the longevity and reliability of the welded components. This strength is essential for applications where the integrity of the weld is critical.
- Reduced Defects: The use of argon minimizes the risk of weld defects such as porosity and oxidation. This results in higher-quality welds that meet stringent industry standards.
By understanding and utilizing argon welding tanks effectively, welders can achieve superior results in their projects, whether they are working on small-scale hobbyist projects or large industrial applications.
Troubleshooting Common Issues
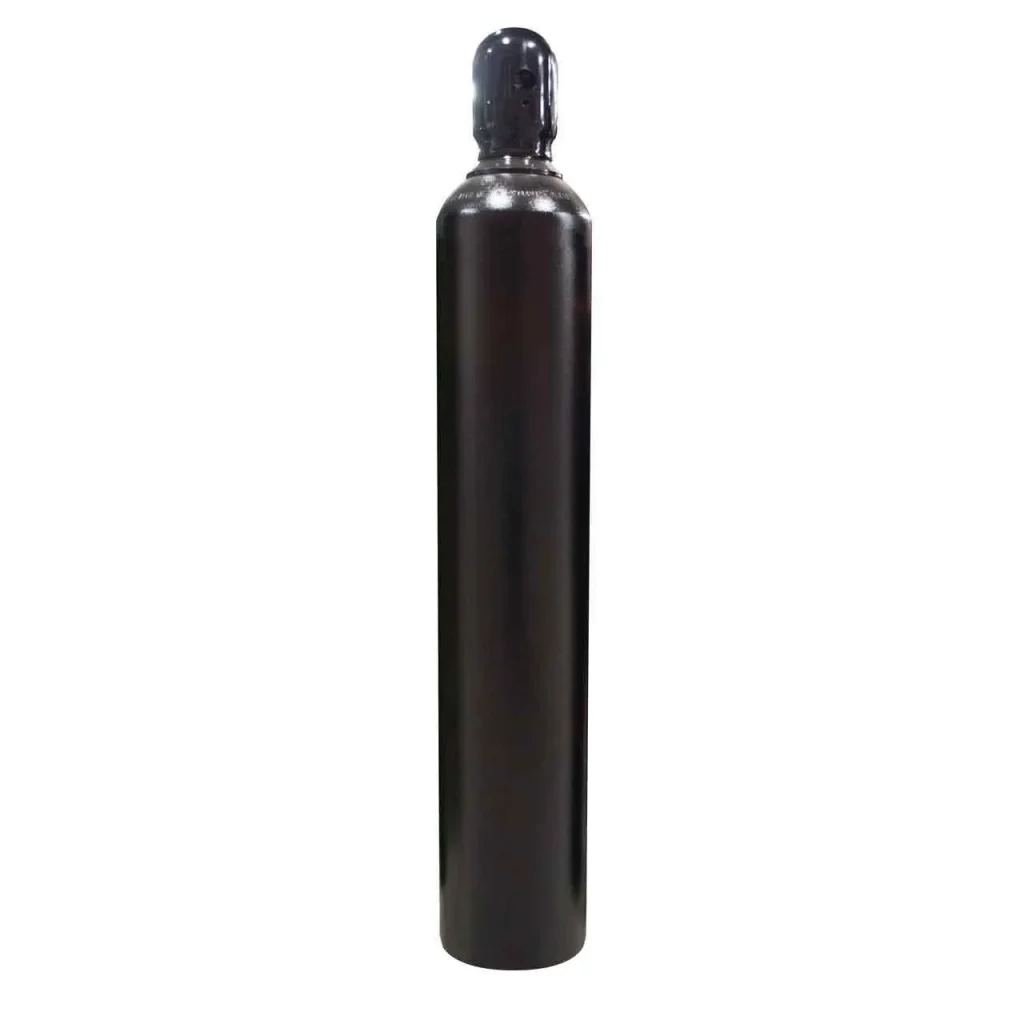
Even with the best equipment and practices, welders may encounter issues that can affect the quality of their welds. Here are some common problems and their solutions:
Inconsistent Gas Flow
- Symptoms: Unstable arc, porous welds, oxidation.
- Causes: Blocked or kinked hoses, malfunctioning regulator, low gas pressure.
- Solutions: Inspect hoses for kinks or damage and replace if necessary. Check the regulator for proper functioning and replace if defective. Ensure the tank is not empty or low on gas and refill if needed.
Contaminated Welds
- Symptoms: Welds with impurities, spatter, discoloration.
- Causes: Contaminated base metal, dirty or damaged electrode, inadequate shielding gas coverage.
- Solutions: Clean the base metal thoroughly before welding. Replace or clean the electrode if it is dirty or damaged. Ensure proper gas flow and adjust the regulator to maintain adequate coverage.
Poor Weld Penetration
- Symptoms: Weak welds, lack of fusion between materials.
- Causes: Low amperage settings, incorrect welding technique, insufficient gas flow.
- Solutions: Increase the amperage setting on the welding machine. Adjust your welding technique to ensure proper heat distribution. Check and adjust the gas flow rate to ensure adequate shielding.
Excessive Spatter
- Symptoms: Excessive metal droplets around the weld area.
- Causes: Incorrect settings, contaminated gas, improper technique.
- Solutions: Adjust the voltage and amperage settings to the recommended levels. Ensure the gas is pure and free from contaminants. Refine your welding technique to maintain a steady arc.
Weld Cracks
- Symptoms: Cracks appearing in the weld or surrounding material.
- Causes: High thermal stresses, incorrect filler material, inadequate preheat or post-weld treatment.
Solutions: Preheat the base material to reduce thermal stress. Use the correct filler material for the specific metal being welded. Implement proper post-weld heat treatment to relieve stress.
Advanced Tips for Argon Welding
Optimizing Gas Flow
- Flow Rate: Adjust the flow rate to the optimal level for your specific welding process. Too much gas can cause turbulence and poor weld quality, while too little can lead to contamination.
- Gas Coverage: Ensure the gas coverage is consistent and reaches all areas of the weld. Use gas lenses and proper nozzle sizes to improve gas distribution.
Electrode Preparation
- Sharpening: Sharpen the tungsten electrode to a fine point for precise welding. The shape of the electrode tip can significantly impact the arc stability and weld quality.
- Contamination Prevention: Avoid touching the electrode with bare hands or contaminated surfaces. Always handle with clean gloves and tools.
Welding Techniques
- Torch Angle: Maintain an appropriate torch angle to ensure proper gas flow and heat distribution. A 15-20 degree angle is usually recommended for most applications.
- Travel Speed: Adjust your travel speed to match the material and thickness. Too fast can cause incomplete fusion, while too slow can lead to excessive heat buildup and warping.
- Puddle Control: Pay close attention to the weld puddle and adjust your technique to maintain control. This is especially important when welding thin materials.
Equipment Maintenance
- Regular Inspections: Conduct regular inspections of all equipment, including the tank, regulator, hoses, and torch. Look for signs of wear, damage, or leaks.
- Cleaning: Keep all equipment clean and free from contaminants. Regularly clean the torch, nozzle, and electrode holder to ensure optimal performance.
- Calibration: Periodically calibrate your welding machine and gas regulator to maintain accurate settings and flow rates.
Conclusion
Argon welding tanks are a vital component in achieving high-quality welds across various industries. Understanding the proper use, maintenance, and selection of these tanks can significantly impact the success of your welding projects. By following the guidelines and tips provided in this guide, both beginners and experienced welders can enhance their skills and produce superior welds.
Whether you are working on small-scale hobby projects or large industrial applications, investing in the right argon welding tank and accessories, practicing safe handling, and mastering advanced techniques will ensure your welding operations are efficient, safe, and produce the desired results. Remember, the key to successful welding lies not only in the equipment but also in the knowledge and skills of the welder.
Leave a Reply