Introduction to TIG Welding
Tungsten Inert Gas (TIG) welding, also known as Gas Tungsten Arc Welding (GTAW), is a widely used welding process that employs a non-consumable tungsten electrode to produce the weld. This method is renowned for its precision and ability to create high-quality welds on a variety of metals, including non-ferrous materials like aluminum and magnesium, as well as thin sections of stainless steel. TIG welding is commonly used in industries such as aerospace, automotive, and metal fabrication due to its capability to produce clean, strong, and aesthetically pleasing welds.
The process involves generating an electric arc between the tungsten electrode and the workpiece, which melts the base metal and any filler metal used to create the weld joint. One of the key aspects that sets TIG welding apart from other welding methods is the use of a shielding gas, typically argon, to protect the weld area from atmospheric contamination. This shielding gas is critical in preventing oxidation and other defects that could compromise the integrity of the weld.
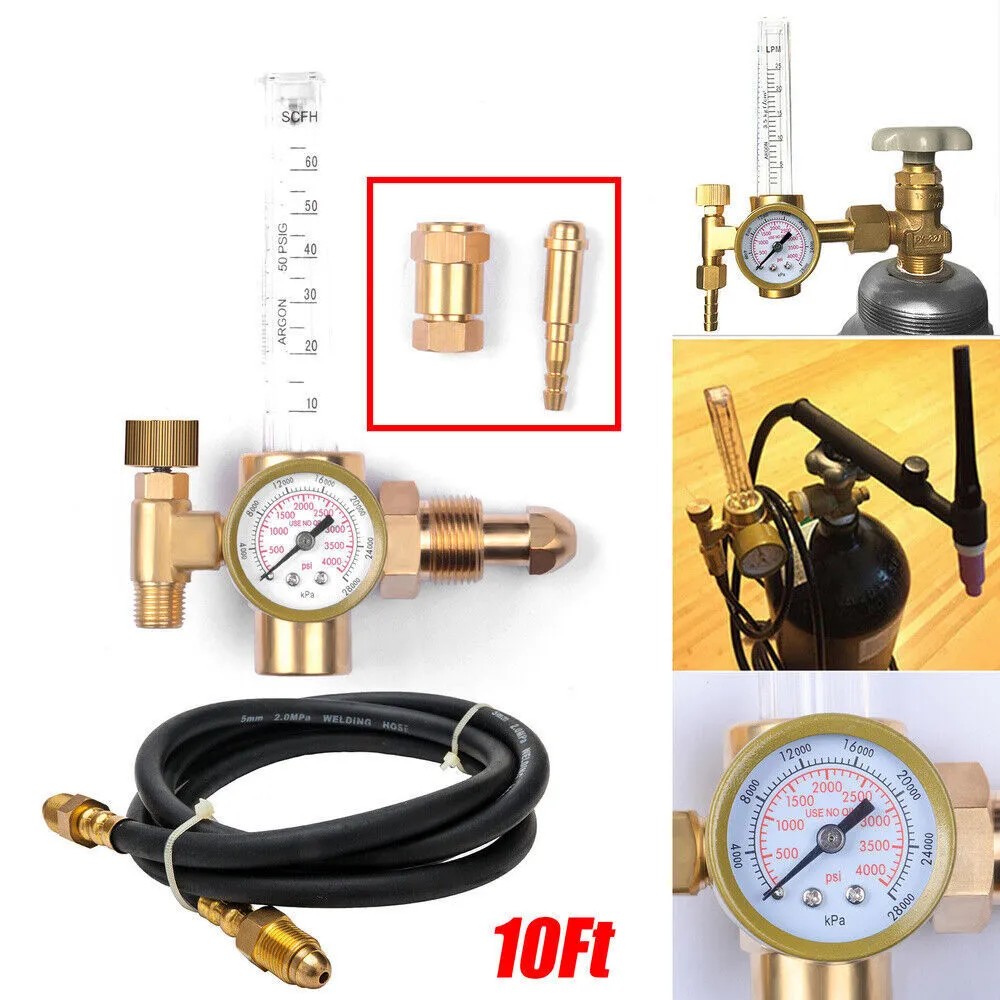
Importance of Argon in TIG Welding
Argon gas is essential in TIG welding for several reasons, which contribute to the overall quality and success of the welding process:
- Stable Arc Production: Argon helps maintain a consistent and stable arc, which is crucial for producing uniform welds. A stable arc ensures that the heat is evenly distributed across the weld joint, reducing the risk of defects and ensuring the weld’s integrity.
- Shielding from Contamination: The primary role of argon is to act as a shielding gas, protecting the weld area from atmospheric gases such as oxygen, nitrogen, and hydrogen. These gases can cause various defects, including oxidation, nitriding, and hydrogen embrittlement, which weaken the weld and lead to failures.
- Reduced Tungsten Erosion: Using argon helps reduce the erosion of the tungsten electrode. Tungsten erosion can lead to contamination of the weld pool and affect the quality of the weld. By minimizing electrode wear, argon ensures a cleaner and more stable welding process.
- Versatility: Argon is versatile and can be used with a wide range of metals and alloys. This makes it an ideal choice for various welding applications, providing welders with the flexibility to work on different projects without changing the shielding gas.
By providing a controlled environment, argon allows welders to achieve precise, high-quality welds. Its inert properties ensure that it does not react with the weld pool, preserving the weld’s purity and strength.
Ideal Argon Pressure Settings
Setting the correct argon pressure is crucial for achieving optimal results in TIG welding. The right argon flow rate ensures a stable arc, adequate shielding, and high-quality welds. Here are some general guidelines for argon pressure settings in TIG welding:
- Standard Argon Pressure: For most TIG welding applications, an argon flow rate of 15-20 cubic feet per hour (CFH) is recommended. This standard setting provides a good balance between effective shielding and gas consumption. It ensures that the weld area is adequately protected from atmospheric contamination, resulting in clean and strong welds.
- Low-Pressure Applications: When welding thin materials or performing precision work, reducing the argon flow to 10-15 CFH can be beneficial. Lower flow rates help prevent excessive turbulence and potential weld defects. This is particularly important when working with delicate or thin materials, where too much gas flow can disturb the molten weld pool and cause irregularities.
- High-Pressure Applications: For thicker materials or situations requiring increased shielding, argon flow rates can be adjusted to 20-30 CFH. Higher flow rates ensure that the weld area is fully protected, especially in challenging conditions such as outdoor welding or environments with drafts. This helps maintain the weld’s integrity and prevents defects caused by contamination.
These guidelines provide a starting point for setting argon pressure, but adjustments may be necessary based on specific welding conditions and objectives. It’s essential to monitor the weld and make changes as needed to achieve the best results.
Factors Affecting Argon Pressure
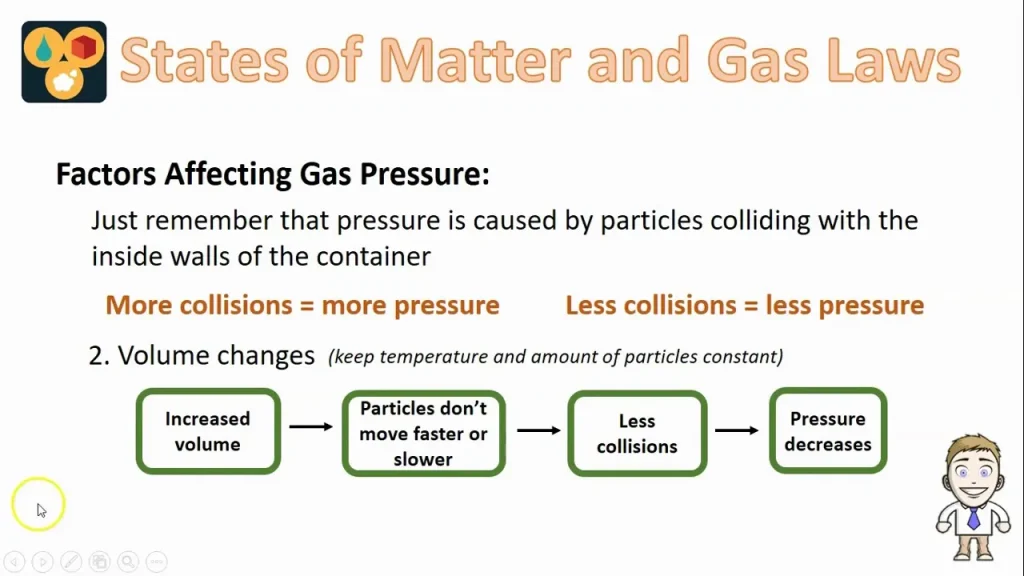
Several factors can influence the optimal argon pressure settings in TIG welding. Understanding these factors can help welders make informed adjustments to achieve the best possible weld quality.
- Material Thickness:
- Thin Materials: When welding thin materials, lower argon flow rates (10-15 CFH) are often sufficient. Excessive gas flow can create turbulence and lead to weld defects such as porosity or burn-through.
- Thick Materials: Thicker materials require higher argon flow rates (20-30 CFH) to ensure adequate penetration and shielding, maintaining the integrity of the weld.
- Joint Configuration:
- Simple Joints: For straightforward joints, standard argon pressure settings are typically adequate. A consistent flow rate ensures uniform coverage and protection of the weld area.
- Complex Joints: Welding complex or multi-pass joints may necessitate higher argon flow rates to ensure all areas of the weld are properly shielded. This is particularly important in joints with tight corners or intricate geometries where gas flow might be obstructed.
- Welding Environment:
- Indoor Welding: In controlled indoor environments, standard argon flow rates are generally sufficient. However, care must be taken to avoid drafts from ventilation systems that could disturb the shielding gas.
- Outdoor Welding: Outdoor welding or welding in drafty conditions may require increased argon flow to counteract the effects of wind and ensure consistent shielding. Using windbreaks or enclosures can help mitigate environmental impacts.
- Welding Position:
- Flat Position: In flat or horizontal welding positions, standard argon pressure settings usually work well. The gas naturally flows over the weld area, providing effective shielding.
- Vertical or Overhead Positions: Welding in vertical or overhead positions might require adjustments to the argon flow to maintain proper shielding and control of the molten weld pool. Higher flow rates or specific nozzle adjustments can help achieve better gas coverage.
- Electrode Size and Type:
- The size and type of tungsten electrode can also impact the required argon flow rate. Larger electrodes or those used for higher current settings might need higher argon flow rates to ensure adequate shielding. Conversely, smaller electrodes or low-current applications might benefit from reduced flow rates to prevent turbulence.
Tips for Optimizing Argon Pressure
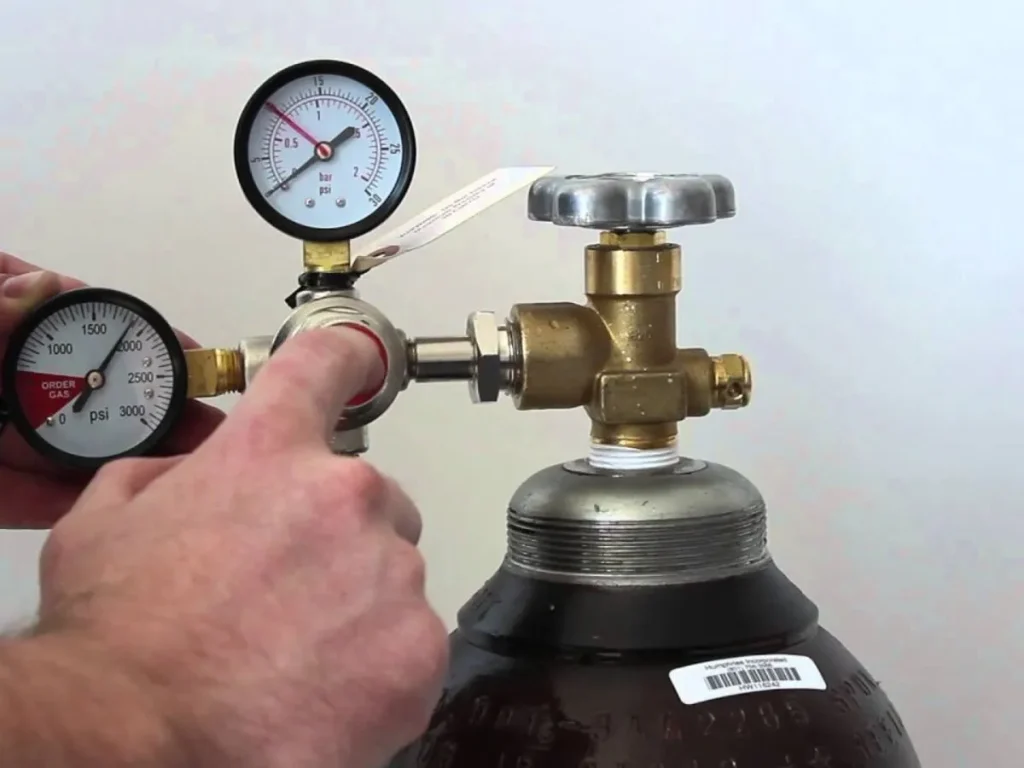
To achieve the best results in TIG welding, consider the following tips for optimizing argon pressure:
- Check for Leaks:
- Ensure there are no leaks in the gas lines or connections, as leaks can reduce argon pressure and compromise weld quality. Regularly inspect hoses, regulators, and connections for any signs of wear or damage. Use a leak detection solution or soapy water to check for bubbles indicating gas leaks.
- Monitor Flow Meter:
- Regularly check the flow meter to maintain the desired argon pressure. Fluctuations in the flow rate can lead to inconsistent welds. Ensure that the flow meter is functioning correctly and calibrated. An accurate flow meter is essential for precise control over the shielding gas flow rate.
- Adjust for Specific Applications:
- Tailor the argon pressure settings based on the specific welding task at hand. Fine-tuning the flow rate for different materials, joint configurations, and welding positions can significantly improve weld quality. For instance, use lower flow rates for thin materials to avoid turbulence and higher flow rates for thicker materials to ensure adequate shielding.
- Use a Gas Lens:
- Incorporating a gas lens can help achieve a more laminar gas flow, reducing turbulence and improving shielding effectiveness. A gas lens provides a smoother, more concentrated argon flow, which can enhance weld quality, especially in challenging positions. Gas lenses are particularly useful for welding in tight spaces or when using longer electrode extensions.
- Perform Test Welds:
- Conduct test welds to determine the optimal argon pressure settings for a given application. Adjust the flow rate based on the results and observations from the test welds to ensure the best possible performance during actual welding operations. Test welds help identify any issues with gas coverage, penetration, and overall weld quality before working on critical parts.
- Maintain Clean Equipment:
- Keep the welding torch and gas nozzles clean to ensure proper gas flow. Contaminants can obstruct the gas flow and affect the quality of the shielding. Regularly inspect and clean the torch components to prevent blockages and maintain optimal gas coverage.
- Use Appropriate Nozzle Size:
- Choose the right size nozzle for the welding application. Larger nozzles provide better gas coverage for larger weld areas, while smaller nozzles are suitable for more precise work. The nozzle size should match the electrode size and the specific requirements of the welding task.
- Consider Environmental Factors:
- In outdoor or drafty environments, use windbreaks or welding enclosures to protect the weld area from wind and drafts. Environmental factors can significantly impact the effectiveness of the shielding gas, so taking precautions to mitigate these influences is essential.
By following these tips, welders can optimize argon pressure settings, ensuring consistent and high-quality welds.
Common Issues with Argon Pressure in TIG Welding
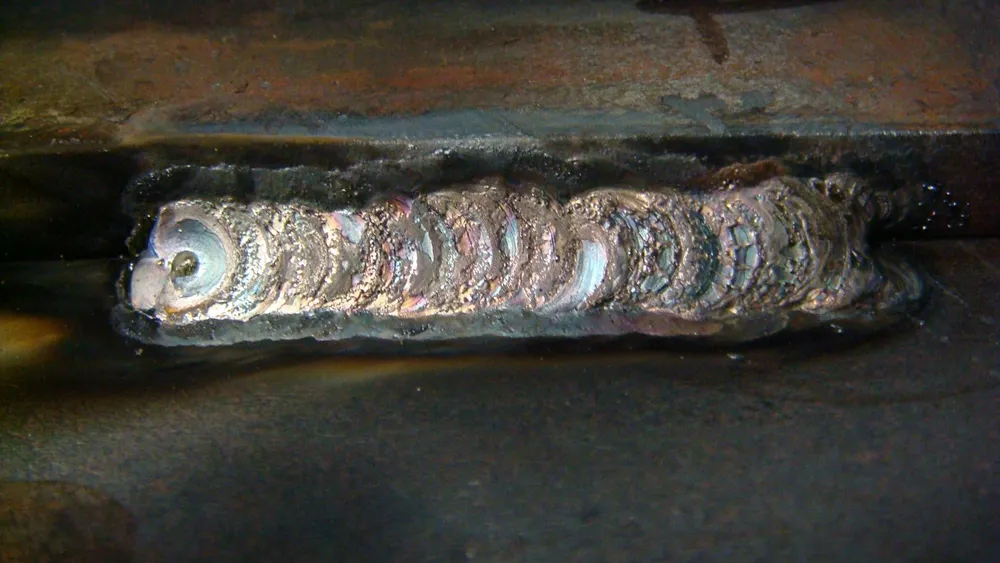
Several common issues can arise if argon pressure is not properly managed in TIG welding. Being aware of these issues can help welders take proactive steps to avoid them:
- Porosity:
- Insufficient argon pressure can lead to porosity in the weld, causing weak points and potential failure. Ensure adequate argon flow to prevent atmospheric contamination, which can introduce gases into the weld pool and create pores.
- Oxidation:
- Low argon flow can result in oxidation, especially when welding reactive metals like aluminum. Oxidation can weaken the weld and cause surface defects. Maintaining proper argon flow is crucial to preventing oxidation and ensuring a clean, strong weld.
- Excessive Spatter:
- Too high argon pressure can cause excessive spatter and turbulent flow, affecting weld appearance and quality. Adjust the flow rate to achieve a smooth, stable arc and minimize spatter.
- Inconsistent Welds:
- Fluctuations in argon pressure can lead to inconsistent welds, with variations in penetration and appearance. Regularly monitor and adjust the flow rate to maintain consistency and ensure uniform weld quality.
- Tungsten Contamination:
- Improper argon pressure settings can lead to tungsten contamination, where particles from the electrode get into the weld pool. This contamination can cause weld defects and reduce the overall strength of the weld. Proper gas flow helps protect the tungsten electrode and minimize contamination.
- Arc Instability:
- Arc instability can occur if the argon pressure is too low or too high. Low pressure may result in a weak and fluctuating arc, while high pressure can cause excessive turbulence and arc wandering. Both scenarios make it challenging to maintain a consistent weld bead and can result in defects.
- Weld Discoloration:
- Inadequate argon shielding can cause weld discoloration, particularly when welding stainless steel or titanium. Discoloration indicates oxidation, which can compromise the weld’s corrosion resistance and mechanical properties. Ensuring sufficient argon flow prevents atmospheric contamination and maintains the desired weld appearance.
- Overheating of the Tungsten Electrode:
- Incorrect argon flow can lead to overheating of the tungsten electrode. Overheating can cause the electrode to degrade faster, leading to frequent replacements and potential contamination of the weld pool. Optimal argon flow helps regulate the temperature of the electrode, extending its lifespan and maintaining weld quality.
Conclusion
Understanding and correctly setting argon pressure is essential for successful TIG welding. By considering factors such as material thickness, joint configuration, welding environment, and electrode size, welders can optimize argon flow to achieve clean, strong, and aesthetically pleasing welds. Regular monitoring and adjustments will ensure consistent results and prolong the life of welding equipment.
This comprehensive guide provides the foundation for mastering argon pressure settings in TIG welding, helping welders achieve professional-quality results in their projects.
Leave a Reply