In the realm of metal fabrication and repair, welding stands out as a fundamental process. Among the various welding techniques, wire welding machines have gained significant prominence due to their efficiency and versatility. This article explores the five outstanding advantages of wire welding machines, offering a thorough understanding of their benefits and applications.
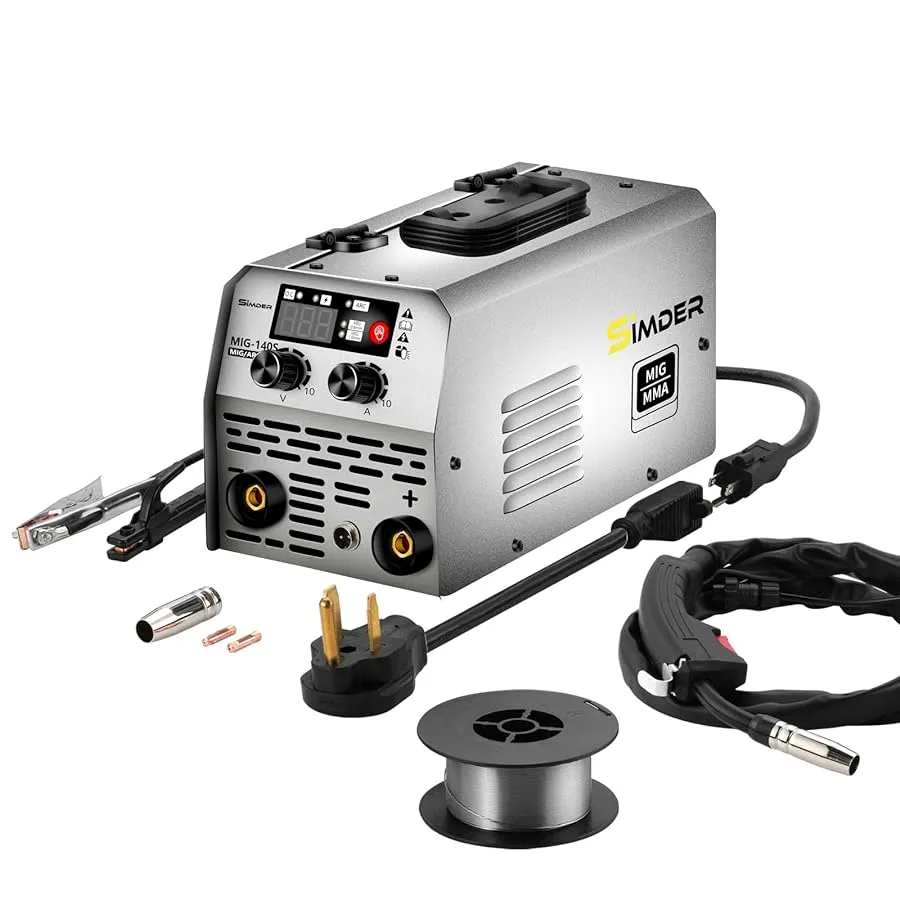
Increased Efficiency and Speed
Wire Welding Machine
A wire welding machine, often known as a wire-feed welder, is designed to automate the welding process, making it faster and more efficient than traditional methods. The continuous feed of wire ensures that the welder can maintain a constant arc, reducing downtime associated with changing electrodes.
Advantages in Speed
- Continuous Operation: Unlike stick welding, where the welder must frequently stop to replace electrodes, wire welding allows for continuous operation. This uninterrupted workflow significantly increases productivity.
- Higher Deposition Rate: Wire welding machines typically have a higher deposition rate, meaning more metal is deposited in a shorter amount of time. This is particularly beneficial in large-scale manufacturing settings where speed is crucial.
Consistency and Quality
- Automated Control: The automation in wire welding machines ensures consistent wire feed and arc length, resulting in uniform welds. This consistency is vital for maintaining high-quality standards in production.
- Reduced Human Error: By minimizing the need for manual intervention, wire welding machines reduce the likelihood of human error, leading to more precise and reliable welds.
Versatility in Welding Applications
MIG Wire Welding Machine
Metal Inert Gas (MIG) welding, also known as Gas Metal Arc Welding (GMAW), is one of the most common types of wire welding. A MIG wire welding machine uses a continuous solid wire electrode fed through a welding gun and into the weld pool, joined with a shielding gas to protect the weld from contamination.
Advantages in Versatility
- Range of Materials: MIG welding is suitable for a wide range of materials, including carbon steel, stainless steel, and aluminum. This versatility makes it an excellent choice for various industries, from automotive to aerospace.
- Thickness Variability: Whether dealing with thin sheet metal or thicker structural components, MIG wire welding machines can handle different material thicknesses with ease. This adaptability is crucial for projects requiring diverse welding needs.
Ease of Use
- Beginner-Friendly: MIG welding is often recommended for beginners due to its relatively simple operation. The automated wire feed and straightforward setup allow new welders to achieve satisfactory results with minimal training.
- Clean and Efficient: The use of inert gas in MIG welding reduces the amount of slag and spatter, resulting in cleaner welds and less post-weld cleanup. This efficiency is a significant advantage in maintaining a tidy and safe workspace.
Enhanced Welding Quality
Flux Cored Wire Welding Machine
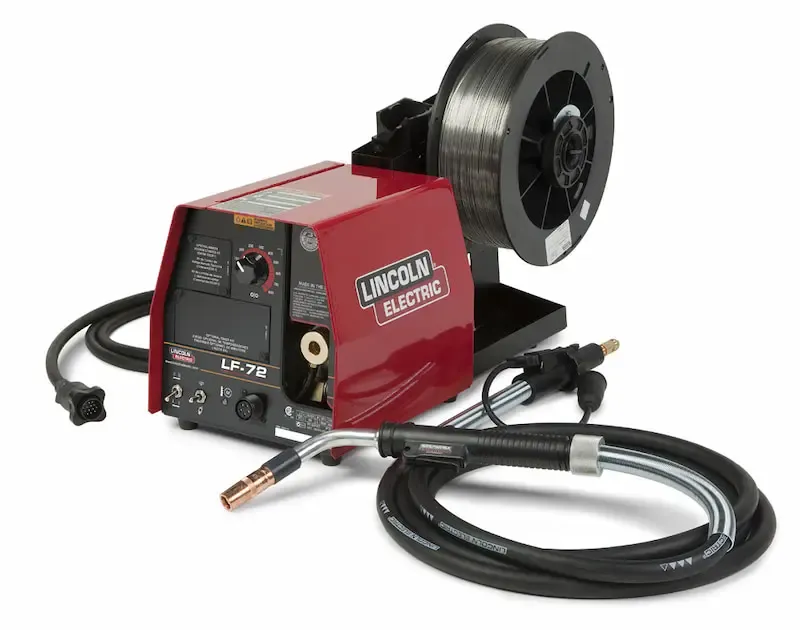
Flux Cored Arc Welding (FCAW) uses a flux cored wire welding machine, which combines the benefits of stick welding and MIG welding. The wire used in FCAW has a flux core that generates shielding gas, eliminating the need for an external gas supply in some cases.
Advantages in Welding Quality
- Deep Penetration: Flux cored wire welding machines provide deep weld penetration, making them ideal for thick materials and heavy-duty applications. This deep penetration ensures strong, durable welds that can withstand significant stress.
- All-Position Welding: FCAW is suitable for all welding positions, including flat, horizontal, vertical, and overhead. This flexibility allows welders to tackle complex projects with varying joint configurations.
Adaptability to Outdoor Conditions
- Wind Resistance: Unlike MIG welding, which requires a shielding gas that can be disrupted by wind, flux cored wire welding can be performed in outdoor environments with less concern for wind interference. This makes FCAW a preferred choice for construction and field repairs.
- Excellent for Dirty or Contaminated Metals: The flux core in the wire helps to clean the welding surface, making FCAW effective for welding on dirty, rusty, or contaminated metals. This self-cleaning action enhances the overall quality and integrity of the welds.
Cost-Effectiveness
Initial Investment and Operational Costs
- Affordable Equipment: Wire welding machines, especially MIG and flux cored wire welding machines, are generally affordable compared to other advanced welding technologies. This lower initial investment makes them accessible to small businesses and hobbyists.
- Consumables and Maintenance: The consumables for wire welding, such as wire spools and shielding gas, are reasonably priced and widely available. Additionally, the maintenance requirements for wire welding machines are minimal, contributing to lower operational costs.
Labor Savings
- Reduced Training Time: The ease of use associated with wire welding machines translates to reduced training time for new welders.Companies can quickly bring new employees up to speed, reducing downtime and increasing productivity.
- Higher Productivity: With the increased speed and efficiency of wire welding machines, production cycles are significantly reduced. This allows manufacturers to meet tight deadlines and handle larger volumes of work without compromising quality.
- Labor Efficiency: The automation and ease of operation reduce the physical strain on welders, enabling them to work more efficiently and for longer periods. This not only boosts productivity but also contributes to a safer and more ergonomic workplace.
Advanced Technological Features
Innovations in Wire Welding Machines
Modern wire welding machines are equipped with advanced technological features that further enhance their performance and usability. These innovations make wire welding more accessible and efficient for both novice and experienced welders.
Digital Controls and Interfaces
- Precision Settings: Many wire welding machines now come with digital controls that allow for precise adjustments of welding parameters. Welders can fine-tune settings such as wire feed speed, voltage, and amperage to match specific project requirements.
- User-Friendly Interfaces: Advanced machines often feature intuitive interfaces with touchscreens and programmable memory settings. These interfaces make it easier to set up and recall preferred welding configurations, saving time and improving consistency.
Advanced Safety Features
- Thermal Overload Protection: To prevent overheating and damage to the machine, many wire welding machines are equipped with thermal overload protection. This feature automatically shuts down the machine if it reaches unsafe temperature levels, protecting both the equipment and the operator.
- Automatic Arc Control: Advanced arc control technologies help maintain a stable arc, even in challenging conditions. This stability results in smoother, more consistent welds and reduces the risk of defects.
Portability and Flexibility
- Compact Designs: Wire welding machines are available in compact and portable designs, making them easy to transport and use in various locations. This portability is particularly beneficial for fieldwork and on-site repairs.
- Multi-Process Capabilities: Some wire welding machines are designed to support multiple welding processes, such as MIG, TIG, and Stick welding. This versatility allows welders to switch between different techniques as needed, using a single machine.
Detailed Comparison: MIG Wire Welding Machine vs. Flux Cored Wire Welding Machine
Understanding the specific advantages of different types of wire welding machines can help in selecting the right equipment for various applications. Here, we compare the key features and benefits of MIG wire welding machines and flux cored wire welding machines.
MIG Wire Welding Machine
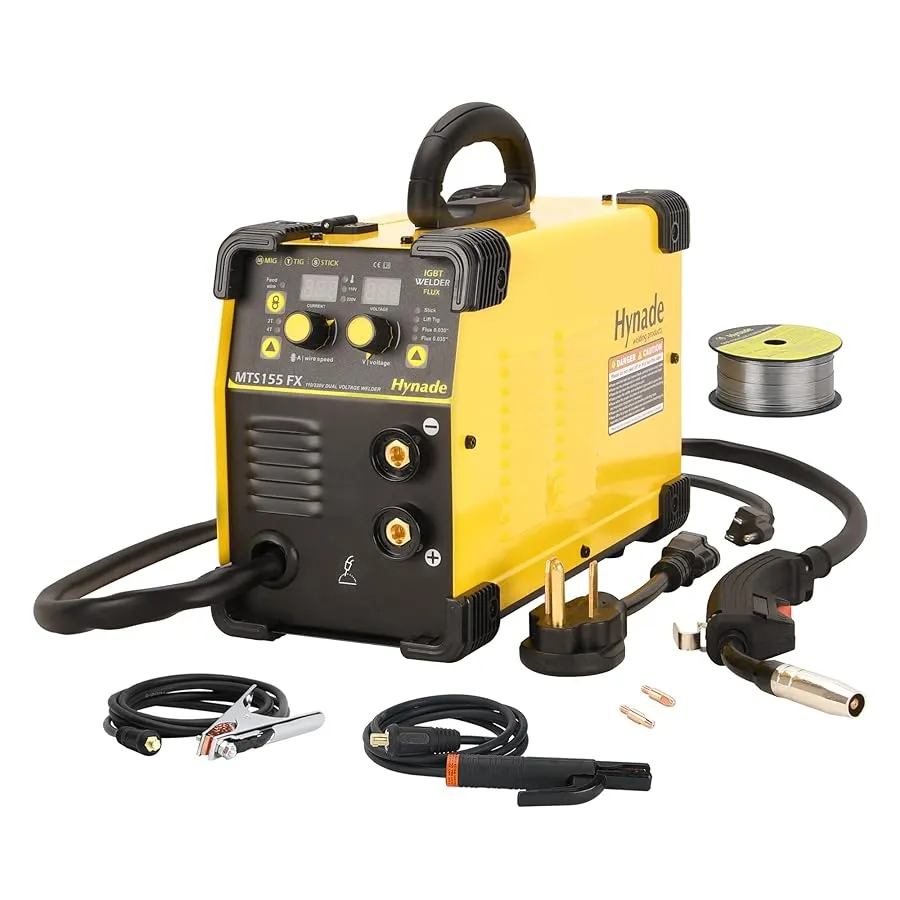
MIG welding is renowned for its ease of use and clean welds. It’s a preferred method for many applications due to its versatility and efficiency.
Advantages
- Ease of Use: Ideal for beginners, MIG welding’s straightforward operation makes it accessible to those new to welding.
- Clean Welds: MIG welding produces less slag and spatter, resulting in cleaner welds that require minimal cleanup.
- Speed: The continuous wire feed mechanism allows for faster welding speeds, increasing productivity.
- Versatility: Suitable for a wide range of materials, including thin metals and aluminum, MIG welding is highly adaptable to different projects.
Applications
- Automotive Repair and Manufacturing: MIG welding is commonly used in car body repair and the manufacturing of automotive parts.
- Fabrication of Light to Medium Structures: From furniture to light structural components, MIG welding is favored for its precision and clean finish.
- Artistic and Decorative Projects: The clean welds and ease of use make MIG welding a popular choice for artistic metalwork.
Flux Cored Wire Welding Machine
Flux cored arc welding is particularly effective for heavy-duty applications and challenging environments. Its ability to handle thicker materials and outdoor conditions makes it a robust choice for construction and industrial projects.
Advantages
- Deep Penetration: Flux cored welding provides deep weld penetration, making it suitable for thick materials and heavy-duty applications.
- All-Position Welding: Capable of welding in all positions, FCAW is flexible for various joint configurations.
- Outdoor Suitability: The flux core generates its own shielding gas, making it resistant to wind and ideal for outdoor work.
- Effective on Contaminated Metals: The flux helps clean the welding surface, allowing for effective welding on dirty, rusty, or contaminated metals.
Applications
- Construction and Infrastructure: FCAW is widely used in the construction of buildings, bridges, and other infrastructure due to its strength and reliability.
- Heavy Equipment Repair: The method is ideal for repairing heavy machinery and equipment, where thick materials and robust welds are required.
- Shipbuilding: The deep penetration and all-position capabilities make FCAW suitable for the demanding requirements of shipbuilding.
Real-World Impact and Case Studies
Case Study: Automotive Industry
In the automotive industry, the shift to wire welding machines, particularly MIG welding, has revolutionized the manufacturing and repair processes.
Leave a Reply